溅射靶材是电子信息产业的关键原材料之一,其产品质量关系到溅射薄膜的品质和溅射设备的安全。溅射靶材种类繁多l1 ]。从材质来说,包括铝及铝合金、铜及铜合金、镍及镍合金、铬、钼、钛、钨及钨合金、金、银、铂、钽、硅、二氧化硅、氧化铟锡、二氧化锡、铁基合金和稀土等。从靶材原始坯料的制造方法来分,主要有熔铸靶和粉末靶;从有无背板的角度来分,主要是焊接靶和单体靶。熔铸靶材的制造流程一般包括以下四步:化学提纯制备高纯原材料、熔炼铸造制备铸坯、塑性加工(锻造、挤压和轧制)与热处理、最后是机械加工。难熔金属靶材、熔点相差很大的金属合金靶材和陶瓷靶材坯料一般采用粉末法制备坯料。其关键制造流程是:制粉、粉末冶金制坯或直接喷涂成型、对坯料进行切割、机械加工成品。上述两大靶坯制造流程中,除提纯、制粉和机械加工外的其他制造工序都是容易产生内部缺陷的高风险工艺。靶材内部缺陷的存在将会在溅射过程中产生颗粒或飞溅,从而降低薄膜质量。对于焊接靶材,焊接质量关系到溅射靶材与背板之间的焊接强度和溅射过程中靶材散热,无论是对于溅射设备安全还是溅射薄膜质量,焊接质量都是衡量溅射靶材质量是否合格的关键指标之一。因此,在溅射靶材的制造过程中采用无损检测技术成为确保制备合格溅射靶材的必要措施。

1、铸坯与粉末冶金坯料的检验
靶材制造用铸坯中的缺陷包括气孔、夹渣、疏松和裂纹等,多是体积型缺陷。对于铝及铝合金靶材来说,还存在氧化铝颗粒的检测问题。如果带有缺陷的铸坯进入制造流程中,最终的靶材可能完全不合格。因此在下料前必须对铸锭进行内部缺陷检验。X射线检测技术和超声波检测技术都可以进行材料内部缺陷检验,但其适用性取决于铸坯的材质。
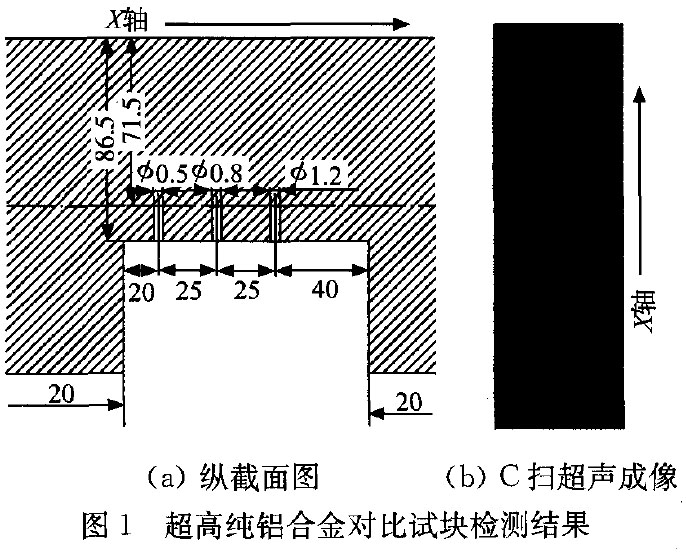
试验发现,超声波在超高纯铝及合金(>5N,99.999wt %)铸坯中传播时,衰减较小,也不存在由于晶粒粗大导致的晶界散射现象 。图1所示为设计的铝合金铸坯对比试块轴向截面图和超声C扫图像,检测频率为10 MHz,探头晶片直径0.375×25.4 mm,探头焦距为4×25.4 mm。可以看出,水浸C扫超声波技术可以有效满足铝及铝合金铸锭内 0.5 mm平底孔当量的缺陷检测要求。检验质量验收标准如表1所示。
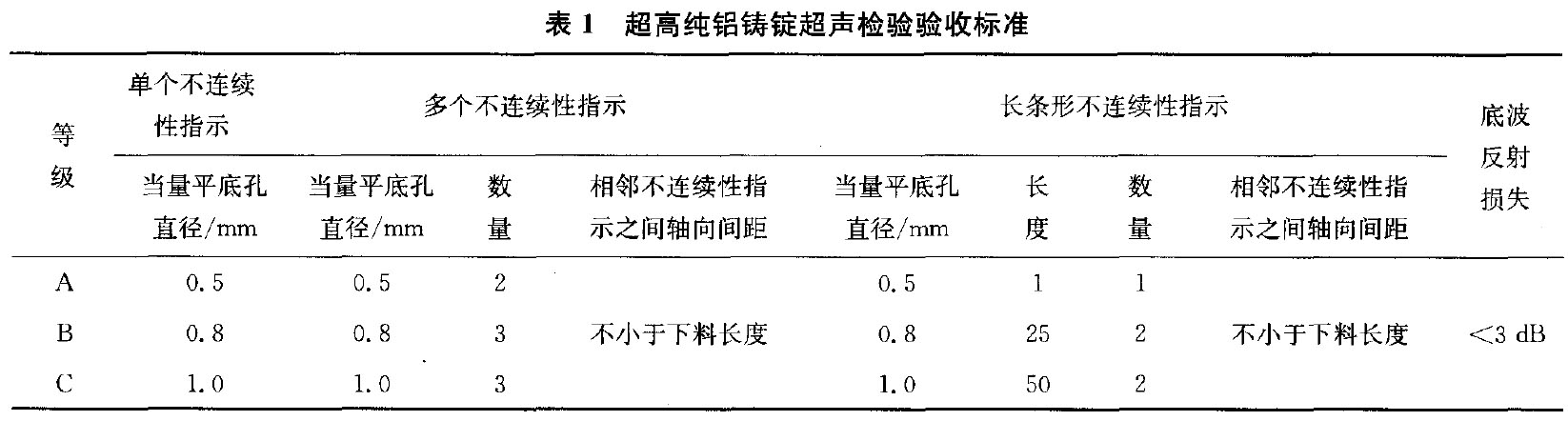
超高纯铜(≥6 N)铸坯和超高纯镍(≥5 N)铸坯的晶粒尺寸巨大,都是厘米量级,主要是因为铸造过程中缺少型核质心导致过低的形核率而造成的。
通过对两者的铸坯进行超声波检验发现,两者都不适合采用超声波检验技术进行内部缺陷检验,但其原因却完全不同。
超声波在超高纯铜中传播时存在两个问题:一是衰减严重;二是晶体取向的影响。首先,采用USN60超声探伤仪和5 MHz纵波直探头,以82 dB的增益检验上下表面平行的150 mm厚铸锭(表面粗糙度<1.6μm)时,只能观察到一次底波且波幅不超过满屏的10%,表明超声波衰减严重,无法对铸锭进行有效检测。其次,在利用水浸C扫描技术采用2.25 MHz 4×25.4 mm焦距探头对75 mm厚高纯铜铸锭进行检测时发现,检测入射面不同区域的底波显示的厚度与实际厚度存在较大差别,如图2所示。不同区域的C扫测量厚度的差异表明不同区域之间的声速存在差别,与标准声速相比最大可以增大约24.56 。这种现象主要是由于铸锭内晶粒尺寸的巨大引起的。超声波在介质中传播的声速与介质的弹性模量E有关。对于晶粒细小的多晶材料,由于晶体取向是随机的,因此材料整体表现为各向同性,其弹性模量也是各向同性,超声波在其中传播的声速也各向相等。但对于单晶材料,其弹性模量与晶体取向有关。超声波在晶粒粗大的超高纯铜铸锭中传播时,实质是在不同晶粒内的传播。各个晶粒的取向都存在差异,由此导致了各区域声速的不同。这种晶体取向导致声速的差异为利用超声波检测超高纯铜铸锭内部缺陷增加了新的困难。
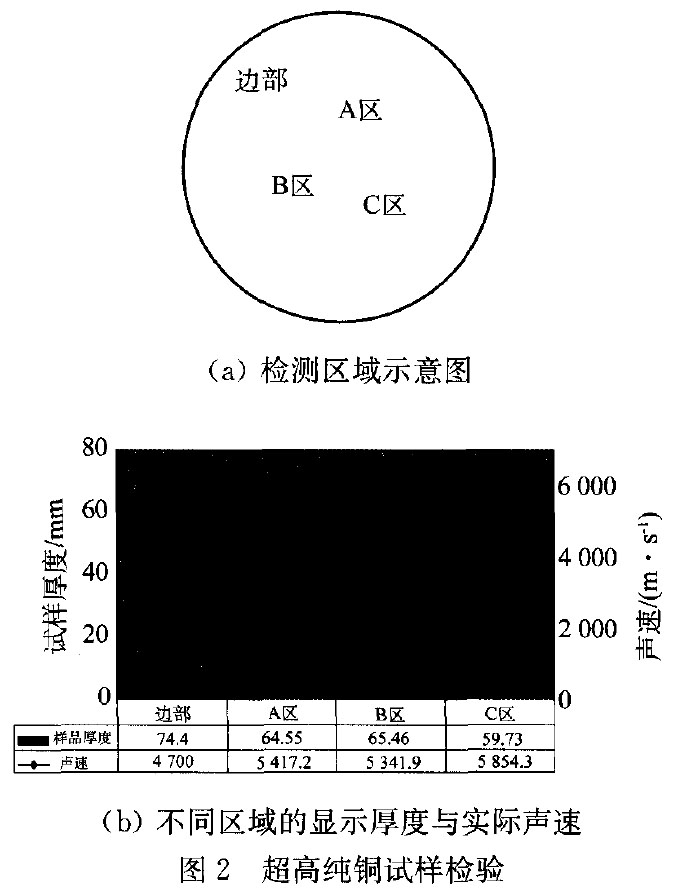
与超高纯铜铸锭明显不同,超声波在高纯镍中的衰减并不明显,其主要问题是粗大晶粒导致的晶界散射。将高纯镍铸锭切割成薄片,表面处理后粗糙度<1.6μm。然后分别采用x射线检测技术和超声波检测技术对该切片进行检测。对比发现两种方法的检验结果并不相符,X射线判定切片中无缺陷的区域,超声波检验时判定存在缺陷。经解剖并逐层磨制观察,确认这些区域不存在缺陷,而是晶界,如图3所示。说明超纯镍铸锭中晶界散射对超声波检验存在严重干扰而无法进行有效判定。综上所述,对于高纯铜和高纯镍铸锭的内部缺陷,超声波检测存在局限,x射线技术更适用。
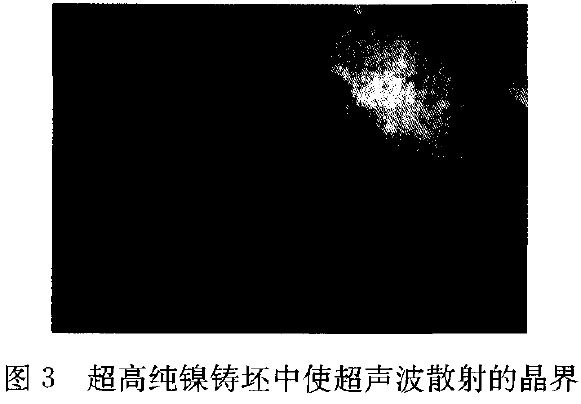
粉末法制备的靶材坯料一般超声波声学特征较好,且晶粒尺寸细小,因此,多数可以适用于超声波检测技术。
粉末法制备的坯料,无论是粉末冶金法还是喷涂法,其内部缺陷主要包括裂纹、空洞、夹杂和不致密。与铸锭内的球形或长条形空洞不同,粉末法坯料中的空洞和夹杂主要是不规则形状,其形状与夹杂物的形状相同。因此,空洞、夹杂和裂纹在粉末坯料中可以任意方向,必须从多个角度进行检测才能确保无遗漏。对于不致密则主要是观察底波损失来判定。一般如果某区域底波损失超过4dB,即可判定该区域不致密。
2、塑性加工靶坯的检验
除少数铸造靶材和直接喷涂成型靶材外,大多数靶材都是通过一系列塑性加工和热处理制成。塑、性加工方法包括热锻、冷锻、热轧制、冷轧制、模压、挤压和拉伸等。热处理包括固溶处理、正火、退火、淬火和时效等。理论上每个工序后都应该进行检验,但考虑到生产效率,一般在加工完成后对最终的靶材板坯进行检验。
经过上述工艺加工后,靶材板坯的显微组织得到了显著细化,板坯厚度为3~40 mm之间,超声波声学特征良好。在上述加工过程中,靶材板坯内可能形成的缺陷包括裂纹、分层、夹杂、折叠、过热、晶粒粗大、过烧、白点和疏松等。除裂纹外,这些缺陷有个共同的特征,即呈线性平面形状,方向沿塑性加工的流线方向,且与塑性加工平面平行。显然,超声波检测技术对此类特征的缺陷最为灵敏。因此靶材内部缺陷的检验与评判一般都采用超声纵波脉冲反射式水浸C扫检测技术。检测时一般将超声波焦点聚焦到靶坯厚度的中间位置。
评判验收标准与靶材的应用等级有关。根据验收要求设计加工人工平底孔对比试块即可。表2列出了当前通用的靶材坯料内部验收标准。
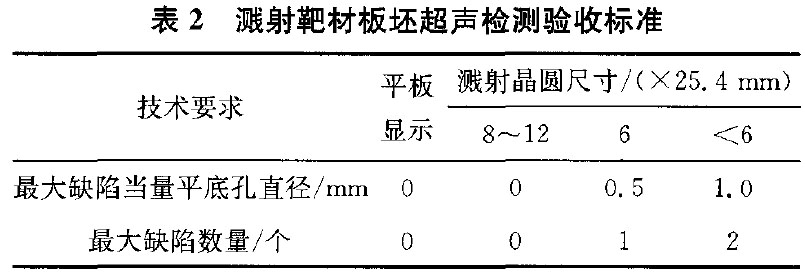
3、焊接质量检验
出于降低成本和增强板材组件强度和导热性能要求,多数溅射靶材采用了与冷却背板焊接的形式,尤其是大尺寸靶材。溅射靶材的背板一般采用铝合金、铜合金、钼或者不锈钢等,其构型有的简单,只是一块具有一定硬度、强度和厚度的圆形或者矩形板材;有的构型复杂,内部带有复杂的冷却水道。
溅射靶材与背板的焊接是在对溅射靶材板坯完成机械加工后进行,使用的焊接技术包括钎焊、电子束焊、扩散焊和爆炸焊等。
真空电子束焊接形成的焊缝中可能存在的缺陷有裂纹、空洞、夹杂、未熔合和未焊透等。根据使用环境的技术要求来确定针对真空电子束焊接质量的检验方法。
钎焊、扩散焊和爆炸焊应用于靶材时,焊接方式基本都是两个平面之间的焊接。钎焊是采用中间材料将两工件进行粘接的连接方式,中间材料(即钎焊焊料)包括铟和锡基焊料等低温焊料。存在的焊接缺陷主要是未粘接和夹杂。
扩散焊过程较为复杂,焊接面还要进行特殊处理,如喷砂毛化或者车齿。毛化或者车齿后的焊接界面本身就存在着缺陷——微小尺寸的裂隙,一般为百微米量级。因此扩散焊检测的主要是尺度较大的,如毫米量级的未焊合。爆炸焊和扩散焊相似。
无论是钎焊、扩散焊还是爆炸焊,其焊接缺陷具有共同的特征,即线状平面型缺陷。因此主要采用超声纵波C扫描技术进行检验和评判。
焊接检验用对比试块的设计与加工技术要求可以参考ASTM F1512标准。对于钎焊来说,一般选择10 MHz的水浸聚焦探头进行检验。而对于对扩散焊,超声波频率的选择则必须考虑焊接界面特征。另外,钎焊与扩散焊的质量验收标准也存在差别。
表3列出了钎焊和扩散焊焊接质量的验收标准。显然扩散焊的验收要高于钎焊。
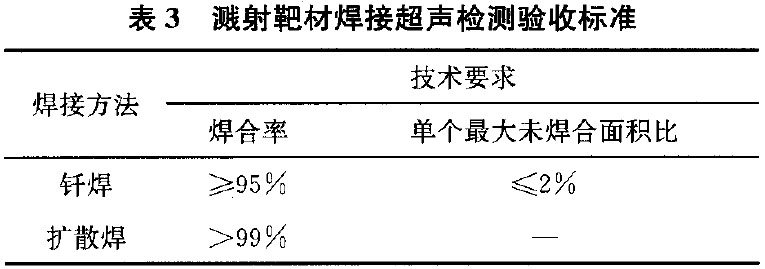
4、结语
当前X射线检测技术和超声波检测技术基本可以满足靶材制造的检测要求。除铸锭原材料外,超声波检测技术在溅射靶材制造中应用得更为广泛。超声波检测工序的安排要兼顾产品质量和生产效率。靶材板坯和焊接质量的检验方法主要是超声纵波脉冲反射C扫描技术。溅射工艺的要求导致靶材检验的验收标准十分严格。
参考文献:
【1】陈建军,杨庆山,贺丰收.溅射靶材的种类、应用、制备及发展趋势【J】.湖南有色金属,2006,22(04):38—76.
【2】金永中,刘东亮,陈建.溅射靶材的制备及应用研究[J].四川理工学院学报(自然科学版),2005,18(3):22
【3】努力古.溅射靶材的制备及发展趋势【J】.新疆有色金属,2008(5):55—56.
【4】尚再艳,江轩,李勇军,等.集成电路制造用溅射靶材【J】.稀有金属,2005,29(4):475—477.
【5】刘志坚,陈远星,黄伟嘉,等.溅射靶材的应用及制备初探[J].南方金属,2003,135:23—32.
【6】Wickersham C E,Poole Jr J E,Leybovich A,et a1.Measurements of the critical inclusion size for arcingand macroparticle ejection from aluminum sputteringtargetsVJ,1.J Vac Sci Technol A,2001,19(6):2767—2772.
【7】Wickersham C E,Poole Jr J E,Fan J S.Arc genera—tion from sputtering plasma-dielectric inclusion interae—tionsVJ].J Vac Sci Technol A,2002,20(3):833—838.
【8】Wickersham C E,Poole Jr J E,Fan J S,et a1.Videoanalysis of inclusion induced macroparticle emissionfrom aluminum sputtering targets[J].J Vac Sci Tech—nol A,2001,19(6):2741—2750.
【9】 Gary S Selwyn,Corey A Weiss,Federico Sequeda,eta1. Particle contamination formation in magnetronsputtering processes[J].J Vac Sci Technol A,1997,15(4):2023— 2028.
【10】Vikram Pavate,Murali Abburi,Sunny Chiang,et a1.Correlation between aluminum alloy sputtering target
metallurgical characteristics[J].Arc initiation and InfilmDefect Density,1997(3214):42— 47.
【11】Paul S Gilman,Alfred Snowman,Andre Desert.De—termination of actual defect size in cathode sputtertargets subjected to ultrasonic inspection: US,
6269699 B1EP].2001.
【12】 Charles E Wickersham,John E Poole,AlexanderLeybovich,et a1.M ethod for determing a critical sizeof an inclusion in aluminum or aluminum alloy sputte—ring target:US,7087142 B2[P].2006.
【13】 Charles E Wlckersham JR,John E Poole,AlexanderLeybovich,et a1.Method for determing a critical sizeof an inclusion in aluminum or aluminum alloy sputte—ring target:US,2004/0118675 AI[P].2004.
【14】Russell B Gore,Ronald H Fleming.Methods of tes—ting sputtering target materials: US, 6439054 B1[-P1.2002.
【15】Charles E Wlckersham JR,John E Poole,AlexanderLeybovich,et a1. Sputter targets and methods ofmanufacturing same to reduce particulate emission
during sputtering:US,2002/0184970 A1I-p].2002.
【16】Hidemasa Tamura,Norio Yokoyama,Eiichi Shimi—ZU,et a1. Sputtering target and production method
thereof:US,6024852[P,1.2000.
【17】陈岳军,赵海燕,史耀武.粗晶材料超声检测缺陷信号增强的小波分析法[J].中国有色金属学报,1997,7(2):94— 96.
相关链接