近几年,集成电路制造获得快速发展,随着器件技术的进步和器件尺寸的缩小,高级逻辑器件如微处理器(MPU)和数字信号处理器(DPU)等需更高的运行速度,这就要求其内部导线电阻更小,能传送更大的电流密度。为此,逻辑器件的内部导线材料由铝替换为铜,虽然铜有更好的导电、导热性,但也带来了新问题:Cu元素能快速地扩散到硅(SiO2)中破坏绝缘层。为防止Cu扩散,集成电路导线槽底部和侧面的阻挡层不能再使用原来的氮化钛材料,目前使用的是Ta和TaN薄膜,而此类薄膜由钽靶通过PVD方法溅射形成。
稀有金属钽具有高熔点(2996℃)、高密度(16.6g/cm3)以及优异的塑性和耐腐蚀性,其两次退火间的总加工率可达到95%以上,且纯度越高,塑性越好,因此钽是极易进行塑性加工的材料。溅射用靶材通常有板状和管状(又称柱状),用于集成电路制造的钽靶材通常为板状,又分为圆板靶和方板靶。板状钽靶材一般是通过将真空电子束熔炼的高纯钽锭进行塑性加工和真空退火得到。目前,对PVD用钽靶材的研究主要集中在钽靶材晶粒度和织构对其溅射性能的影响方面。溅射靶材的晶粒度越细小、越均匀,溅射速率越快,薄膜厚度越均匀;晶体取向越趋于一致,溅射时薄膜沉积速率越快,薄膜均匀性越好[1]。然而,在实际生产中由于铸锭原始组织和塑性变形的不均匀性,要得到晶粒尺寸细小而均匀的组织并不容易,特别是要得到晶体取向趋于一致的组织更加困难。本文根据国内外研究结果对溅射用钽靶材的性能要求进行了分析,并通过试验对钽靶材的制备和微观组织进行研究。
1、晶粒度和织构对钽靶材溅射产出率的影响
国内不少学者对钽靶材的性能要求进行了研究。钟景明等[2]研究认为,对于65nm、45nm及以下芯片制程而言,有的溅射机台要求钽靶材具有{100}、{111}织构组分的体积分数为20%~35%、{110}织构组分比例尽量少的组织,有的溅射机台要求钽靶材具有{111}织构占优的组织,有的溅射机台要求钽靶材具有{100}织构占优的组织。郝小雷[3]研究认为,溅射靶材的晶粒大小和晶粒取向直接影响其溅射性能和溅射薄膜的品质,主要表现在随着晶粒尺寸的增大,薄膜沉积速率呈现逐渐降低的趋势。靶材的平均晶粒尺寸和晶粒尺寸的均匀性是影响靶材溅射性能的要素之一。极大规模集成电路用半导体溅射靶材不仅要具有合适的晶粒尺寸,还要保证其均匀性。宜楠等[4]研究认为,钽靶材晶粒尺寸应小于100μm,再结晶率达到95%以上,且在靶材整个厚度范围内应以(111)织构为主。刘宁等[5]研究认为钽靶材的晶粒尺寸一般要求控制在50~80μm左右,均匀性控制在±10μm以内。以上研究虽然指出晶粒度和织构对溅射后沉积的薄膜性能均有影响,但是对于哪一个因素的影响更大以及何种组织和织构最有利于钽靶材溅射后的沉积并没有给出明确的答案。国外学者在这方面的研究则更加系统,特别是对于钽的溅射产出率方面的研究更加深入。
美国Cabot公司的ZHANG等[6]对(110)织构占优和(111)织构占优的大晶粒钽靶材进行了溅射试验,结果表明:近(111)取向的晶粒具有较低的溅射产出率,近(110)取向的晶粒具有较高的溅射产出率,(110)取向(垂直于氩离子入射方向)的溅射产出率是(111)取向的2倍。但该试验并未研究(100)织构占优的钽靶材的溅射产出率,也就不能比较(111)织构占优和(100)织构占优的钽靶材溅射产出率。
MICHALUK[7]研究了钽的晶体取向和晶粒度与钽靶材的物理溅射表现的关系,结果表明:细小均匀的晶粒度和良好的晶体取向可以增强钽的沉积性能,控制显微组织和织构的均匀性是确保钽靶材可靠性和随后溅射沉积得到良好薄膜的关键;保持织构不变,减小晶粒度可提高钽靶材的溅射产出率或沉积率,而保持晶粒度不变,改变钽靶材溅射表面的晶体取向也能影响沉积率;从(111)占优的织构变为随机的(111)-(100)织构并没有影响钽的溅射表现,即(111)占优织构与随机的(111)-(100)混合织构的溅射产出率相当;对于钽的溅射产出率而言,改变晶粒度比改变织构产生的影响更为显著;晶粒度对薄膜质量的影响是晶体取向和溅射产出率(以每个离子溅射出的原子数量表示)之间影响关系的延伸。
溅射产出率S(hkl)的概念被MAGNUSON和CARLSON[8]首次提出:

式中:K(hkl)表示体系的系数,E1/2表示入射离子能量的平方根,Pc(hkl)表示入射离子在垂直于(hkl)晶面方向运动后到达靶材表面与其原子发生碰撞的可能性(概率)。对于面心立方(fcc)晶体,具有最大表面自由原子密度(free atom surface density,FASD)的晶体取向其溅射产出率最大,因此S(111)>S(100)>S(110);而对于体心立方晶体(bcc),溅射产出率与晶体取向的关系也可以根据表面自由原子密度推导[8]。钽金属中三个低指数晶面(110)、(100)和(111)的原子密度分别为2.8/a2、2.0/a2和1.7/a2[7],由此可见,钽的溅射产出率与晶体取向之间的关系可能为S(110)>S(100)>S(111)。虽然对于bcc金属溅射性能的研究未达到fcc金属的程度,但对于bcc多晶体靶材溅射沉积物的研究结果[9-13]支持了这种关系。
MICHALUK的研究[7]还表明:钽中的(100)织构带是抗溅射的,且钽中(111)织构的沉积率稍强于(100)织构,即实际的溅射产出率与晶体取向之间的关系为S(110)>S(111)>S(100);(100)织构带之所以抗溅射,不是因为其织构特性,而是因为其具有较大的有效晶粒度;局部集中存在的(100)织构通常会形成条带织构或称带状组织;(100)织构带具有小角度晶界,这种小角度晶界不利于钽的溅射。CLARK等[14]认为(100)织构可能遗传于原始铸锭中的大柱状晶。
钽是bcc金属,最密排面是{110},最密排方向是<111>。MICHALUK的另一项研究[15]表明,钽的加工态和再结晶态均不能得到{110}为主的织构,而是主要由{100}织构和{111}织构组成,很少有{110}织构出现;钽靶材表层主要以{100}织构为主,而靶材厚度中心则以{111}织构为主,这种织构分布不均匀不利于靶材的溅射;钽的晶粒度与织构间有独特的联系:{111}织构为主的加工钽材由细小而均匀的晶粒组成,而具有大的再结晶或多边形晶粒的钽材为{100}织构,这种织构与加工产品在厚度方向上具有显微组织和织构不均性密切相关。采用目前的加工工艺生产的钽靶材还易存在织构在靶材厚度方向上分布不均匀的问题。
通过以上分析可以得出,最有利于溅射后沉积的钽靶材应具备以下特点:(1)晶粒细小而均匀,无带状组织;(2){111}占优织构或{100}-{111}混合随机织构均具备较好的溅射性能;(3)具有细小而均匀晶粒组织的{100}占优织构对溅射性能的影响也不大。实际上很难得到{100}织构占优且具备细小而均匀的晶粒组织,因为{100}织构的存在常伴随着带状或不均匀的大晶粒组织。
2、试验材料与方法
本试验所用高纯钽锭是将钽条经过真空电子束炉熔炼两次后所得,其机械加工尺寸为ϕ110mm×165mm,钽的纯度为大于99.95%,化学成分如表1所示。
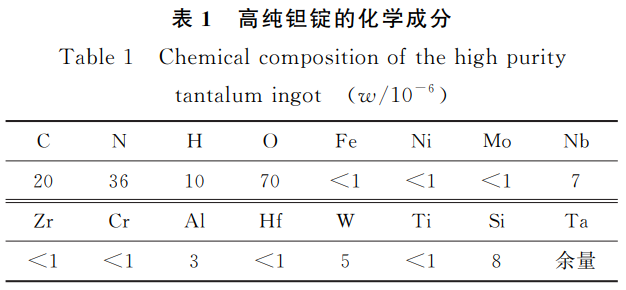
钽锭在室温下经过多次镦拔,总加工率达到了约96%,锻造后板坯尺寸约为60mm×162mm×162mm。锻造板坯经过950℃保温1h的真空退火后在四辊轧机上进行轧制,先进行交叉轧制,轧制至一定宽度后再沿一侧方向一直轧制至8.7mm厚,总加工率达到约85%。轧制板坯使用水刀切割成多块成品靶坯,再经过真空成品退火(在1050℃温度下保温1.5h)、校平、铣圆角和四边以及表面抛光处理后制成320mm×100mm×8mm的钽靶材成品。
如图1(a)所示,在成品靶材上连续截取3块试样,其中2块为金相试样,尺寸20mm×20mm×8mm,另一块为EBSD样,尺寸10mm×5mm×8mm。金相试样一块进行轧制面(RD-TD)试验,另一块进行侧面(RD-ND)试验,每一个试样的截面均采取标准金相制样方法处理,随后采用WY—20倒置金相显微镜观察金相组织。平均晶粒度分别在金相试样的轧制面和侧面上按照GB∕T6394—2017《金属平均晶粒度测定方法》采用截点法测定。EBSD试样经过标准的制样方法处理后尺寸大小为10mm×3mm×8mm,采用GeminiSEM300场发射扫描电子显微镜观察钽靶材的侧面(RD-ND),分别在图1(b)所示的A、B(靠近靶材轧制表面)以及C(靶材厚度中心)三个微区进行扫描,扫描步长控制为1.2μm。

3、试验结果与讨论
3.1金相组织及晶粒度
钽靶材试样的金相照片见图2。从图中可以看出,无论是钽靶材的轧制面还是厚度方向各处,均无明显的粗晶或细晶区,晶粒均细小而均匀且无带状组织。钽靶材各处平均晶粒度统计结果见表2。由表2可知,厚度方向近表面、1/4处和1/2处的晶粒度最大相差约4μm,平均值为27.30μm,与轧面的平均晶粒度相差0.11μm;厚度方向的最大晶粒度与轧面平均晶粒度相差约1.3μm;各处平均晶粒度级别为7~7.5级。
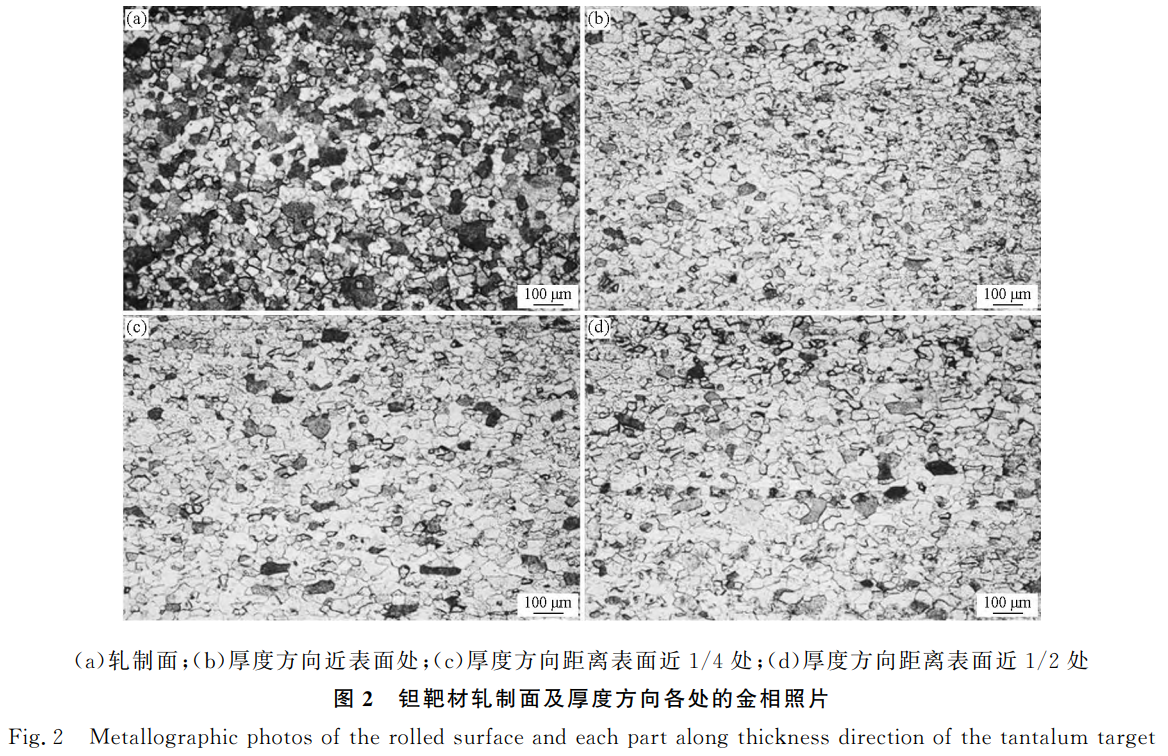
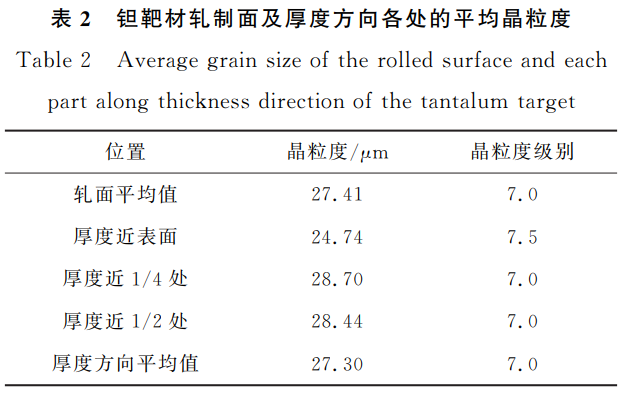
3.2织构
EBSD收集的数据采用AZtecCrystal软件进行分析,分别得到试样中A、B、C三区的极图和反极图、织构组成以及取向差角分布和晶粒尺寸分布,如图3~图5所示。
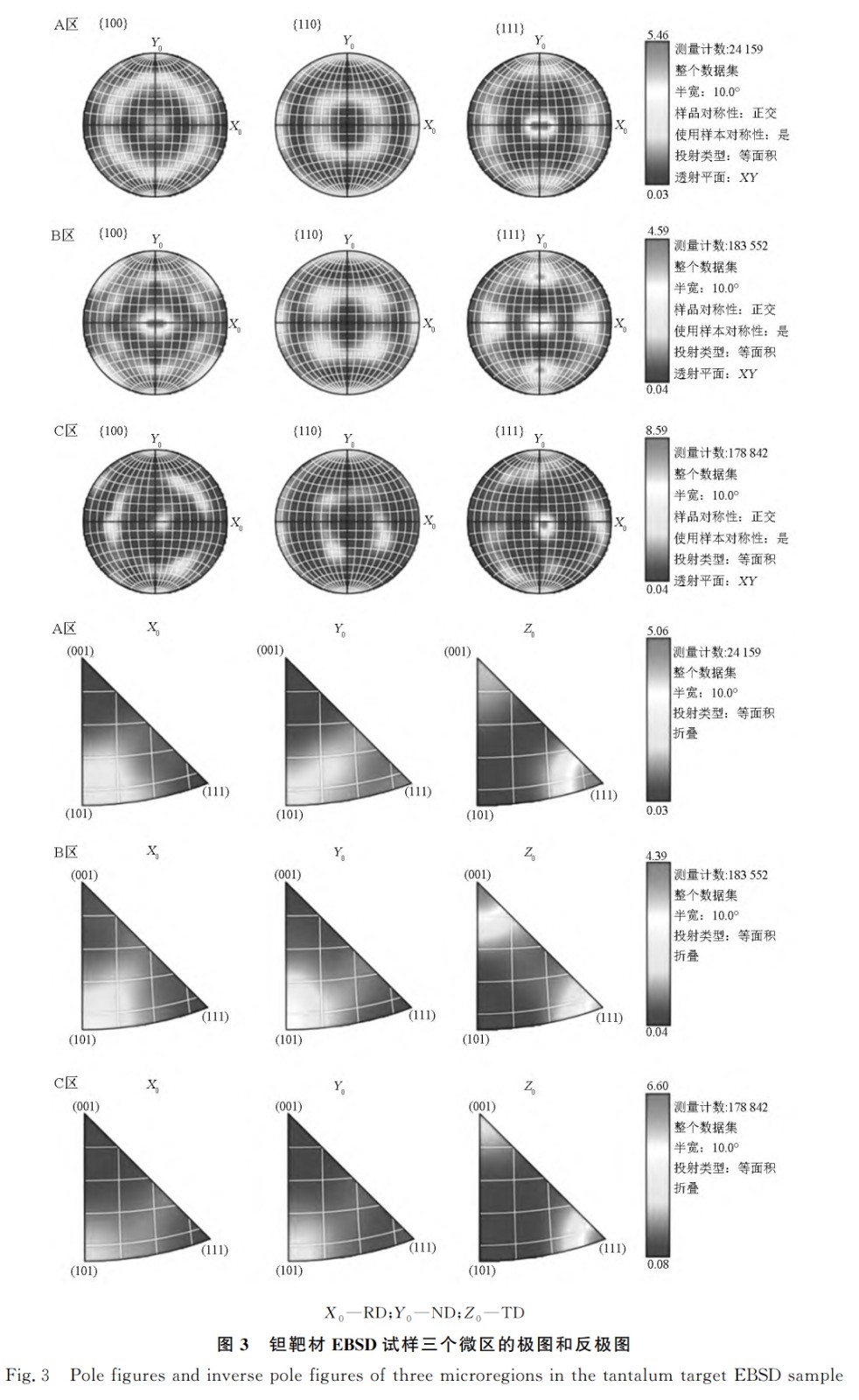
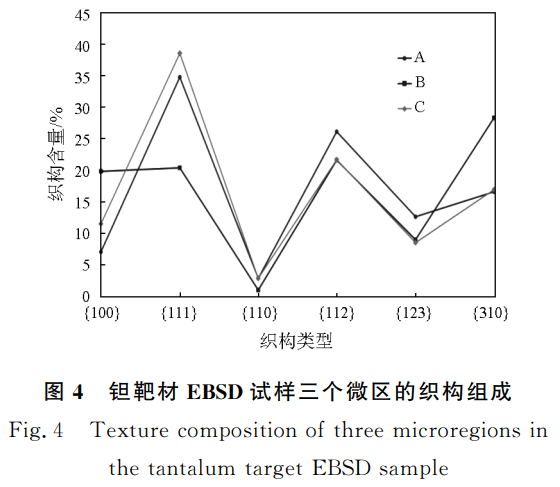
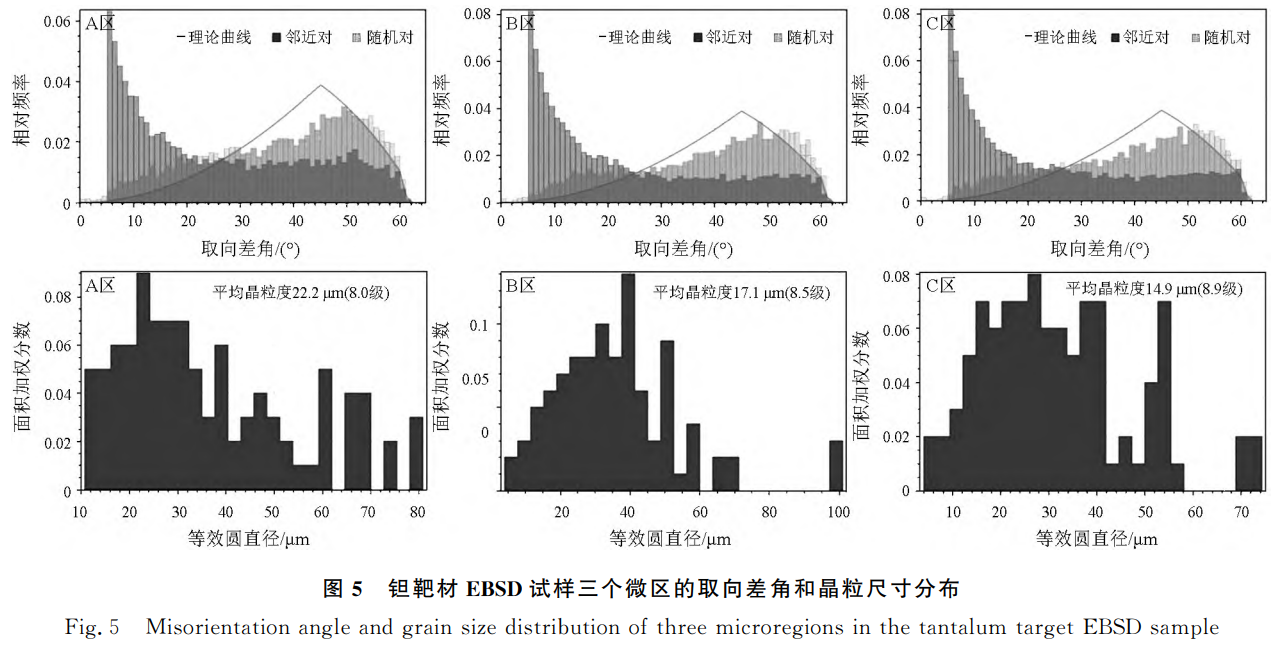
从图3可以看出,A区和C区的主要织构均为{111}和{100},且A区和C区两者的{111}和{100}织构的含量均接近;B区{100}和{111}也是主要织构,但A区和C区的{111}织构含量高于{100},而B区的{100}和{111}织构含量相当,可能与变形的不均匀性和再结晶退火不完全有关。钽单晶研究[16]显示,相比其他取向,{100}取向的晶粒加工硬化更小,再结晶更困难,而{111}取向的晶粒更易发生大量的再结晶。三个区的{110}织构含量均较低,可从图4所示各织构含量得到证实。在图4中,钽靶材含量较高的织构依次是{111}、{112}、{310}、{123}和{100},其中{111}织构的含量是{100}织构的3倍以上,前三种织构的含量均较高,比较符合织构随机分布的结论。A区与C区的织构类型和含量均相似,说明在钽靶材厚度方向上,无论是轧制面附近还是厚度方向中间处,其织构类型相似且分布均匀。
从图5所示取向差角分布可以看到,三个区的取向差角随机对分布与理论曲线相似度均很高,这说明三个区的晶粒取向呈随机分布[17];同时,10°以下取向差角的相对频率较高,说明存在大量小角度晶界的晶粒,这些晶粒有相同或相近的晶体取向。小角度晶界是由位错构成的,为位错的塞积区,大量小角度晶界的出现说明材料的再结晶程度并不完全。从图5所示晶粒尺寸分布可以看出,各区晶粒度分布较为均匀,大致呈正态分布;A、B、C区的平均晶粒度分别为22.2、17.1、14.9μm,对应的晶粒度级别分别达到了8.0级、8.5级和8.9级(ASTME2627标准)。
3.3高溅射产出率的钽靶材制备工艺探讨
真空电子束熔炼的高纯钽铸锭通常以粗大的柱状晶为主,柱状晶通常为{100}织构,其长度方向几乎平行于铸锭中心线,这种织构取向对于变形加工是极其不利的,也会对钽靶材成品的织构组成产生重要影响,因此铸锭开坯就显得极为重要。根据前面的分析,钽靶材的晶粒度大小和均匀性对其溅射产出率的影响比织构组成更为显著,故获得晶粒细小而均匀的组织是制备合格钽靶材的关键。相比于后续的轧制,铸锭的变形加工更容易改善组织,须制定最佳的铸锭变形工艺以获得具有良好组织结构的轧制坯。
纯钽具有良好的塑性,可以在室温下进行冷加工,因此本试验制定的开坯工艺选择在室温下进行多向锻造。为最大程度地破碎铸锭的柱状晶组织,须加大冷变形加工的变形量。多向锻造首先沿着铸锭中心线的方向进行镦粗,然后沿着铸锭中心线方向进行拔长,如此进行三次镦粗和两次拔长操作,最后一次沿着铸锭中心线镦粗至60mm厚。镦粗锻造对于铸锭柱状晶的破碎具有重要作用,增加镦粗的加工变形量有利于破碎柱状晶。CLARK等[14]研究认为,沿铸锭中心线锻造能破碎铸锭的柱状晶,为随后的退火创造大量的形核位点,从而有利于再结晶。沿径向锻造的轧制坯在后续轧制中的应变不能增加足够的变形量以消除铸锭的柱状晶。为此,本试验将钽铸锭锻造的总变形量增大到约96%,充分破碎了铸锭的柱状晶,同时弥补了后续轧制变形量的不足。
材料的变形加工须配合最佳的热处理工艺才能获得良好的组织和织构。锻造后的轧制坯应采取较低的中间退火温度,以形成部分再结晶或仅起到回复作用,从而为后续成品退火提供较大的储存能以增加更多的形核机会;而较高的中间退火温度会增加成品钽靶材晶粒粗化和尺寸不均匀的概率。
从本试验的结果来看,大变形量的铸锭锻造结合较低温度的中间退火工艺以及后续轧制和成品退火得到的钽靶材,其金相照片显示轧制面以及沿靶材厚度方向的晶粒细小而均匀且无带状组织,反映出钽靶材达到了完全再结晶,说明通过大变形量的铸锭锻造加工可以得到晶粒细小且均匀的组织。但EBSD分析结果却显示上述工艺得到的钽靶材再结晶不完全,这是因为EBSD分析的精度更高,其通过非弹性背散射电子的衍射获得样品表面每个极其微小区域的菊池花样,进而得到该微区的晶体学信息(晶体结构、晶体取向等),因此EBSD分析更微观,比金相组织观察更准确。通过EBSD结果分析退火态钽靶材α取向线和γ取向线上的织构组成,结果如图6所示。
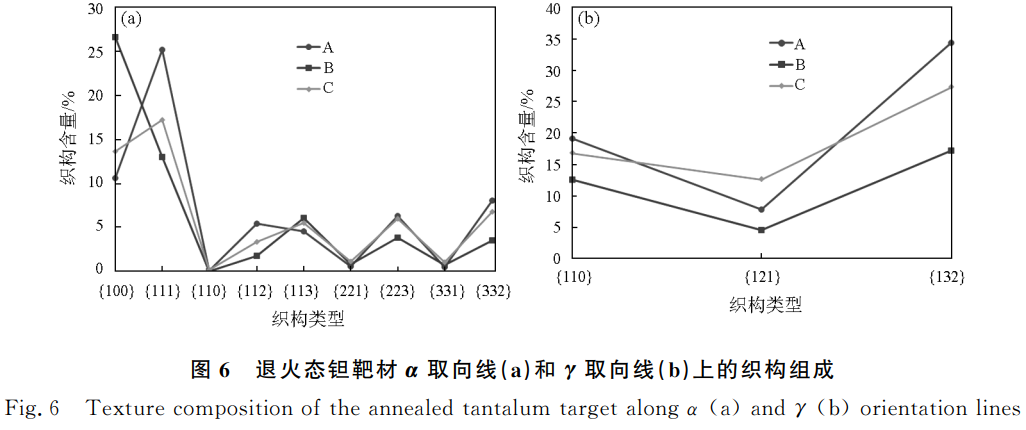
通常,大变形量的单向轧制会增强{111}取向织构的含量,从而获得{111}织构占优的钽靶材[17],而交叉轧制会使各种织构分布更均衡,对细化晶粒作用不大[18]。本试验采取交叉轧制工艺制备钽靶材,得到的织构是{100}-{111}混合随机织构。一般而言,bcc金属经过再结晶退火后,α取向线上的织构会消失,γ取向线上的织构会增强[19]。但从图6可以看出,退火钽靶材中α取向线上的织构含量仍然较高,γ取向线上的织构含量却不高,也说明成品退火再结晶不充分。如果延长退火保温时间或提高退火温度,使钽靶材达到完全再结晶,那么α取向线上的织构含量会降低,γ取向线上的织构含量会增加,但也会增加晶粒长大的概率,这需要在今后的试验中进一步验证。
4、结论
1)通过增大铸锭开坯变形量可使钽靶材在厚度方向获得细小而均匀的晶粒组织。
2)细小而均匀的晶粒组织有利于织构在厚度方向上均匀地随机分布。
参考文献:
[1] 侯洁娜,陈 颖,赵聪鹏,等.溅射靶材在集成电路领域 的应用及市场情况[J].中国集成电路,2023,32(7):23- 28.
[2] 钟景明,何季麟,汪 凯,等.芯片用钽阻挡层材料织构 控制技术研究[J].稀有金属,2018,42(12):1 273-1 280.
[3] 郝小雷.组织均匀钽溅射靶材的制备现状[J].山东工业 技术,2017(18):63,159
[4] 宜 楠,权振兴,赵鸿磊,等.集成电路用钽溅射靶材制 备工艺研究[J].材料开发与应用,2016,31(7):71-75.
[5] 刘 宁,杨 辉,姚力军,等.集成电路用大尺寸高纯钽 靶材的制备工艺进展[J].集成电路应用,2018,35(2): 24-28.
[6] ZHANG Z,KHO L,WICKERSHAM C E.Effect of grain orientation on tantalum magnetron sputtering yield[J].Journal of Vacuum Science & Technology A, 2006,24(4):1 107-1 111.
[7] MICHALUK C A.Correlating discrete orientation and grain size to the sputter deposition properties of tantalum[J].Journalof Electronic Materials,2002,31(1):2- 9. [8] MAGNUSON G D,CARLSTON C E.Sputtering yields of single crystals bombarded by 1- to 10-keV Ar+ ions [J].Journal of Applied Physics,1963,34:3 267-3 273.
[9] ONDERDELINDEN D.Single-crystal sputtering includingthe channeling phenomenon[J].Canadian Journal of Physics,1968,46:739-745.
[10] BEHRISCH R,ANDERSEN H H.Sputtering by particlebombardment Ⅰ:Physical sputtering of single-elementsolids[M].Berlin: Springer-Verlag,1981:219- 256.
[11] WEHNER G K . Controlled sputtering of metals by low-energy Hg ions[J].Physical Review,1956,102: 690.
[12] ZHUKOVA Y N,MASHKOVA E S,MOLCHANOV V A,et al.Effect of the target texture on the spatial distribution of sputtered substance[J].Bulletin of the Russia Academy of Sciences,1994,58:1 626-1 631.
[13] ECKSTEIN W,MASHKOVA E S,MOLCHANOV V A,et al.The effect of the fibre target structure on the spatial distributions of sputtered atoms[J].Nuclear Instrumentsand Methods in Physics Research (Section B),1996,115:482-484.
[14] CLARK J B,GARRETT R K,JUNGLING T L,et al. Influence of initial ingot breakdown on the microstructuraland textural development of high-purity tantalum [J].Metallurgical Transactions A,1991,22(12):2 959- 2 968.
[15] 国际钽铌研究中心.钽铌译文集[M].刘贵材,娄燕雄,译.长沙:中南大学出版社,2009:149-159.
[16] CLARK J B,GARRETT R K,JUNGLING T L,et al. Effect of processing variables on texture and texture gradients in tantalum[J].Metallurgical Transactions A,1991,22:2 039-2 048.
[17] 毛卫民,杨 平,陈 冷.材料织构分析原理与检测技 术[M].北京:冶金工业出版社,2008:87-88.
[18] CLARK J B,GARRETT R K,JUNGLING T L,et al. Influence of transverse rolling on the microstructural and texture development in pure tantalum[J].MetallurgicalTransactions A,1992,23:2 183-2 191.
[19] 余 永 宁.金 属 学 原 理 [M].北 京:冶 金 工 业 出 版 社, 2012:462.
相关链接