引言
近年来,计算机辅助设计技术(CAD)的进步,推动了增材制造(AM)(又称 3D 打印)技术的快速发展。 增材制造技术是一种基于三维数字模型,对产品进行建模分层,采用逐层制造方式将材料结合起来形成产品的工艺,其工艺流程如图 1 所示[1] 。 目前,增材制造技术被广泛应用于各个领域(如图 2),主要成形的材料有铝合金、钛合金、镍基高温合金以及陶瓷等[2⁃3] 。 金属材料增材制造技术依据其成形原理可分为:激光烧结式(SLS)、熔融沉积式 (FDM)、激光熔化式(SLM)、激光熔覆沉积(LCD)和电子束熔化沉积(EBM),其成形工艺对比见表 1[4] 。 常用的激光熔覆技术与选区激光熔化技术原理如图 3、图 4 所示[5⁃6] 。 增材制造所使用的金属粉末除了需要具备良好的可塑性之外,还必须满足粉末粒径细小、含氧量低、粒度分布区间较窄、球形度高、流动性好和松装密度高等要求。 当前,增材制造能够应用的金属粉末材料种类包括模具钢、镍合金、钛合金、铝合金和青铜合金等。 一般情况下,激光选区熔化成形中所需粉末粒径在20~45μm,而激光熔覆成型中所需粉末粒径一般在 90~150 μm[7] 。 目前,等离子旋转电极法(PREP)、等离子雾化法(PA)和气雾化法(GA)是增材制造用金属粉末的主要制备方法,三种方法都可以制备球形或者近球形金属粉末。
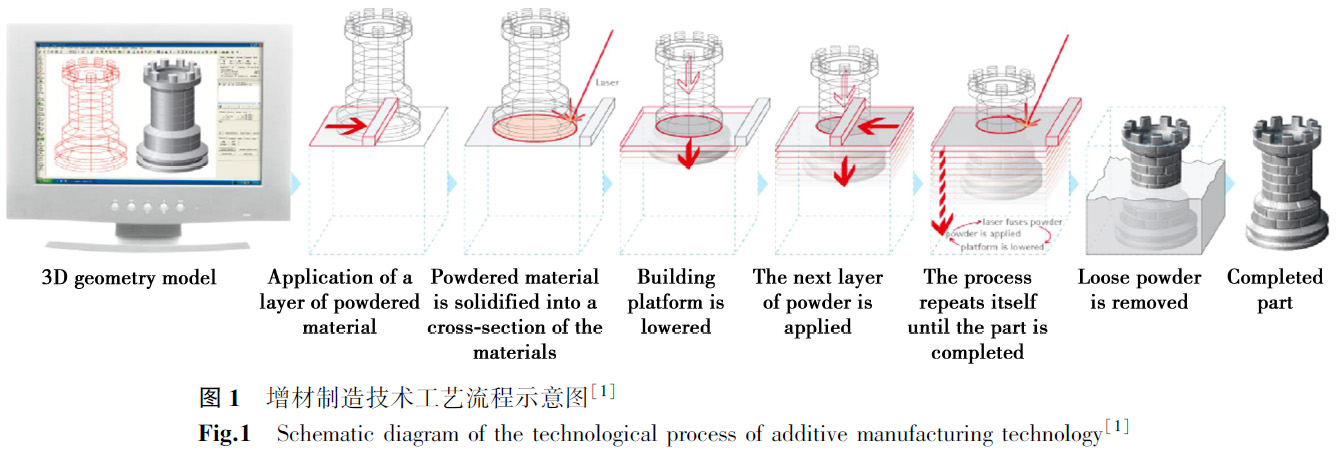
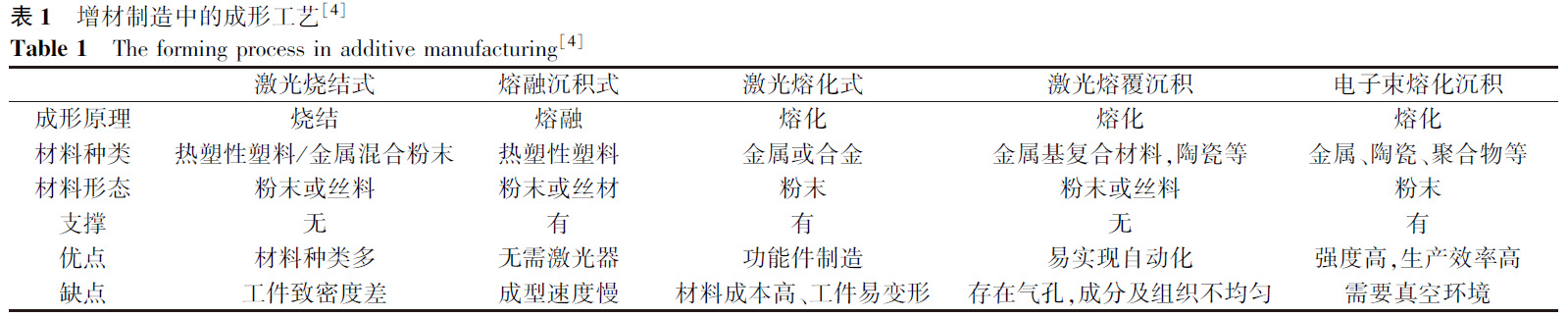
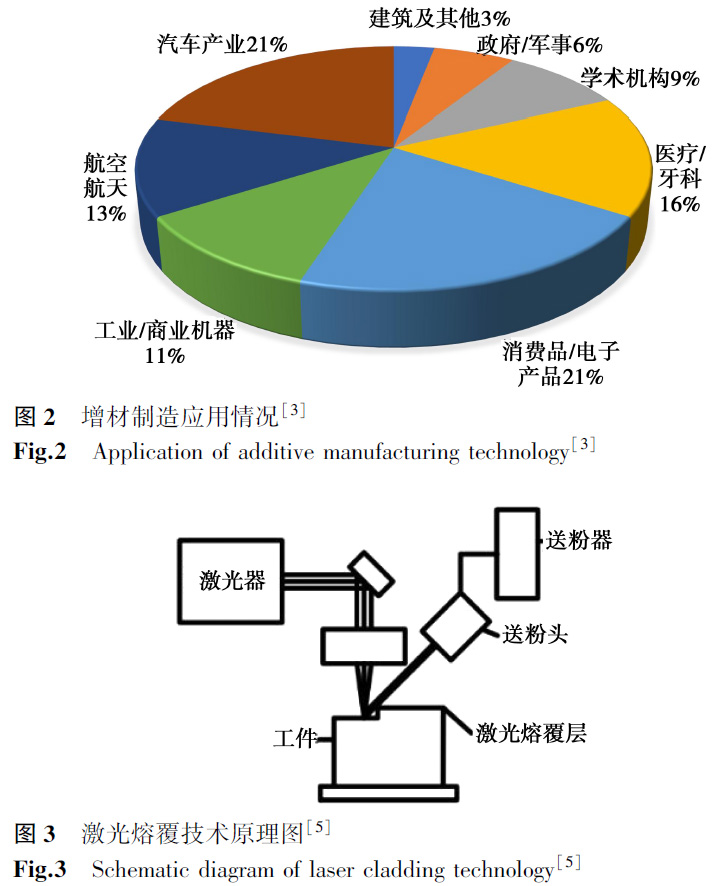
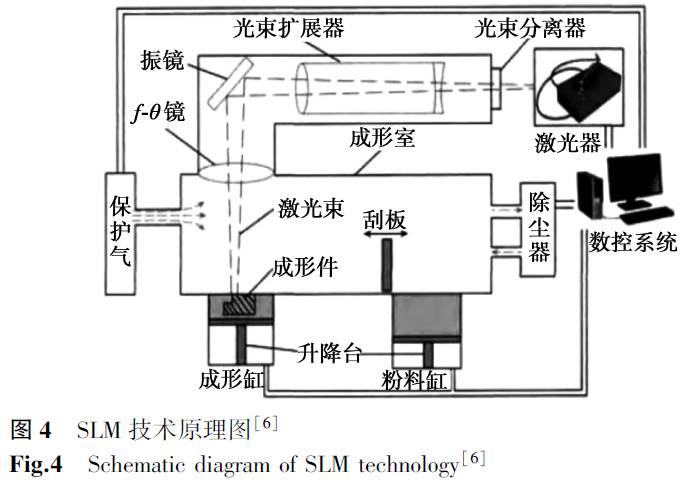
相比传统制造,增材制造具有以下优势:(1)节约环保,没有边角料,材料利用率高;(2)可生产形状结构复杂的产品;(3)按生产情况所需,即打即用;(4)生产周期短,效率高。
因此,增材制造技术被广泛地应用于航空航天、医疗、教育、生活等各个领域,主要体现在机械制造领域。 但是,增材制造技术也存在着以下的问题[8] :(1)大部分工艺采用的原料是粉末,其制备要求较高;(2)材料成型的过程比较难控制;(3)所得成形件的精度不高;(4)增材制造过程中的支撑结构制备技术不成熟;(5) 所应用的软件编程技术有待进一步提高。
1、镍基高温合金研究进展
镍基高温合金是一种在高温条件下(540 ~ 1 000 ℃ 范围)具有高强度、抗氧化能力好、蠕变强度和持久强度好以及抗燃气腐蚀能力的材料。 它是基于 Cr20 Ni80 合金发展起来的,为满足高温热强性和气体介质中的抗氧化和抗腐蚀的要求,加入了大量的强化元素,来保证其优越的高温性能。 镍基高温合金凭借其优异的综合性能,被广泛应用于航空航天领域、汽车通讯领域、船舶制造领域等(见图 5)。 镍基高温合金的开发和使用开始于 20 世纪 30 年代末期,是基于飞机对材料的综合性能提出更高要求的背景下发展起来的,英国于 20 世纪 40 年代初率先生产出 NI75 镍基合金,后来美国和苏联也相继研制出镍基高温合金,中国于 20 世纪 50 年代研制成功。 镍基合金的发展包括合金成分的改进和生产工艺的创新两个方面,真空熔炼技术的发展为制备镍基合金提供了条件。 之后,通过熔模精密铸造工艺制备了许多具备良好高温强度的铸造合金。 镍基高温合金种类繁多,已成熟应用于 SLM 工艺的合金材料有 K4202、GH3536、IN738LC、IN625、IN718 五种[9] 。
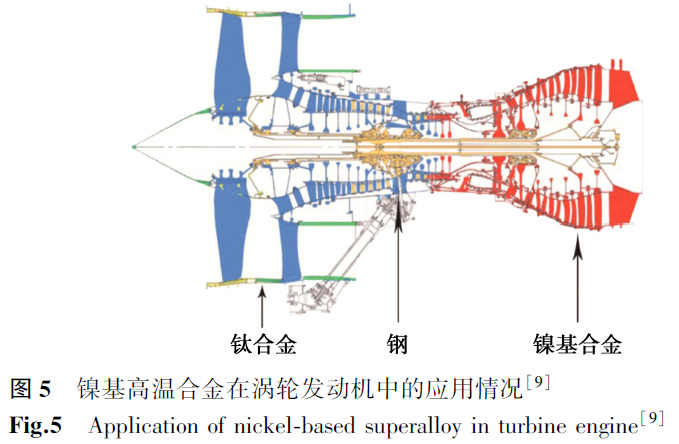
未来,镍基高温合金的发展趋向于低成本、高强度、密度小以及抗热腐蚀性方向。 镍基高温合金的发展有以下几个方面[10] :(1)发展耐腐蚀性能优越的单晶合金;(2)保持组织稳定性,提高材料强度;(3)降低昂贵金属元素的添加量,节约成本;(4)研究发展密度小的单晶合金。 随着我国工业化的进步,镍基高温合金以其优异的性能在航空领域所占比重越来越大,尤其用于制造发动机受热部件以及火箭发动机的各种高温部件。 随飞机发动机性能要求的提升,对材料的要求也相应提升。 因此,推进耐高温以及耐腐蚀性能的合金发展对我国航空事业的发展有着重大意义。
2、增材制造镍基高温合金研究现状
激光增材制造对于镍基高温合金的制备具有独特的优势,如生产周期短、成本低以及可进行功能预设等。 对于航空发动机及燃气机轮中喷嘴、燃烧室等热段部件以及航天飞行器等复杂零件的成形制造非常有利[11] 。 近年来激光增材制造镍基高温合金受到广大研究人员的关注,研究热点主要有以下几点[11⁃13] :(1)激光增材制造过程中凝固组织的变化规律;(2)激光增材制造过程中工艺参数与熔池宏观形态间的关系;(3)激光增材制造过程中残余应力的分析探究;(4)激光增材制造过程中的缺陷的探究。 国内外的专家对激光增材制造镍基高温合金做了大量的研究,以下对激光增材制造的镍基高温微观组织以及力学性能等方面进行介绍。
2.1 微观组织
2.1.1 3D 打印沉积态的微观组织
目前,应用增材制造工艺制备镍基高温合金较为普遍,最常用的方法主要有 SLM 和 LCD 技术两种。 增材制造技术制备的镍基高温合金与传统制造所得合金在微观组织以及
性能上差异较大。 通过不断调整工艺参数探究增材制造制备的镍基高温合金的微观组织以及缺陷变化,寻求最优化的制造工艺,来提高增材制造镍基高温合金的应用性能。
金属增材制造沉积过程中,高能量激光束熔化金属粉末,扫描过程中会形成熔池特征。 激光束光斑直径在微米尺度,故熔池尺寸也在微米等级。 且成形过程中移动速度较快,激光束能量集中,熔池附近温度梯度高,熔池冷却很快,晶粒没有充裕的时间长大。 熔池与金属粉末、已凝固区以及周围气体存在热传导、热对流等,故散热方向复杂多样。 因
此,增材制造过程显微组织的形成极其复杂,与传统工艺产品的微观组织差异较为显著。 增材制造镍基高温合金零件沉积态 形 貌 一 般 为 典 型 的 鱼 鳞 状 相 互 搭 接 的 熔 池 形 貌。
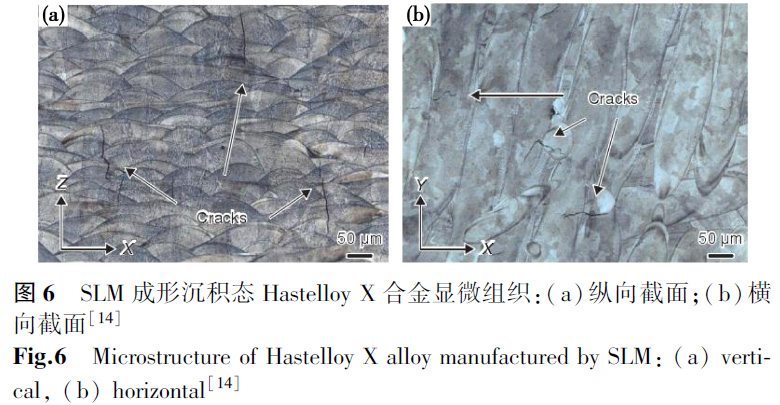
图 6[14] 为 SLM 工艺制备 Hastelloy X 合金纵向和横向截面的微观组织,从图中可以观察到沿沉积方向熔池层叠,呈鱼鳞状。 这种鱼鳞状形貌的形成的原因[15] 是:每根熔线截面受激光熔化本道熔线的形貌和相邻下一道熔线形成过程的影响,下一道熔线成型前,当前熔线的底部呈碗状,而顶部的形状受到液态表面张力以及底部熔池熔液的粘附力共同作用,一般呈弧形。 当下一道熔线成型后,依据扫描的方向,前一道熔线的部分形貌因部分重熔而被后一道熔线擦除,擦除部分的多少取决于扫描间距的大小,扫描间距越小,擦除部分越多,最终会形成鱼鳞片状单层结构。
实际应用过程中,晶粒的取向对金属零件的使用性能有着非常重要的影响。 增材制造镍基高温合金零件的晶粒主要包括柱状晶粒和部分的等轴晶粒。 陈梦洋等[16] 对增材制造的 FGH96 高温合金成形件进行了显微组织观察,发现其组织基本上为柱状晶组织,接近表面处有细小的等轴晶生成,这种典型的组织在相关文献中已经得到证实[17] 。 利用 EBSD技术进一步分析发现,当打印的材料厚度不同时,其组织结构也并不相同。 当厚度为 2 mm 时,主要以柱状晶为主,大部分为立方织构{001}〈100〉;当厚度为 5 mm 时,主要为柱状晶和等轴晶,柱状晶区域织构主要是{001}〈120〉和{001}〈230〉,等轴晶织构主要为{113}〈141〉。 增材制造合金组织中柱状晶和等轴晶的形成过程主要为扫描速度快,残留于沉积层的热量来不及扩散出去,前一层对下一层沉积起到了高温回火的作用。 随着沉积层厚度的增加,热量逐渐积累,试样整体温度升高,对后一层回火温度越高,所以后一层的组织以柱状晶方式生长。 当沉积接近顶层,试样接触空气产生急冷效果,进而导致表面形成了细小的等轴晶。
目前,对于增材制造镍基高温合金的研究发现,形成的晶粒尺寸除柱状晶区外,还存在细晶区和粗糙蜂窝状晶区,结果如图 7 所示[18] 。 这种现象是因为随着激光能量的输入,粉末熔化形成细小的晶粒,并且扫描过程中出现重熔区,使得高能量输入区域的亚晶胞状组织长大成蜂窝状的粗糙胞状组织,而另一部分晶粒在负温度梯度下沿粗糙界面长大成柱状晶。
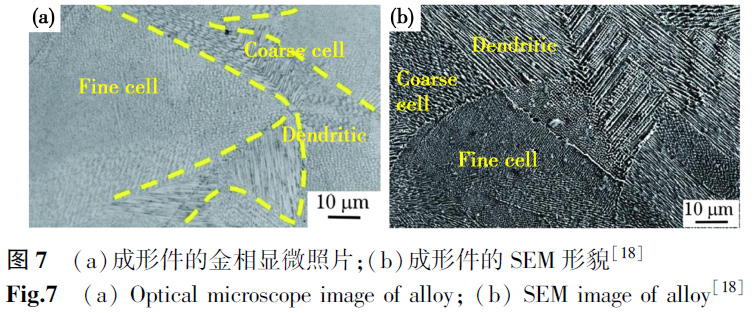
晶体的各向异性是由于沿晶格的不同方向,原子排列的周期性和疏密程度的不同,导致晶体在不同方向的物理化学特性也不同而产生的持征。 晶体的各向异性具体表现在不同方向上的弹性模量、硬度、屈服强度等的差异。 增材制造技术因其本身工艺的特点,晶体的各向异性特征也非常显著。 Choi等[19] 利用 SLM 技术制备了 IN718 试样,利用扫描电镜对试样的 XZ 平面微观组织进行分析,发现熔池中间为柱状晶粒,柱状晶粒的生长方向与熔池冷却的方向基本相同,这与熔池凝固过程中的热流方向和凝固冷却温度梯度有关。 熔池边缘存在等轴晶粒,且晶体取向具有多种,其原因是[9] :其一,打印过程中熔池边缘位置发生重熔,导致晶粒生长方向随热流方向的变化发生改变;其二,熔池边缘杂质富集,使得晶粒生长为异向的等轴晶小颗粒。
此外,一些学者对增材制造合金的显微组织进行分析时,在层与层之间的组织中还观察到层带结构,如图 8 所示[20] 。有研究认为成形件底部形成的层带组织是在高温度梯度及低凝固速度下平界面凝固生长的结果,成形件中部的层带结构则是平界面生长受到扰动失稳所导致的[21]。
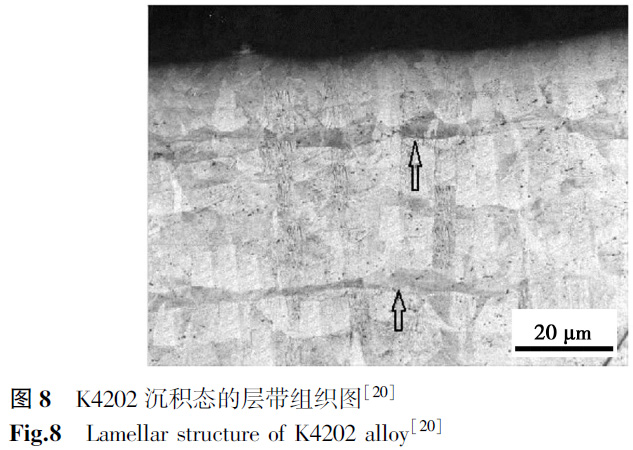
增材制造制备镍基高温合金过程中冷却速度很快,最初形成 γ 枝晶干,溶质元素不断进入枝晶间的液相中,出现成分过冷与枝晶偏析现象,故枝晶间会产生许多低熔点共晶相。
通常情况下,共晶反应首先发生,形成一次碳化物 MC,凝固最后阶段发生 L→γ+Laves 共晶反应,生成大量的 γ/ Laves 共晶。在增材制造过程中,复杂的热循环会对已沉积层产生热处理效应,造成共晶产物进一步发生固态相变,析出碳化物以及 δ相等。 吕豪等[22] 对 10 mm/ s 的沉积速度下的 GH4099 合金微观组织进行了观察,并对 GH4099 合金沉积态的析出相进行了分析,发现了枝晶之间存在明显的白亮色相,如图 9 所示。 利用能谱仪对其进行研究,结果表明,白亮色的相为 γ⁃γ′共晶相,是 Al 和 Ti 元素在枝晶间产生了明显的偏析所造成的。
Chlebus 等[23] 对 SLM 技术制备的 IN718 试样的微观相分布进行分析时,发现了脆性 δ⁃Ni3Nb 相和 Laves 相,以及在枝晶结构间离散分布的溶质元素。 此现象出现在多熔道的重熔区域或凝固层的层间重叠区域,主要是由于 Nb 和 Mo 元素在熔池固化的过程中会发生微观偏聚而形成的,这在一定程度上会造成成形件的残余应力,进而影响成形件的性能。 Brynk 等[24]向 IN718 合金粉末中添加了不同质量分数的 Re 金属元素,利用透射电子显微镜分析了增材制造所得成形件的微观组织,结果如图 10 所示。 他们发现添加适量的 Re 能使 IN718 零件经热处理后的树枝状晶粒更细,但过量会导致有害相 Laves 相和碳化物的增加,在难溶部分的 Re 附近形成许多位错。
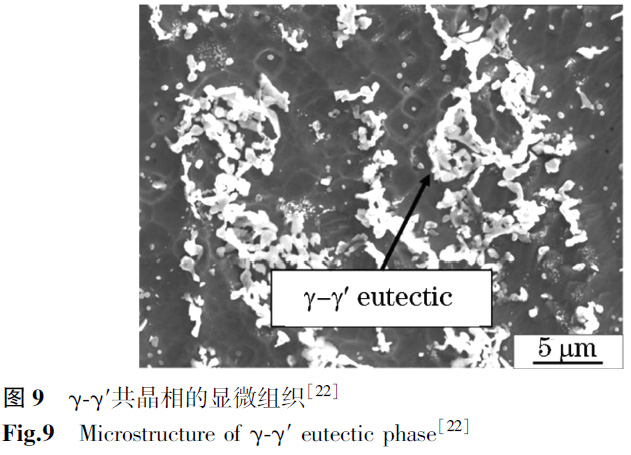
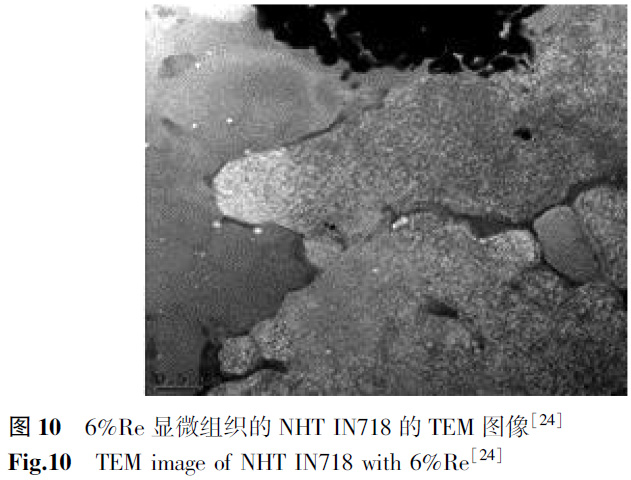
传统铸造工艺成形的镍基高温合金组织形貌以粗大的枝状晶状结构为主,需要通过锻压消除颗粒晶界、压碎枝晶,使得晶粒细化为等轴晶结构达到 SLM 净成形合金晶粒大小水
平。 增材制造镍基高温合金成形件的组织,其形貌为典型的鱼鳞状相互搭接的熔池形貌,晶粒以具有显著外延性特征的柱状晶和等轴晶为主,组织中也存在一些偏析所致的脆性
δ⁃Ni3Nb 相和 Laves 相,这些相的存在降低了成形件的性能。
2.1.2 后处理的组织特征
为了减少或消除增材制造后零件的微观和宏观缺陷,提高其综合性能,进行后处理是很有必要的。 目前,普遍应用的后处理方法主要有热等静压处理(HIP)、固溶处理(ST)和时效处理(AT)。 一般情况下,可结合两种或两种以上的处理方法对材料微观组织进行改善。 对于增材制造所得试样,选择合理的后处理工艺能够极大地改善合金的组织,进一步提高成形件的性能。
热等静压处理的基本原理是以气体或液体作为压力介质,使材料在加热过程中经受各向均衡的压力,借助于高温与高压的共同作用促进材料致密化和元素扩散。 热等静压技术
最显著的特点是可使处理后的材料仍保持细晶粒的晶体结构。
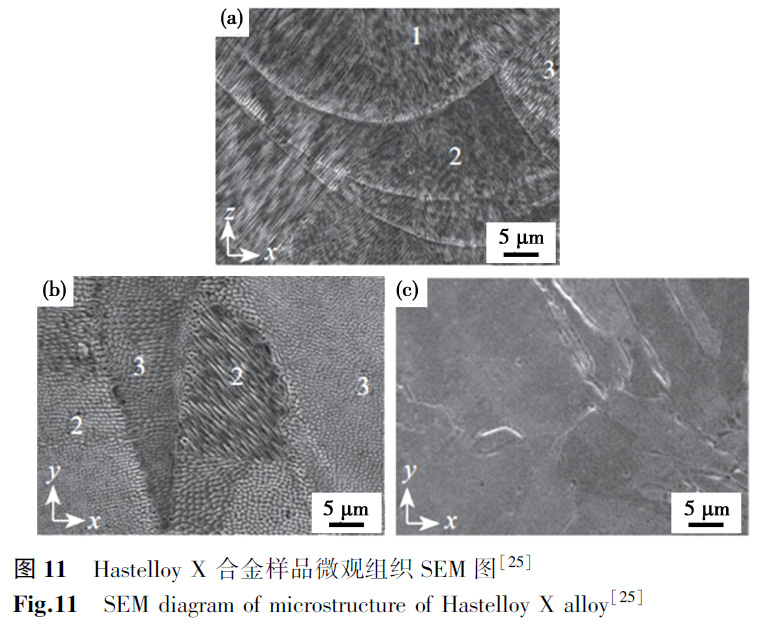
经过热等静压处理后,熔池边界消失,微观组织中枝状晶发生溶解并呈现均匀化,形成等轴晶,如图 11 所示[25] 。 李雅莉等[26] 对SLM 制备的 Hastelloy X 合金试样经过热等静压(1 175 ℃,150 MPa,1 h,炉冷)处理后的微观组织进行了观测。 研究发现经过热等静压后,熔池形貌消失,裂纹愈合。 同时微观组织演变为等轴晶,且晶界及晶内溶质元素扩散并聚合,形成了较多的析出物。 张永志等[15] 对 SLM 制备哈氏合金试样做了热处理+热等静压处理,研究了横向和纵向截面的晶粒形态,发现纵向截面中部分晶粒为柱状晶态,而横向截面中晶粒基本为等轴晶组织,且横向和纵向截面存在一定量的细晶区,这是因为在热等静压再结晶过程中,晶粒之间或晶粒与周围粗晶的取向差异较大,部分细晶不能充分合并长大,导致热等静压后仍存在少量相对较细的晶粒。
固溶处理是将合金加热到合理的温度范围之内,促进溶质原子充分溶解于固溶体之中,进而使得固溶体产生畸变,增大位错运动阻力,使得合金得到强化。 吕豪等[22] 对激光增材制造 GH4099 合金沉积态试样进行了固溶处理(1 120 ℃,2 h),研究表明,在固溶处理过程中发生了明显的再结晶,柱状晶内部的枝晶形貌消失,转变为细小的等轴晶组织,且在等轴晶内部存在许多孪晶界。 利用扫描电镜进一步观察,发现枝 晶 间 的 初 生 相 发 生 了 明 显 的 回 溶 反 应,相 的 尺 寸 从10 μm下降到了 200 nm 左右,如图 12 所示。 这是由于在凝固过程中 Al 和 Ti 等元素偏析到枝晶间形成尺寸较大的初生相,导致沉积态组织中存在微观偏析现象,形成了枝晶亚结构;而高温固溶过程也是一个均质化的过程,可以明显地消除组织中的偏析,使初生相发生回溶,尺寸有所降低,而且 Al和 Ti 等元素在经过固溶处理后充分固溶在 γ 基体中,这使得
存在于沉积态中的枝晶亚结构也会消失。
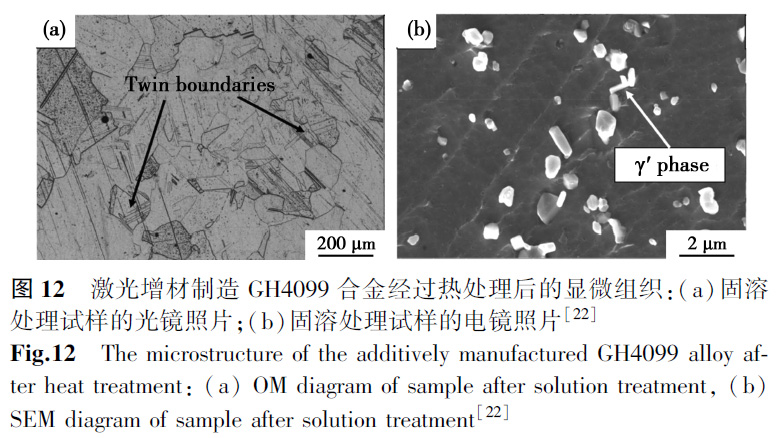
时效处理主要是经时效处理使得饱和固溶体中的合金元素弥散析出在合金基体中,从而形成部分体积较小的溶质原子富集区,进而形成沉淀相,此沉淀相能有效阻止位错和晶界的运动,改善组织,对合金起到强化作用。 然而,单一的时效处理对组织的改善并不理想,目前应用较为广泛的是固溶+时效处理方法。 邓晓阳等[27] 对 SLM 工艺制备的 IN718合金进行了固溶+双级时效处理(940 ℃×1 h,空冷+720 ℃ ×8 h,56 ℃ / h 炉冷到 620 ℃后保温 8 h),发现处理后合金在晶内和晶界析出了短棒状和针状两种不同形貌的相,利用 EDS分析发现这两种相均为 δ 相。 合金中晶界短棒状 δ 析出相在固溶过程中析出,而晶内针状 δ 析出相在时效过程中析出。 利用 TEM 与电子衍射对试样进一步观察分析,结果如图 13 所示,发现还存在圆盘状 γ″相和黑点状 γ′相,这些析出相强化了合金的性能。
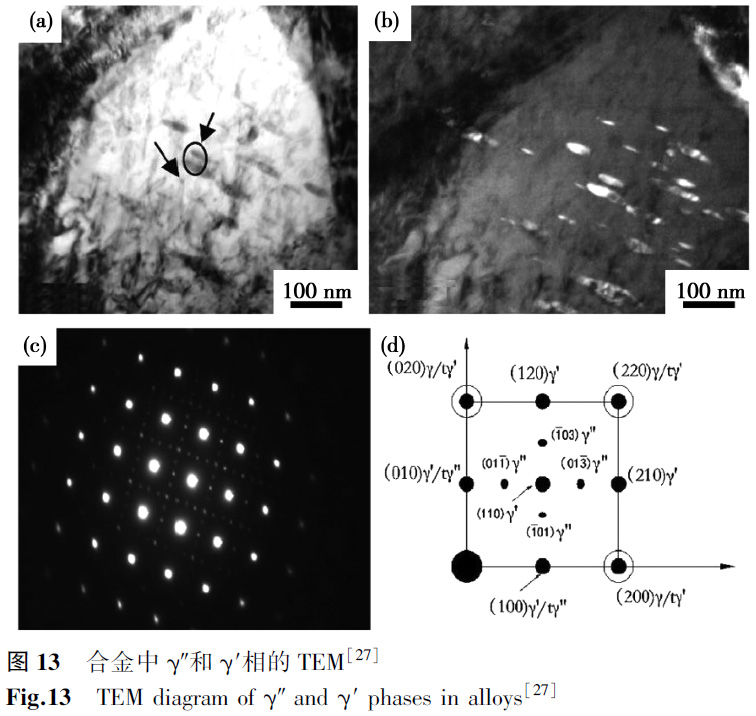
黄文普等[28] 利用 SLM 技术制备了 K4202 合金并进行了固溶+时效处理(1 125 ℃保温 4 h,空冷至 825 ℃保温 5 h 再空冷至室温), 结果表明成形态组织主要为 γ 相, 经固溶+时效和时效处理后,γ′相大量析出。 通过 XRD 对不同后处理状态下的试样进行分析发现,试样中均存在 CrNi、Ni3(Al,Ti)、
Cr2Ni3、Ni17 W3 以及 MoNi4 这几种物相。 其中基体 γ 相为CrNi,构成 Ni⁃Cr 基固溶体;γ′相为 Ni3 (Al,Ti);而 Cr2Ni3、Ni17W3和 MoNi4 为合金中的属间化合物。
经过后处理之后,增材制造所得零件的组织呈现均匀化,熔池边界消失,晶粒转变成细小的等轴晶,组织中含有较多不同形貌的 δ 析出相,晶粒的长大被抑制,固溶+时效处理
后,γ′相和 γ″相的析出强化了合金的性能,脆性 Laves 相得到了完全溶解,且 MC 碳化物增加,后处理后组织的变化使得成形件的综合性能得到充分改善,满足了复杂条件下样件应用标准。
2.2 力学性能
力学性能是镍基高温合金的一个应用的重要指标,包括强度、延伸率及硬度等。 表2简要概述了通过不同材料和工艺所获得的最高可实现的力学性能[29] 。 XY 是指平行于构建平台构建的拉伸试样,而 Z 是指垂直于构建平台构建的拉伸试样。 在参考平面的横截面上测试样品的硬度。 由 SLM制造的镍基高温合金零件经后处理后其力学性能得到了极大的改善,表 3 简要概括了 SLM 成形的各种镍基高温合金经后处理后的力学性能。
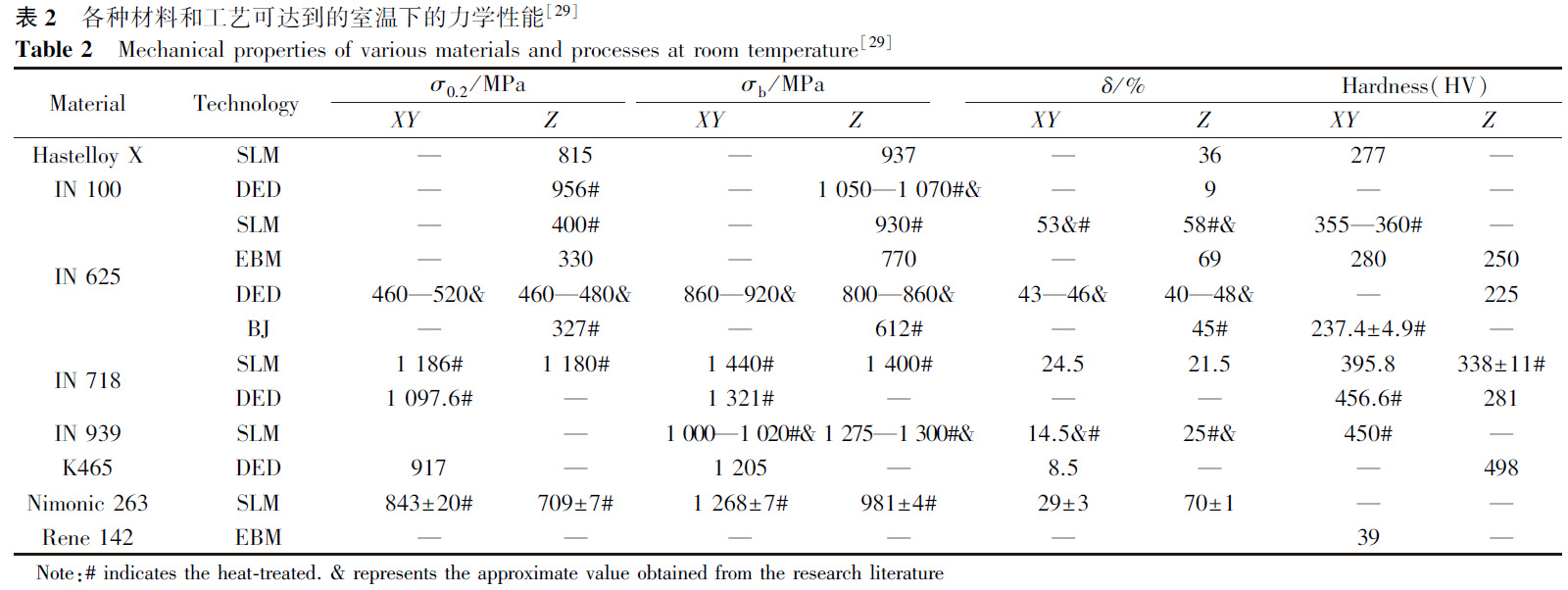
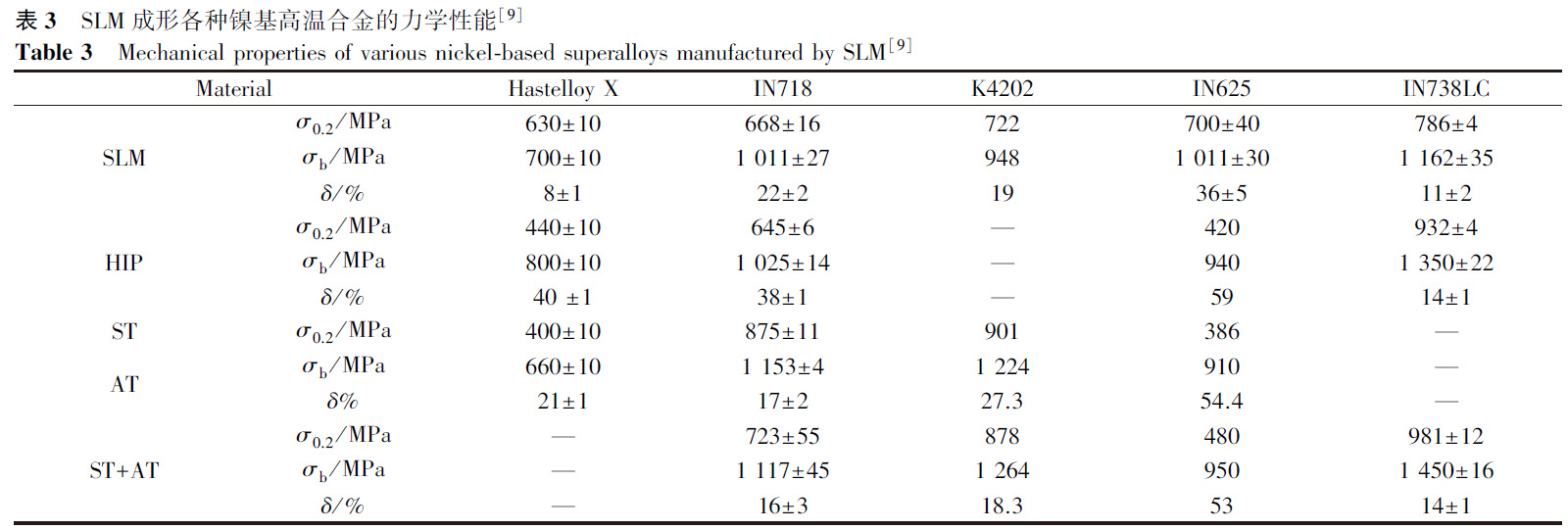
2.2.1 显微硬度
硬度通常定义为材料抵御硬且尖锐的物体所施加的压力而产生永久压痕的能力。 材料的硬度是材料重要的力学性能之一。 不同于拉伸性能的各向异性,增材制造制备的试样在沉积方向或垂直于沉积方向上的硬度差异比较小。 赵卫卫等[30] 对激光立体成形 IN718 沉积态的显微硬度做了测试。 图 14 为显微硬度沿沉积方向的变化情况,可以发现沿沉积方向,从底部到表层硬度分布较为均匀。
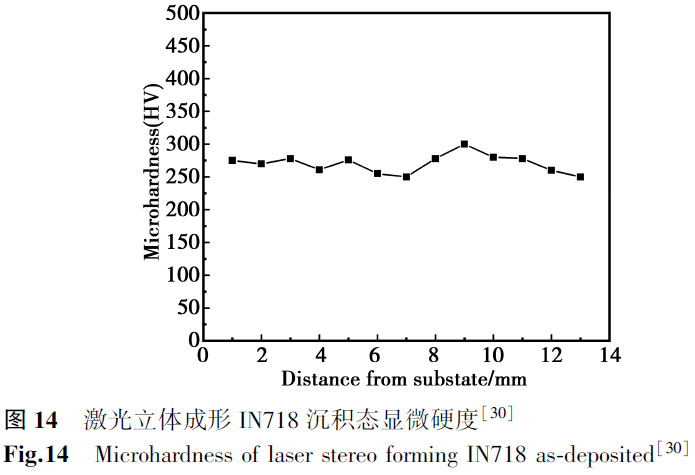
增材制造制备的试样存在各种类型的缺陷,会对沉积态的硬度造成不同程度的影响。 因此,选择合适的后处理工艺能够进一步提高试样的硬度。 黄文普等[28] 对 SLM 制备的K4202 合金,在沉积态,固溶+时效(1 125 ℃ /4 h,空冷至 825 ℃,保温 5 h 再空冷至室温)和时效处理(825 ℃ /5 h,然后空冷至室温)三组试样的显微硬度进行了测试,结果如图 15 所示。 研究发现,热处理后的 K4202 试样的硬度明显高于沉积态,且时效处理的硬度略高于固溶+时效处理的试样。 其原因是在热处理过程中合金中的 γ′相从过饱和的 γ 相中析出,γ′相有效地提高了试样的显微硬度。 而固溶+时效过程中再结晶的发生使得晶格畸变和位错减少,晶粒发生长大,因此固溶+时效处理后试样的显微硬度略低于时效处理的试样,文献[31]也证明了这一点。
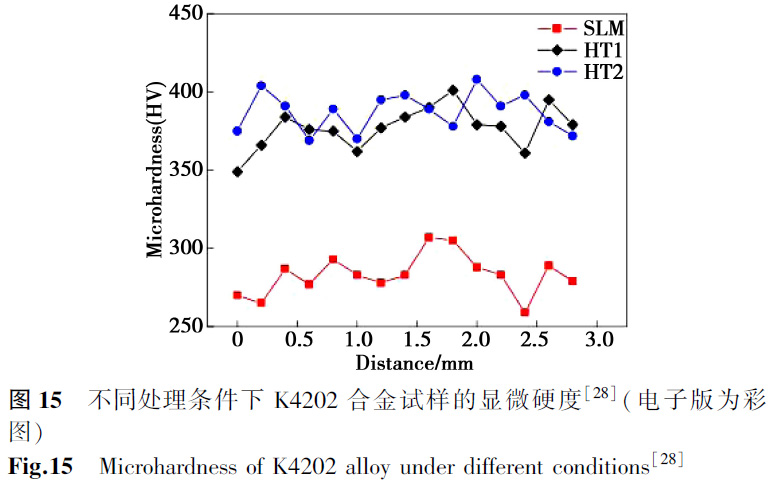
2.2.2 拉伸性能
增材制造镍基高温合金相比于传统的铸态或锻态,其显微组织有着很大的差异, 因而材料的力学性能也不同。 大量研究表明,增材制造技术制备的试样拉伸性能优于传统的铸
造合金。 如表 4 所示,为 SLM 制备的 K4202 试样的拉伸性能测试结果,结果表明 K4202 合金 SLM 成形态试样的拉伸强度和塑性明显优于传统铸造合金。
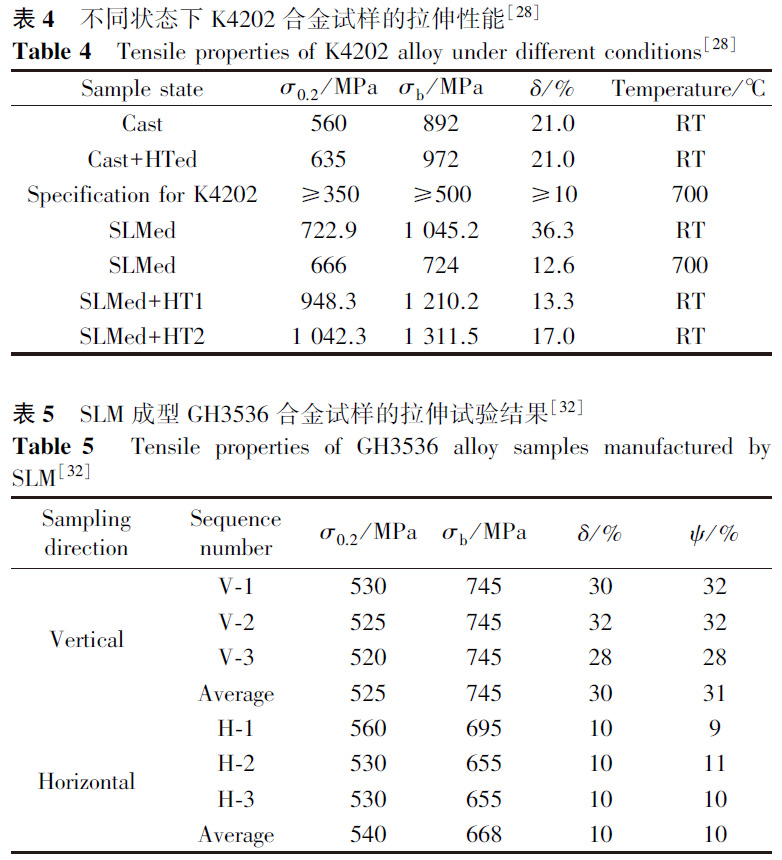
由于增材制造工艺本身的特点,所制备的合金材料显微组织存在着各向异性,其不同方向的拉伸性能也有所不同。 刘凯等[32] 对 SLM 成形的 GH3536 试样以 1 mm/ min 的速率在常温下进行了横向与纵向拉伸实验(结果如表 5 所示),研究发现纵向试样的拉伸性能优于横向,试样性能存在各向异性。 通过对增材制造试样显微组织形貌的分析可知,纵向试样的鱼鳞状熔池堆叠层数多于横向,纵向试样同层的条状熔池延伸距离比横向试样短,而横向和纵向显微组织之间的差异性,是造成试样纵向和横向拉伸性能差别的主要原因。
前已述及,因增材制造加工过程中冷却速率极快,沉积态的晶粒以具有显著外延性特征的柱状晶和等轴晶为主,组织中存在偏析所致的脆性 δ⁃Ni3Nb 相和 Laves 相。 此外,合金内部存在的微裂痕和宏观方面试样的残余内应力等因素,致使合金性能较低,选用合理的热处理工艺能够进一步提高材料的性能。 固溶处理、时效处理等能够改善合金组织,对合金拉伸性能有着不同程度的提高。 左蔚等[33] 研究了三种热处理条件(固溶、固溶+时效、直接时效)下 SLM 成形 K4202高温合金拉伸性能,如表 6 所示。 研究发现直接时效热处理可以获得优于传统固溶+时效热处理制得的室温拉伸性能,热处理后抗拉强度达 1 320.6 MPa,比沉积态提高了约 43%。
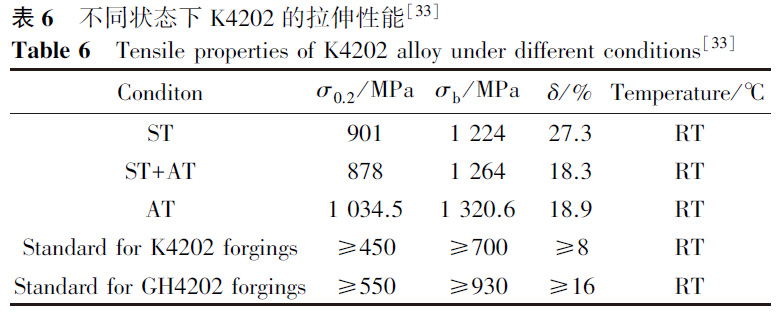
时效处理后试样拉伸性能较高是因为时效处理后试样晶粒的尺寸和形貌相对于沉积态变化不大,保留了大量的位错和晶界,阻碍了位错和滑移,使其强度得到提高。
通过分析不同的研究发现,相比于沉积态的力学性能,经过不同条件下热处理后的成形件各项力学性能(屈服强度、抗拉强度、硬度等)均能达到或超过锻件的标准,强度相比于沉积态零件有不同程度的提高。 相比于直接沉积的成形件,经过后处理后零件的综合性能有了较大的提升,可以满足不同领域的应用要求。
3、 现存难点
3.1 残余应力
残余应力的定义是材料内部处于平 衡 状 态 的 静 态 应力[34] 。 在增材制造过程中,局部快热或者快冷会产生较大的温度梯度,很容易形成热应力残留在成形件内部。 在特定的条件下残余应力释放时,会导致材料产生裂纹,影响材料的综合性能。 残余应力的产生因素主要有塑性变形、温度梯度和固态相变,通常残余应力的产生综合了这几种因素。 激光成形加热与冷却速度都极快,在激光增材制造加热过程中,不同位置温度不同,熔化不同步,冷却过程中凝固不同步,使得不同位置的膨胀与收缩具有不一致性,从而产生热应力。
在激光增材制造成形过程中出现或是在成形完成后马上出现的缺陷,主要与热应力有关[35] 。 金属激光增材制造过程中,应力的产生和演变规律与焊接过程相似,但由于激光增材多层堆积过程中各种条件的差异会使冷却过程不同,热过程差异造成应力演化、分布更加复杂,使得增材制造在逐层处理过程引入的残余应力既复杂又比较大。 通常,增材制造制备的成形件内部并不希望存在残余应力,因为它会降低成形件的疲劳性能与拉伸性能,最终导致成形件产生几何变形[36] 和裂纹。
目前,对控制和减少增材制造制备成形件中的残余应力方面已经做了大量的研究[37⁃39] 。 图 16[40] 为不同的残余应力测试技术对应的测试深度和分辨率。 对于高温合金盘锻件,需要测试分析距表层 10 mm 甚至更深的内部残余应力,分辨率要求为 mm 级,因此主要方法包括中子衍射法(Neutron dif⁃fraction)、 轮 廓 法 ( Contour method)、 深 孔 法 ( Deep⁃holedrilling)和超声法(Ultrasonic)。
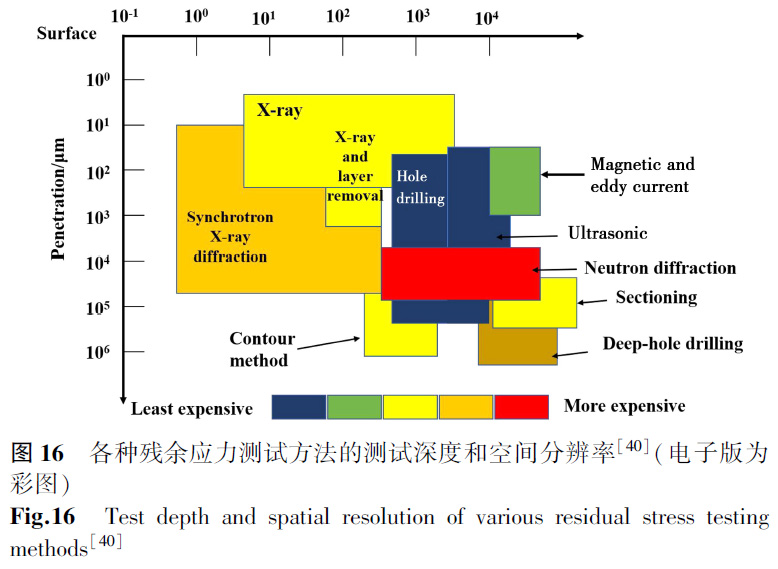
因此,残余应力的控制与消除决定着激光增材制造成形件质量的优劣。 增材制造主要分为预热、沉积、后处理三个部分,残余应力的形成与这几个过程都存在一定的关系。 通
常,对基板在 150~400 ℃进行预热可以减少成形件中的残余应力[41] 。 沉积部分主要是工艺参数的选择,合理的工艺参数能够有效地减少成形件的残余应力[42] 。 近年来科研专家还提出了许多后处理工艺方法以减少残余应力。 通过热处理来降低材料残余应力的方法有热等静压法、退火与固溶时效处理方式。 杨启云等[43] 测试了选区激光熔化制备 IN625 合金退火(1 140 ℃,2 h)前后的表面残余应力,发现残余应力由退火前的398MPa 减小到242MPa,降低了39.2%。 除此
之外,目前常用的有效调控方法还有以下几种:选择适当沉积方式;采用与打印材料同材质基材,减小热导率和热膨胀系数差而产生的残余应力;采用机械约束,对成形过程中产
生的翘曲变形进行严格控制等。 目前对增材制造中残余应力的演化规律的认识还存在不足,需要进一步探索更加简便、高效的处理方法以降低成形件中的残余应力。
3.2 孔隙
孔隙现象在增材制造成形件中普遍存在,它对成形件的综合性能有着极其重要的影响[34] 。 孔隙是在材料成形过程之中形成的,熔池内的气体在材料快速熔化和凝固时因来不及排出而残留于成形件内形成气孔,其形状通常为规则的球形且尺寸较小[44] 。 除此之外,雾化制备粉体材料时内部会不可避免地混入少量的保护气体[45] 。 在增材制造过程中,粉末熔化使得气体释放,若来不及排出则会在成形件内部形成气孔从而产生孔隙现象。 成形件内的气孔、裂纹与应力等都对孔隙的形成有一定影响。
目前,针对孔隙现象许多科研专家也提出了同的控制方法。 研究发现,实验前对基板进行预热可以减小与熔池之间的温度梯度,降低熔池的冷却速度使气体能够排除,以达到
减小成形件孔隙度的目的[46] 。 在增材制造过程中,选择合理的工艺参数对于减少成形件的孔隙度也有极其重要的作用。
此外,采用热等静压对成形件进行后处理,也能减少成形件的孔隙度。 Li 等[47] 对 SLM 制备的哈氏合金做了热等静压处理,结果证明热等静压能够有效地减少 SLM 成形件中的微裂纹和孔隙等缺陷,Tomus 等[25] 的研究结果也证明了这一点。
未来,对于孔隙率的控制仍需要进一步研究,对孔隙的处理方法需要进行针对性的探究。
3.3 微观结构的各向异性
一般而言,增材制造技术制备的成形件为柱状晶结构,且晶粒穿过多个熔覆层向上延伸。 较快的凝固速度以及垂直于基材方向的热损失使得晶粒在粉床中外延生长。 在选区激光增材制造制备的构件中可以观察到一些可变性的结构,这是通过使用棋盘式扫描策略导致形成嵌入在主要柱状晶区域中的近等轴晶区域[48] 。 更重要的是,由于该工艺的反
复加热性质,显微组织在几十微米尺度上也表现出不均匀性,这表现在所见的“鱼鳞”形貌和晶粒结构或偏析上的不均匀性[17,49] 。 晶粒结构中的各向异性本身不是问题,但是我们期望可以通过控制晶粒的各向异性来获得某些特定的力学性能,比如定向浇铸(Directionally cast, DS)获得结构的方向性。 通过调控工艺参数进而实现对晶粒尺寸和晶体取向的控制,增材制造技术在这方面具有很大的潜力。 但目前关于这方面的研究还非常少,其潜力还尚未被充分发掘,需要进一研究。
与微观结构相关的另一个难点是结构中快速凝固副产物的亚稳态性质。 大多数镍基高温合金增材制造成形件的结构要么表现出一定程度的枝晶间偏析,要么显现出其它不希望出现的凝固诱导相(如 Laves 相)[50] 。 因此,通常需要后处理来修复增材制造工艺引起的缺陷。 除了固溶和时效热处理外,还可以产生一定尺寸和比例的沉淀物来提高材料的高温特性。 然而,这些后处理操作会进一步增加增材制造工艺的成本,降低它们的吸引力。
4、结语
本文简述了激光增材制造的各种技术以及镍基高温合金的研究进展,综述了增材制造镍基高温合金成形件后处理前后的组织特征以及力学性能。
本文阐述了增材制造镍基高温合金成形件存在的缺陷及其形成的机理,概括了目前研究中针对这些缺陷所提出的解决方案,为后续的研究提供参考。
参考文献
【1】Liu K, Sun H J, Wang J, et al. Advanced Ceramics, 2017, 38(4), 286(in Chinese). 刘凯, 孙华君, 王江, 等. 现代技术陶瓷 , 2017, 38(4), 286.
【2】 Zhou R Y,Shuai M B, Jiang C. Materials Reports A:Review Papers,2016, 30(1), 67(in Chinese). 周汝垚, 帅茂兵, 蒋驰. 材料导报:综述篇 , 2016, 30(1), 67.
【3】Liao W J, Hu J. The Magazine on Equipment Machinery, 2015(1), 1(in Chinese). 廖文俊, 胡捷.装备机械 , 2015(1), 1.
【4】Liao W J, Fan E X, Fu C. Materials for Mechanical Engineering, 2018,42(7), 16 (in Chinese). 廖文俊, 樊恩想, 付超.机械工程材料 , 2018, 42(7), 16.
【5】Hu Z N, Zhang Y T, Wang N N. Shandong Coal Science and Technolo⁃gy, 2014(8), 95 (in Chinese). 胡振南, 张玉堂, 王娜娜.山东煤炭科技 , 2014(8), 95.
【6】Lan F, Liang Y J, Huang B B. Equipment Manufacturing Technology,2018(5), 43(in Chinese). 兰芳, 梁艳娟, 黄斌斌.装备制造技术 , 2018(5), 43.
【7】Le G M, Li Q, Dong X F, et al. Rare Metal Materials and Engineering,2017, 46(4), 1162(in Chinese). 乐国敏, 李强, 董鲜峰, 等. 稀有金属材料与工程 , 2017, 46(4),1162.
【8】Yao F L. Mechanical Management and Development, 2019(8), 116(inChinese). 姚福龙.机械管理开发 , 2019(8), 116.
【9】 Wang D, Qian Z Y, Dou W H, et al. Aeronautical Manufacturing Tech⁃nology, 2018, 61(10), 49 (in Chinese). 王迪, 钱泽宇, 窦文豪, 等.航空制造技术 , 2018, 61(10), 49.
【10】Tang Z J, Guo T M, Fu Y, et al. Metal World, 2014, 1(4), 36 (inChinese). 唐中杰, 郭铁明, 付迎, 等.金属世界 , 2014, 1(4), 36.
【11】Wu K, Zhang J L, Wu B, et al. Journal of Iron & Steel Research, 2017,
29(12), 953.
【12】Gan Z, Liu H, Li S, et al. International Journal of Heat and Mass Trans⁃fer, 2017, 111, 709.
【13】Seidel A, Finaske T, Straubel A, et al. Metallurgical and MaterialsTransactions: A, 2018, 49(9), 3812.
【14】Zhang Y Z, Hou H P, Peng S, et al. Journal of Aeronautical Materials,2018, 38(6), 50 (in Chinese). 张永志, 侯慧鹏, 彭霜, 等.航空材料学报 , 2018, 38(6), 50.
【15】Wu W H, Yang Y Q, Mao G S. Manufacturing Technology & MachineTool, 2014(4), 46 (in Chinese). 吴伟辉, 杨永强, 毛桂生.制造技术与机床 , 2014(4), 46.
【16】Chen M Y, Bai P C, Zhang A F, et al. Materials Reports, 2015, 29(20), 105 (in Chinese). 陈梦洋, 白朴存, 张安峰, 等.材料导报 , 2015, 29(20), 105.
【17】Vilaro T, Colin C, Bartout J D, et al. Materials Science and Engineering: A, 2012, 534, 446.
【18】Chen X J, Zhao G R, Dong D D, et al. Chinese Journal of Lasers, 2019,46(12), 1202002(in Chinese). 陈秀娟, 赵国瑞, 董东东, 等.中国激光 , 2019, 46(12), 1202002.
【19】Choi J P, Shin G H, Yang S, et al. Powder Technology, 2017, 310, 60.
【20】Zuo W, Zhang Q M, Wu W J, et al. Journal of Rocket Propulsion, 2017,43(1), 55 (in Chinese). 左蔚, 张权明, 吴文杰, 等.火箭推进 , 2017, 43(1), 55.
【21】Lin X, Yang H O, Chen J, et al. Acta Metallurgica Sinica, 2006, 42(4), 361(in Chinese). 林鑫, 杨海欧, 陈静, 等.金属学报 , 2006, 42(4), 361.
【22】 Lv H , Yang Z B, Wang X, et al. Chinese Journal of Lasers, 2018, 45
(10), 1002003(in Chinese). 吕豪, 杨志斌, 王鑫, 等.中国激光 , 2018, 45(10), 1002003.
【23】Chlebus E, Gruber K, Kuznicka B, et al. Materials Science and Engi⁃neering: A, 2015, 639 (15), 647.
【24】Brynk T, Pakiela Z,Ludwichowska K. Materials Science and Engineering: A, 2017, 698, 289.
【25】Tomus D, Yang T, Rometsch P A, et al. Materials Science and Enginee⁃ring: A, 2016, 667 (14), 42.
【26】Li Y L, Lei L M, Hou H P, et al. Journal of Materials Engineering,2019, 47(5), 100 (in Chinese). 李雅莉, 雷力明, 侯慧鹏, 等.材料工程 , 2019, 47(5), 100.
【27】Deng X Y, Lu S Q, Wang Y C, et al. Special Casting & Nonferrous Al⁃loys, 2017, 37(8), 878 (in Chinese). 邓晓阳, 鲁世强, Wang Yachao, 等.特种铸造及有色合金 , 2017, 37
(8), 878.
【28】 Huang W P, Yu H C, Yin J , et al. Acta Metallurgica Sinica, 2016, 52(9), 1089 (in Chinese). 黄文普, 喻寒琛, 殷杰,等.金属学报 , 2016, 52(9), 1089.
【29】Graybill B, Li M, Malawey D, et al. In: ASME 2018 13th InternationalManufacturing Science and Engineering Conference, 2018, pp. 1.
【30】Zhao W W, Lin X, Liu F C, et al. Chinese Journal of Lasers, 2009, 36(12), 3220 (in Chinese). 赵卫卫, 林鑫, 刘奋成,等.中国激光 , 2009, 36(12), 3220.
【31】 Pang X T, Cheng X, Tian X J, et al. Rare Metal Materials and Enginee⁃ring, 2019(5), 1615(in Chinese). 庞小通, 程序, 田象军, 等.稀有金属材料与工程 , 2019(5), 1615.
【32】Liu K, Wang R, Qi H, et al. Physical Testing and Chemical Analysis(Part A:Physical Testing), 2019, 55(1), 15(in Chinese). 刘凯, 王荣, 祁海, 等.理化检验:物理分册 , 2019, 55(1), 15.
【33】Zuo W, Zhang Q M, Lei Y, et al. Journal of Rocket Propulsion, 2017,43(3), 53 (in Chinese). 左蔚, 张权明, 雷玥, 等.火箭推进 , 2017, 43(3), 53.
【34】Yao Y S, Wang J, Chen Q B, et al. Laser & Optoelectronics Progress,2019, 56(10), 45 (in Chinese). 姚燕生, 汪俊, 陈庆波, 等.激光与光电子学进展 , 2019, 56(10),
45.
【35】 Du C, Zhang J, Lian Y, et al. Surface Technology, 2019, 48(1), 200(in Chinese). 杜畅, 张津, 连勇, 等.表面技术 , 2019, 48(1), 200.
【36】 Moat R J, Pinkerton A J, Li L, et al. Materials Science and Engineering: A, 2011, 528(6), 2288.
【37】Parimi L L, Attallah M M, Gebelin J, et al. Superalloys 2012, 2012,509.
【38】Klingbeil N W, Beuth J L, Chin R, et al. International Journal of Me⁃chanical Sciences, 2002, 44(1), 57.
【39】Prabhakar P, Sames W J, Dehoff R, et al. Additive Manufacturing,2015, 7, 83.
【40】Bi Z N, Qin H L, Dong Z G, et al. Acta Metallurgica Sinica, 2019, 55(9), 1160 (in Chinese). 毕中南, 秦海龙, 董志国, 等.金属学报 , 2019, 55(9), 1160.
【41】Zhang J, Li S, Wei Q S, et al. Chinese Journal of Rare Metals, 2015, 39(11), 961 (in Chinese). 张洁, 李帅, 魏青松, 等.稀有金属 , 2015, 39(11), 961.
【42】Vrancken B, Cain V, Knutsen R, et al. Scripta Materialia, 2014, 87(1), 29.
【43】Yang Q Y, Wu Y D, Sha F. Materials for Mechanical Engineering,2016, 40(6), 83 (in Chinese). 杨启云, 吴玉道, 沙菲.机械工程材料 , 2016, 40(6), 83.
【44】Ahsan M N, Pinkerton A J, Moat R J, et al. Materials Science and Engi⁃neering: A, 2011, 528 (25⁃26), 7648.
【45】Shi Q, Gu D, Xia M, et al. Optics & Laser Technology, 2016, 84, 9.
【46】 Yuan X B, Wei Q S, Wen S F, et al. Hot Working Technology, 2014, 43(4), 91(in Chinese). 袁学兵, 魏青松, 文世峰, 等.热加工工艺 , 2014, 43(4), 91.
【47】Li Y, Qi H, Hou H, et al. Materials and structural engineering (IC⁃MMSE 2017), Atlantis Press, 2017.
【48】Carter L N, Martin C, Withers P J, et al. Journal of Alloys and Com⁃pounds, 2014, 615, 338.
【49】Amato K N, Gaytan S M, Murr L E, et al. Acta Materialia, 2012, 60(5), 2229.
【50】Parimi L L, Ravi G A, Clark D, et al. Attallah, Materials Characteriza⁃tion, 2014, 89, 102.
相关链接