随着全球海洋资源开发向深远海加速推进,钛法兰凭借其“耐蚀-轻量-高强韧”三位一体特性,已成为深海能源系统的不可替代连接件。在深海油气开采、海水淡化、核电站冷却系统等关键场景中,传统不锈钢法兰因面临氯离子腐蚀、氢脆失效等问题,寿命不足钛法兰的1/3。以一艘11万吨级油船为例,其管路系统需配置超32,500个法兰连接点,采用钛法兰可实现减重40%,显著提升船舶燃油效率与载货能力。据行业预测,2024-2026年海洋工程钛材需求量将以10%年增速攀升,2026年用量将突破3,091吨,直接驱动钛法兰在深蓝战略中的核心地位。更关键的是,钛法兰的30年以上超长寿命可大幅降低全生命周期维护成本,为深远海装备的长效安全运行提供底层保障。
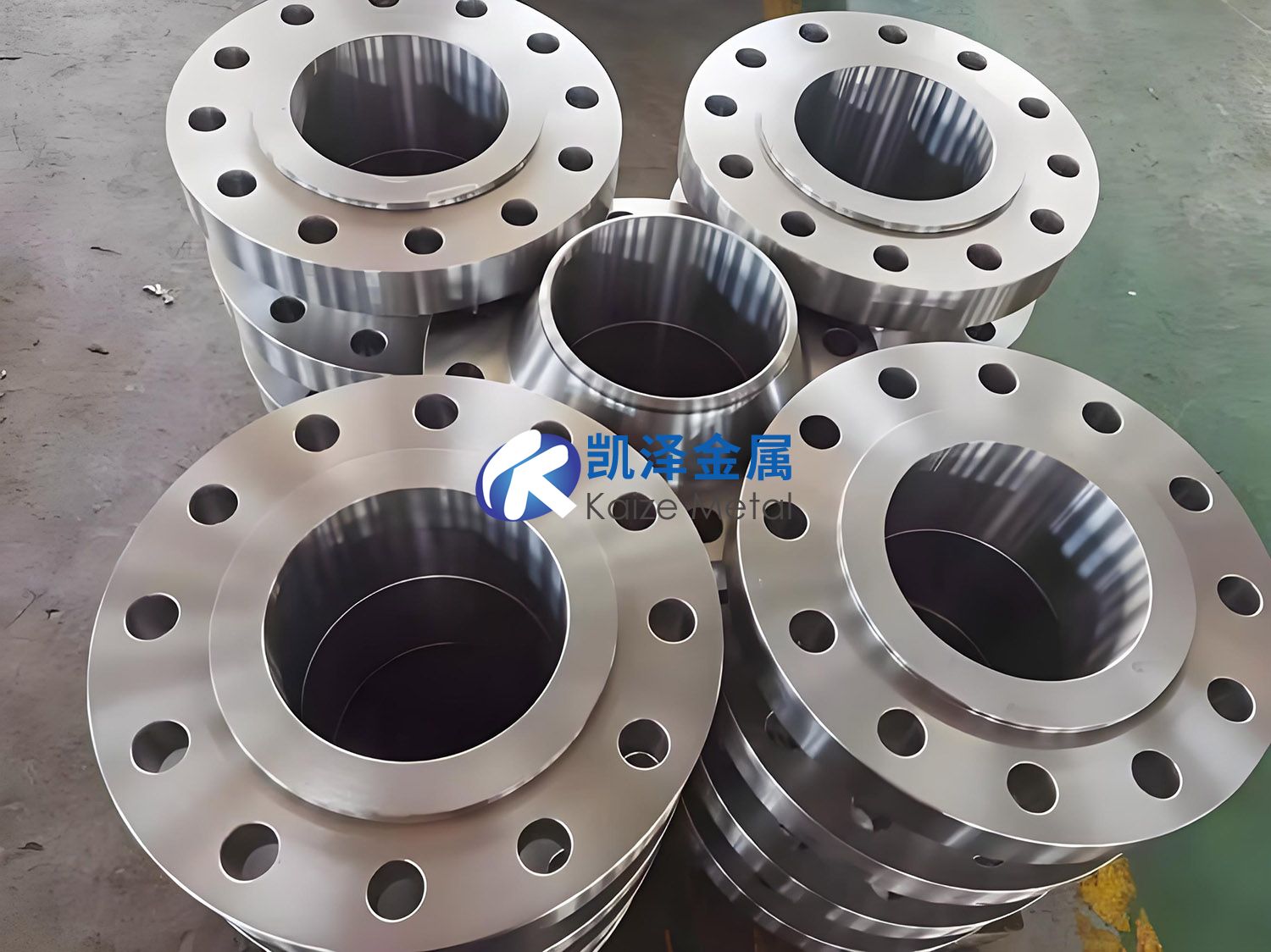
深海高压、低温腐蚀与动态载荷的复合极端环境,对钛法兰提出了近乎严苛的性能要求:
高压密封挑战:1,500米深海工况要求法兰耐受≥15 MPa压力,但钛合金低弹性模量易引发密封失效。前沿研究通过华脱斯法优化法兰锥颈结构,将密封应力集中降低37%,并结合紧凑型设计实现高压下的零泄漏;
氢脆风险防控:深海高压氢渗透速率高达10⁻⁶ g/cm²·h,需开发Ti-Al-Mo-Zr系专用合金(如Ti631)抑制氢扩散,并通过超塑成形/扩散焊接(SPF/DB)工艺替代传统锻造,消除晶界氢脆源;
大尺寸制造瓶颈:Φ>1.5米法兰需万吨级压机成形,国内装备能力不足。领先企业正探索激光选区熔化(SLM)增材制造,实现流道一体化成型,将生产周期缩短50%。这些突破标志着产业从“被动防腐”向“主动设计”的跃迁,推动钛法兰技术进入深海适配新阶段。
在“双碳”目标与海洋强国战略双重牵引下,钛法兰产业正经历结构性升级:
标准化与规模化:国内已建立TA2(Gr2)、TA10(Gr7)等船用法兰材料体系,形成DN20-DN200全系列产品,但三化(标准化、通用化、系列化)水平仍滞后。一艘船舶需26,000-32,500个法兰,若规格不统一将导致备件库存增加30%。近期《船用钛合金法兰通用规范》强制要求缩减尺寸规格,推动模块化设计,目标降低制造成本20%;
智造与绿色转型:宝鸡钛产业集群通过AI视觉质检+自适应加工将废品率压降至0.5%,而电解提取钛粉技术有望2030年落地,实现熔炼能耗降低60%;
国产化替代加速:尽管国内产能居全球首位(年产量超50万件),但航空级Gr9/Gr23钛材仍依赖进口。政策扶持下,头部企业正联合攻关“大规格锻件闭式锻造”技术,力争5年内高端钛法兰国产化率突破70%。此轮升级将催生千亿级蓝海市场,重塑全球海洋装备供应链格局。
一、材料科学基础
名义成分与牌号对应
常用牌号:
工业纯钛:TA1(Gr1)、TA2(Gr2)——高塑性,用于低压系统;
合金钛:TC4(Ti-6Al-4V, Gr5)——高强度,适用高压高温环境;TA10(Ti-0.3Mo-0.8Ni, Gr7)——抗还原性酸腐蚀。
关键元素作用:
Al提高耐热性,V增强韧性,Mo/Ni提升耐缝隙腐蚀能力。
物理与机械性能
物理特性:密度4.5 g/cm³(钢的60%),熔点1668°C,无磁性,热膨胀系数低。
机械性能(以TC4为例):
性能指标 | 数值范围 |
抗拉强度 | ≥895 MPa |
屈服强度 | ≥828 MPa |
延伸率 | ≥10% |
工作温度 | -250°C ~ 600°C |
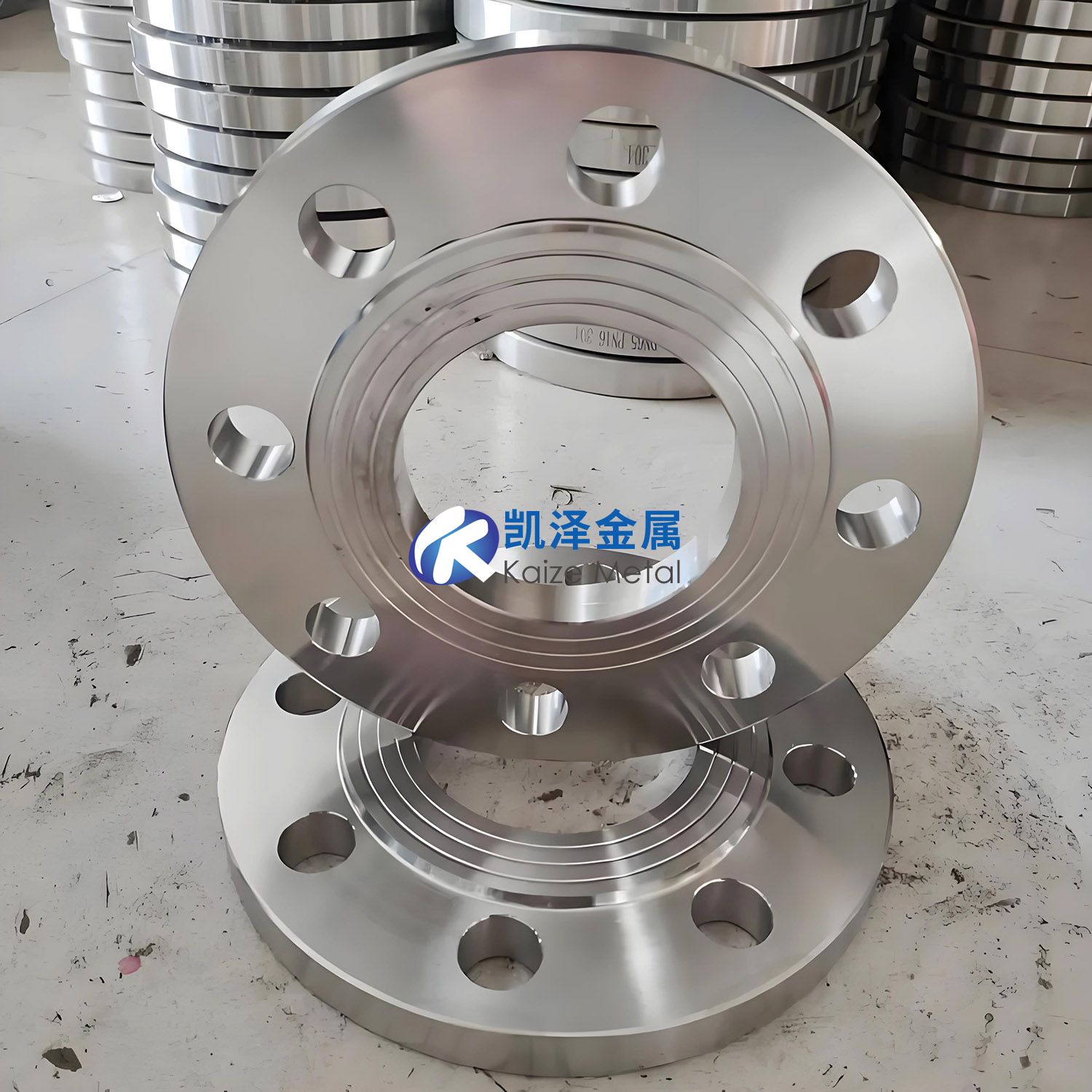
二、耐腐蚀性能与海洋适应性
海水环境表现:
钝化膜(TiO₂)赋予卓越耐蚀性,抗点蚀、应力腐蚀能力显著优于不锈钢。
长期耐受海水流速>20 m/s冲刷,寿命可达30年以上。
风险控制:
电偶腐蚀:需搭配钛合金螺栓或绝缘垫片,避免与钢/铝直接接触;
氢脆:高温高压氢环境中采用低间隙元素牌号(如Gr23)。
三、加工制造核心工艺
工艺流程

*关键环节:热成形需控温(800-900°C)防氧化;焊接需氩气保护,防止α脆化层。*
加工难点与对策
导热性差:低速切削(<50 m/min)+ 高压冷却液;
回弹大:精锻后增加时效处理消除应力。
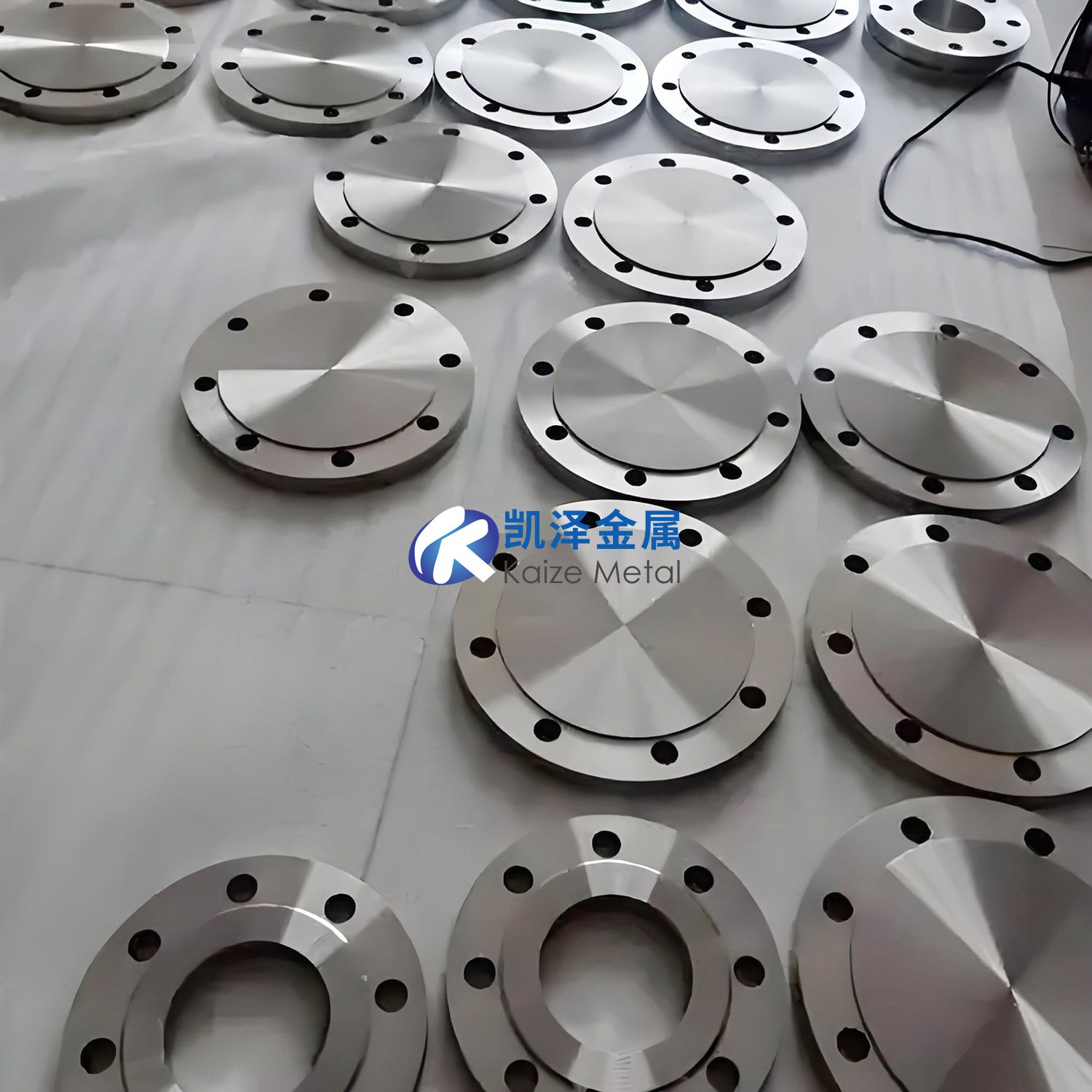
四、执行标准与产品规格
国际标准:
美标:ASME B16.5 Class150-900;
欧标:EN 1092 PN10-PN400;
日标:JIS 5K-20K110。
典型规格:
通径:DN15-DN3000(最大达DN1000常见);
压力:PN1.6-15.0 MPa(Class150-900)。
五、核心应用领域与典型案例
海洋能源系统
海水淡化:高压泵法兰(如TA10材质)耐受盐水腐蚀,寿命提升3倍;
深海油气:TC4法兰用于1500米水下采油树,耐压>15 MPa。
动力装备
船舶动力:轻量化法兰减重40%,燃油效率提升7%;
核电冷却系统:Gr2法兰在核岛二回路替代不锈钢,杜绝放射性泄漏。
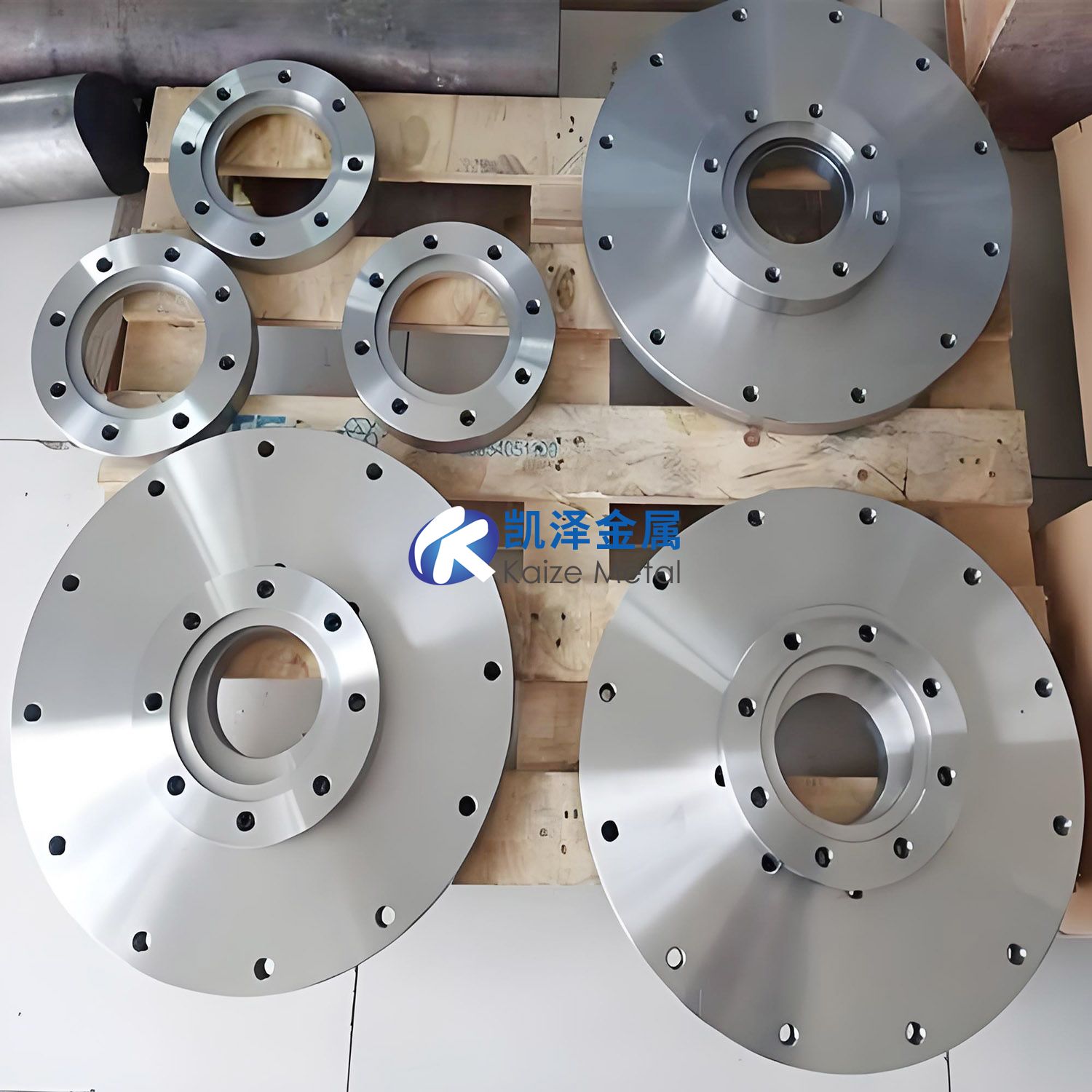
六、先进制造工艺进展
增材制造:激光选区熔化(SLM)实现复杂流道一体化法兰,缩短周期50%;
表面强化:激光熔覆TiB₂涂层,耐磨性提升200%;
智能化生产:AI视觉质检+自适应加工,废品率降至0.5%以下。
七、国内外产业化对比
维度 | 国内现状 | 国际高可靠性 |
产能规模 | 全球最大(宝鸡集群年产超50万件) | 美/日企业产能集约化 |
高端材料 | Gr9/Gr23依赖进口 | 美TIMET垄断航空级钛材 |
成本控制 | 设备利用率<30% | 德企通过闭环锻造降本20% |
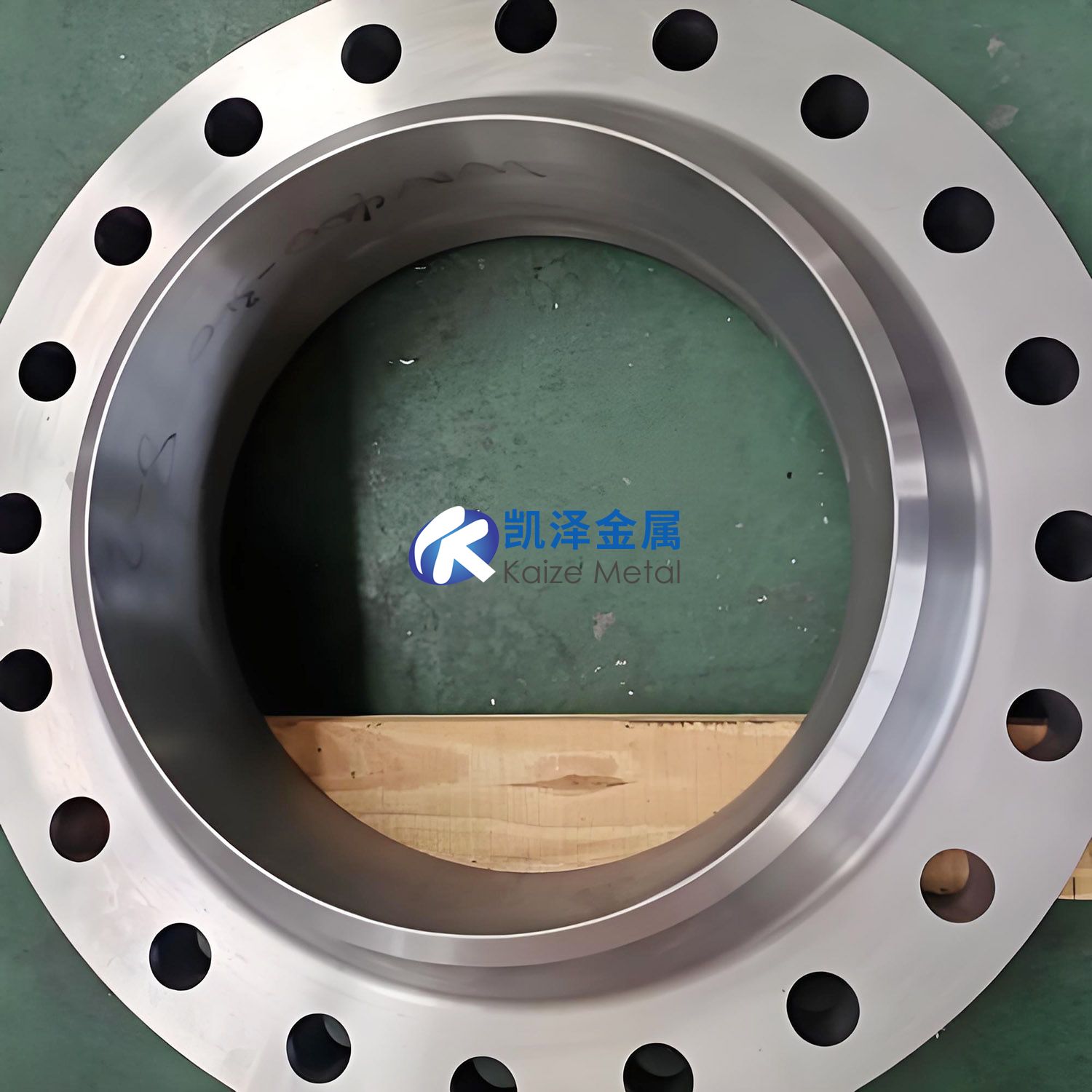
八、技术挑战与前沿攻关
瓶颈问题
大尺寸制造:Φ>1.5 m法兰锻造需万吨压机,国内装备受限;
氢脆敏感:深海高压环境氢渗透速率达10⁻⁶ g/cm²·h。
创新方向
材料设计:开发Ti-Al-Mo-Zr系深海专用合金(如Ti631);
工艺突破:超塑成形/扩散焊接(SPF/DB)替代传统锻造。
九、趋势展望
极端环境应用:万米深潜器法兰(目标耐压110 MPa);
绿色制造:电解提取钛粉技术降低能耗60%(2030年产业化);
数字孪生:全生命周期管理系统实现故障预测精度>95%。
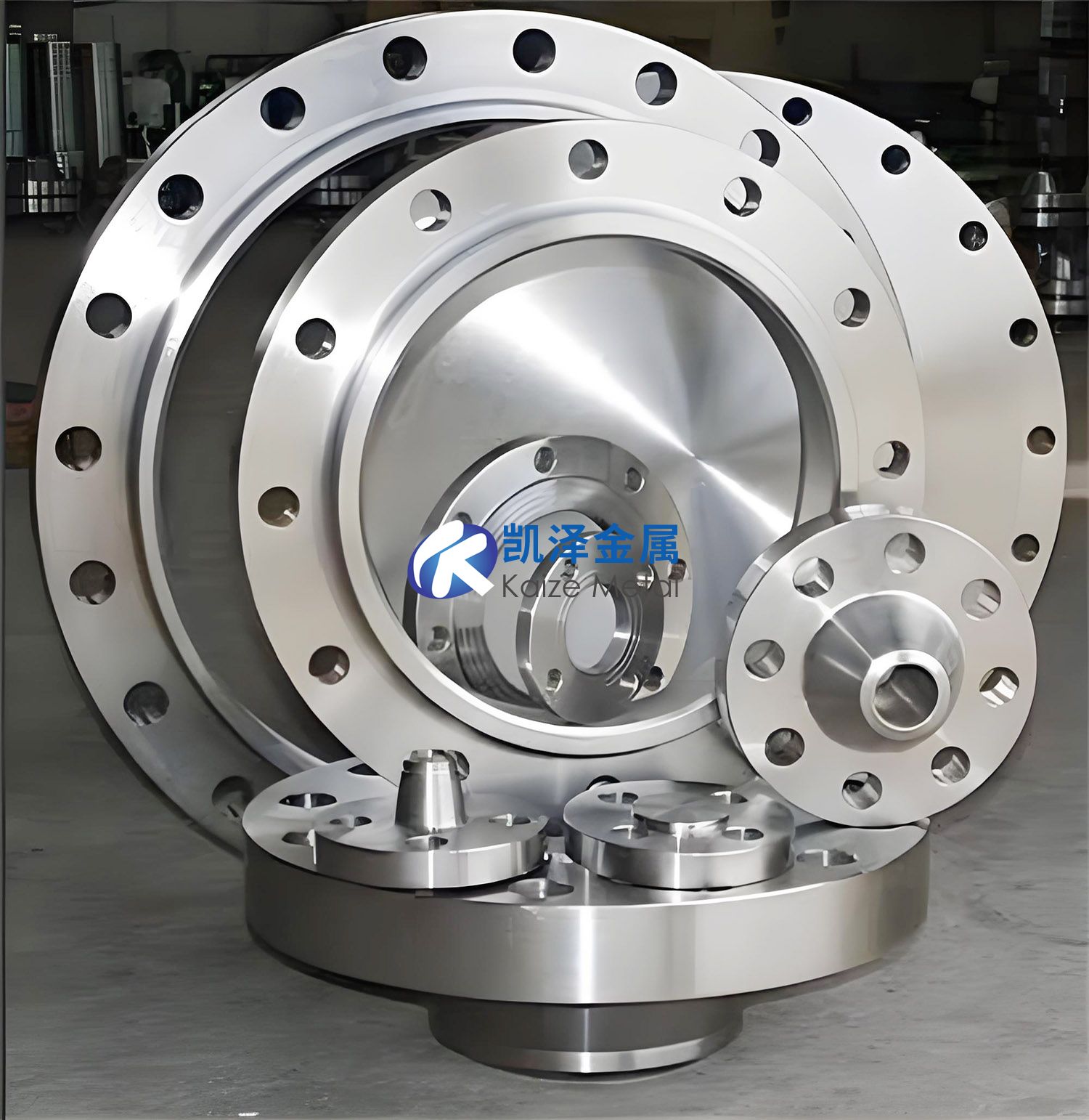
结语:
钛法兰在海洋工程能源动力领域的不可替代性源于其“耐蚀-轻量-强韧”三位一体特性。突破成本与制造瓶颈需产学研协同,重点攻关大规格构件成形与氢脆抑制技术,同时推动智能化与绿色冶金升级,为深远海开发提供可靠支撑。
相关链接