引言
近年来,采用微米级发光二极管 (mini light emitting diode,Mini-LED) 显示技术的产品逐渐普及,其产品主要应用于中大型屏幕的拼接显示场景,主要分为背光式和直显式产品两类,其中直显式产品通过将微型化显示芯片直接封装于显示基板,形成超高密度像素阵列以实现画面呈现。根据近年公开的技术资料,行业主流技术路线多以印制电路板 (printed circuit board,PCB) 作为基板载体,但受限于 PCB 的材料特性、制程工艺等,其显示效果存在明显不足,尤其是拼接显示时的边框宽度和视觉一致性较差,难以满足近距离、高画质的观看要求。因此,开发一种无拼接边框、支持高画质近距离观看的显示产品至关重要。相对于 PCB 基板,玻璃基板具有更高的工艺精度、更好的黑化效果及对比度和平整度。因此,本研究以玻璃基板替代传统 PCB 基板,拟开发一套玻璃基多层金属膜制备技术,通过对基板玻璃进行加工,使驱动面板的线路沿玻璃侧边沉积,从而实现屏幕无缝拼接,以期推动大尺寸屏幕在显示效果、近距离观看体验等方面的跨越式提升。
1、 Mini-LED 技术原理
1.1 Mini-LED 显示屏简介
Mini-LED 显示技术作为一种新型显示技术,采用 50~200μm 的小型化 LED 芯片,通过缩小相邻像素点距离、精确控制每个 LED 的色彩与亮度,实现高对比度和高动态范围的显示画质 [1]。主要分为直显式产品和液晶显示背光用产品两类,目前已广泛应用于电视、笔记本电脑、户外大屏、安防应急指挥中心、虚拟现实和增强现实等领域,极大地提升了设备的显示效果与用户体验。Mini-LED 显示的主要技术优势在于可实现极高的对比度,使画面更为生动;可实现更精细的局部调光,提升画面亮度和暗度表现,进而呈现出更为真实的画面效果 [2-3]。另外,Mini-LED 显示具有极高的亮度,即使在阳光直射的环境下,依然可以呈现清晰的画面。而且,Mini-LED 显示具有较低的能耗和较长的使用寿命,不易出现烧屏、残影等问题,极大地降低了设备维护成本。
其中,Mini-LED 直显式产品通过将微型化 RGB 显示芯片直接封装于基板,形成超高密度像素阵列以实现画面呈现,可满足任意大小的无缝拼接以及高品质、近距离、超大尺寸的显示需求。随着像素间距的不断缩小,像素密度将不断增加,这对 PCB 基板的加工精度提出了极高要求。在此趋势下,基于 PCB 基板的 Mini-LED 产品逐渐失去优势,其极小线宽的技术要求使得生产难度陡增。在中型尺寸高画质显示面板领域,基于玻璃基板的 Mini-LED 产品成为更理想的选择,其不仅具备优异的导热性能,还具有出色的热稳定性和极小的形变量,同时能保证基板的高度平整性。特别值得注意的是,在玻璃基底无缝拼接式 Mini-LED 产品开发中,为实现极窄无缝显示效果,需要将驱动 IC 和控制单元全部设计在基板背面,这种特殊结构使得如何通过产品和工艺设计实现驱动单元与发光单元的有效连接成为核心技术难题。
1.2 玻璃基 Mini-LED 显示技术
1.2.1 侧边工艺对比
为实现正面发光单元和背面驱动单元的有效连接,常规的工艺技术路线包括柔性 PCB (flexible PCB,FPCB) 绑定技术、挖孔刻蚀技术和传统平面磁控溅射镀膜技术等。然而,这些技术均存在各自的应用局限性。例如,FPCB 绑定技术需将电路板在显示屏幕正面绑定后再弯折至背面进行驱动连接,这势必会造成显示屏幕的黑边框宽度增加;挖孔电镀沉积金属技术面临玻璃基材挖孔效率低下且平面磁控溅射设备难以实现深孔台阶覆盖等技术瓶颈,无法满足大规模高效生产需求。因此,针对玻璃基材的极窄边框显示产品线路制备问题,亟须开发新型制备工艺技术。本研究提出的 3D 磁控溅射设备与工艺可有效解决上述瓶颈问题,为玻璃基底 Mini-LED 显示屏幕实现极窄边框设计路线提供创新解决方案。该技术主要应用于驱动和通信金属线路的沉积制备,可实现屏幕侧面连接线路的高效制备,不仅能够达到无缝拼接的显示效果,而且更具备产业化大规模应用潜力。
1.2.2 3D 磁控溅射技术原理
3D 磁控溅射镀膜技术是物理气相沉积 (physical vapor deposition,PVD) 技术的一种,PVD 是在真空条件下,通过材料源表面的气化 (形成气体原子、分子或部分电离成离子) 过程,基于低压气体和等离子体作用,在基体表面沉积功能性薄膜的技术 [4]。其基本工艺过程可概括为 3 个关键阶段:其一,通过蒸发、升华或溅射等过程使粒子从原材料中脱离;其二,粒子间发生碰撞,产生离化或复合等反应并传输至基底层;其三,粒子在基片表面凝结、成核、生长和成膜。在实际溅射工艺中,通常利用电场加速的正离子轰击靶电极 (阴极), 诱导其原子发生溅射。该过程依赖于气体的辉光放电现象。溅射方法种类较多,具有高速、低温、低损伤 [5] 等显著优势。
如图 1 所示,3D 磁控溅射系统的核心特征在于:在靶材背面施加相互垂直的电磁场 (靶材为阴极,基底为阳极), 垂直于电场方向分布的磁力线将电子约束在靶材表面附近做螺旋进动位移,可有效延长其在等离子体中的运动轨迹和路径,提高电子与氩气分子的碰撞概率。同时,受正交电磁场束缚的电子只能在其能量耗尽时湮没在衬底上,在电场 E 的作用下,电子与氩原子碰撞并发生电离,产生 Ar + 和新电子。新电子飞向衬底,Ar + 在电场作用下加速飞向阴极靶材,高速轰击靶材,引生溅射现象。靶材原子产生的二次电子沿 E×B 方向漂移。经多次碰撞后,二次电子能量下降,逐渐远离靶表面,最终沉积在衬底上 [6-8]。上述反应原理使得磁控溅射具有低温、高速的显著优势,同时电子对玻璃基底的轰击能量小,可减少基底损伤,避免基底温升过高,降低薄膜污染的可能性 [9]。
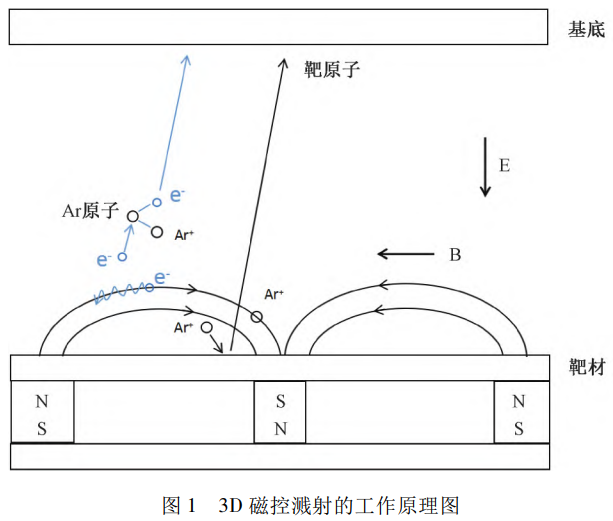
2、 侧边金属线路工艺设计与制作
2.1 设备硬件设施布局与相关性能指标
根据玻璃基 Mini-LED 显示器件的应用场景需求,本研究设计出可 3D 沉积 Mini-LED 侧面金属线路的专用设备,进行侧边线路的 PVD 镀制铜金属薄膜,实现正面显示像素与背面控制单元的回路连接,设备型号为 POWERTECH SP-0606SI 型,设备的硬件结构示意图如图 2 所示,主要包括真空腔室和泵组系统、测量系统、2 套离子电源、2 套直流电源、2 套高压电弧电源、1 套偏压控制系统、反应气体回路等 [10]。
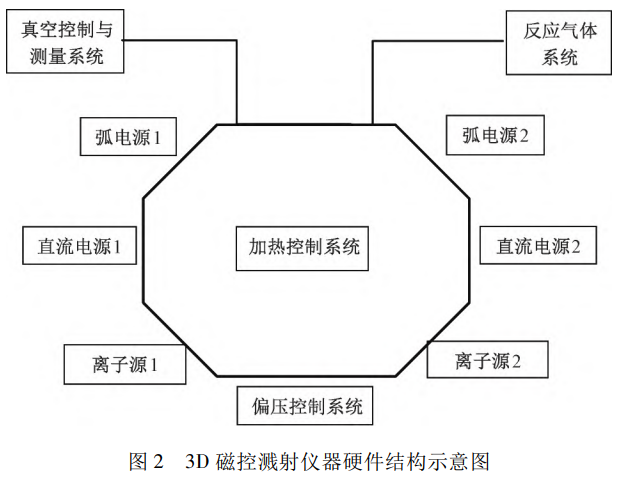
设备相关性能参数如下:腔室真空系统真空能力为 5×10-5~Pa; 反应气体流量系统型号为 Area FC-R7700, 量程 0.6~300 L/H; 离子电源型号为 SP-485 系列,输出最大电压为 DC 1600 V, 输出最大功率为 5 kW; 弧电源型号为 SP-3A150, 工作电压为 16~30 V 最大输出电流≤150 A; 直流电源型号为 AE-PNCL12k, 最大输出功率为 12 kW, 工作设定电压为 800 V。
工艺设施特殊要求如下:实施镀膜工艺时,样品需放置在腔室中心可旋转的偏压转架上,保证导电良好,各靶材依次环绕腔室分布,当对应的靶材开始工作时,样品镀膜区域可定向旋转到靶材正对面位置;直流电源 1 连接直流铜靶材,直流电源 2 连接钛靶材,这 2 套靶材设计有可移动式电机,可以根据样品在腔室中旋转角度进行前后移动,调节靶基距离,以实现更高的镀膜精度和正背面更好的台阶覆盖性。基于该设备可针对性地在 Mini-LED 显示屏幕的侧面镀制驱动和通信线路,实现正面 - 侧面 - 背面的线路连接和导通,最大程度缩小显示屏幕边框,极大提高屏占比。
2.2 工艺条件设计与样品制作
设计好设备硬件设施后,根据 Mini-LED 电路系统选择金属线路的材质,侧边线路对导电性要求较高,要求阻抗 < 35 mΩ, 故使用金属铜而非金属铝进行导电连接,但是由于金属铜的防腐蚀能力较差,其表面需覆盖抗腐蚀性能优异的保护金属,而金属钛具有优异的抗腐蚀能力,因此整个侧边线路选用金属铜和金属钛进行镀制,以实现导电性与防腐蚀性的平衡。
为验证工艺可行性,在设备调试完成后,选用预置电路布线的玻璃基板进行艺参数优化实验,具体实验设计如表 1 所示。第 1 组样品在玻璃基底上分别镀纯铜膜层 (样品 1-1)、纯钛膜层 (样品 1-2); 第 2 组样品在玻璃基底上镀钛 + 铜膜层 (样品 2-1); 第 3 组样品在玻璃基底上分别镀钛 + 钛铜合金 + 铜 (样品 3-1)、钛 + 钛铜合金 + 铜 + 铜钛合金 + 钛 (样品 3-2)、在玻璃基板上镀弧靶钛 + 钛 + 钛铜合金 + 铜 + 铜钛合金 + 钛 (样品 3-3)[11]。
表 1 工艺与膜层结构设计
样品编号 | 直流铜靶 | 直流钛靶 | 弧钛靶 | 离子源 | 偏压 | 膜层 | 样品数量 / 片 |
1-1 | 1 | 0 | 0 | 开 | 开 | 纯铜 | 10 |
1-2 | 0 | 1 | 0 | 开 | 开 | 纯钛 | 10 |
2-1 | 2 | 1 | 0 | 开 | 开 | 钛 + 铜 | 10 |
3-1 | 2、3 | 1、2 | 0 | 开 | 开 | 钛 + 钛铜合金 + 铜 | 10 |
3-2 | 2、3、4 | 1、2、4、5 | 0 | 开 | 开 | 钛 + 钛铜合金 + 铜 + 铜钛合金 + 钛 | 10 |
3-3 | 3、4、5 | 2、3、5、6 | 1 | 开 | 开 | 弧靶钛 + 钛 + 钛铜合金 + 铜 + 铜钛合金 + 钛 | 20 |
注:数字表示镀制工艺顺序。
3 、黏附力测试结果与分析
3.1 黏附力测试标准与结果分析
样品制备完成后,采用统一制式的 3M-2214 型胶黏带进行黏附力测试,测试方法如图 3 所示。
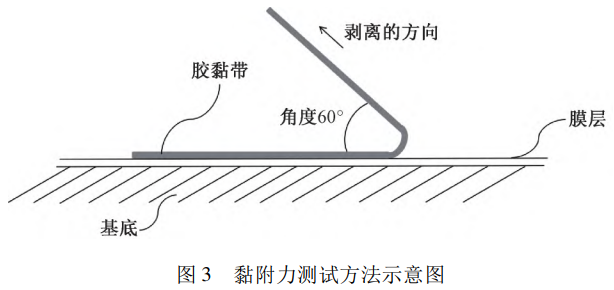
具体测试方法:将胶黏带放在样品膜层中心,用手指将胶黏带与膜层接触部位压平,胶黏带超出接触部位 10 mm。为确保胶黏带与膜层接触良好,用手指尖轻压胶黏带,保证胶黏带与膜层全面接触。在贴上胶黏带 1 min 内,拿住胶带悬空的一端,以接近 60° 的角度,在 0.5~1 s 内匀速撕开胶黏带。测试完成后使用基恩士超景深显微镜 VHX-7000 进行高倍率成像,观察样品黏附力情况,并记录正 - 背 - 侧面的金属膜层脱落面积比例。参考《色漆和清漆划格实验》(GB/T 9286-2021) 等相关标准制定测试标准:A 级,没有任何剥离,黏附力极好;B 级,只有微量剥离,脱落比例 < 5%, 黏附力良好;C 级,部分剥离,脱落比例 5%~15%, 黏附力一般;D 级,大部分剥离,脱落比例 15%~35%, 黏附力较差;E 级,严重剥离,脱落比例 35%~65%, 黏附力差;F 级,完全剥离或脱落比例 > 65%, 黏附力非常差。测试结果如表 2 所示。
表 2 黏附力测试结果
样品编号 | 脱落面积占比 | 脱落情况分级 | 黏附力性能描述 |
1-1 | 8 片 > 65% 2 片≈50% | F | 局部大量脱落,黏附力很差 |
1-2 | 7 片≈0 3 片 < 5% | A | 无脱落,黏附力极好 |
2-1 | 铜层脱落:5 片≈35% 5 片≈20% | D | 分层脱落,铜层黏附力较差 |
3-1 | 10 片 < 5% | B | 极少脱落,黏附力良好 |
3-2 | 10 片 < 5% | B | 极少脱落,黏附力良好 |
3-3 | 抽检 10 片 < 5% | B | 极少脱落,黏附力良好 |
3.2 结果与分析
首先,对比样品 1-1 与样品 1-2 黏附力测试结果可知,纯铜膜层与玻璃基底结合能力要弱于纯钛膜层。究其原因,一方面,可能是由于玻璃表面粗糙度低,金属膜层沉积结合困难,另一方面,铜的热膨胀系数为 17×10-6 K-1, 钛的热膨胀系数为 7.6×10-6 K-1, 而玻璃的热膨胀系数为 3×10-6 K-1, 铜与玻璃的热膨胀系数差异更大,在高温镀膜回温后可能导致内应力产生,造成铜膜层脱落更加严重。此外,金属铜的抗腐蚀性能力远弱于金属钛,即使铜膜层的黏附力得到提升,也不建议直接使用铜膜层与玻璃基底进行接触,因为铜层更易被玻璃基底析出的杂质元素侵蚀,导致通信线路失效,因此将钛作为底层膜与玻璃基底结合更能确保线路的可靠性。
其次,分析样品 2-1 黏附力测试结果可知,钛层和铜层之间的结合面黏附力较差,出现铜钛分层脱落的现象,分析其原因,将钛作为结合层置于中间时,铜与钛的结合力优于铜与玻璃基底的结合力,这是由于铜和钛同为金属晶体,界面结合相对容易,但是由于溅射工艺顺序设置为钛和铜分别沉积,导致两层膜的微观分界面明显,属于简单机械结合,再加上铜的延展性较好,易发生拉伸形变,从而导致一定比例的剥离脱落。为提升金属钛和金属铜的界面结合力,调整磁控溅射镀膜工艺,引入样品 3-1 的铜钛合金层作为金属间过渡层,以改善金属界面分层脱落的问题。事实上,样品 3-1 的 "钛 + 钛铜合金 + 铜" 多层复合膜的黏附力测试结果也显示,铜层的脱落情况得到明显改善,膜层与基底、各膜层之间的结合力均良好,未出现大量脱落的现象,这一创新性的膜层工艺设计极大地提高了膜层的黏附力。这是由于同时镀制铜和钛时,在成核过程中,铜钛金属交织生长,且有一定概率形成铜钛固溶合金,界面结合力更加牢固,界面内膜层黏附力得以改善 [11]。另外,考虑到金属钛的抗腐蚀性能力优异,且其氧化物结构比较致密,能够隔绝水分、氧等环境杂质对通信线路的侵蚀,为更好地对表层金属铜层进行防护,本研究又设计了样品 3-2"钛 + 钛铜合金 + 铜 + 铜钛合金 + 钛" 的多层复合膜结构,进一步提升金属线路的综合抗腐蚀能力,黏附力测试结果显示,样品 3-2 展现出良好的黏附力特性。
最后,为进一步提升黏附力,在前述工艺基础上,添加了高压弧靶钛金属作为成核引导工序,根据磁控溅射仪器的工作特点,弧光放电产生的瞬时熔融高温使得金属钛的晶粒以极高的动能在玻璃表面沉积,这进一步巩固了底层膜层与基板的结合力,而且台阶覆盖度能够得到进一步优化,对后续增加功能膜层厚度有极大帮助。黏附力测试结果显示,样品 3-3 黏附力特性良好。特别的,为进一步验证黏附力测试结论,基于上述工艺条件进行了大批量样品测试与试生产,黏附力特性均表现良好。
4 、结语
本研究通过 3D 磁控溅射法设计制备了不同膜层结构的薄膜器件,通过黏附力测试筛选出最佳的膜层结构,为玻璃基 Mini-LED 显示屏幕的侧边线路镀制提供了创新性解决方案,其创新性主要在于多层膜工艺方案、设备开发、设备与工艺步骤相配合的技术要求等均属于首次应用,并且具备批量生产和大规模应用的可能性。但是,该 3D 磁控溅射工艺中涉及的膜层黏附力和通信线路导电性能、抗腐蚀性能等还可做进一步优化,以提升产品的可靠性。另外,此技术可为硅基光电器件和柔性有机 LED 发光器件等的工艺探索提供一定的参考。
【参考文献】
[1] 冯艳丽,黄卫东,邝国烽,等.Mini-LED 背光液晶显示器光晕测量方法 [J]. 信息技术与标准化,2023 (11):20-24.
[2] 郭黎明,朋朝明,陈伟雄,等.MiniLED 电视背光技术浅析与显示标准介绍 [J]. 电子产品世界,2022,29 (5):24-30.
[3] 卢振威,汤晖,林志杭,等。针对 MiniLED 芯片载板的图像清晰度评价函数设计 [J]. 机械工程与自动化,2023 (6):89-90;93.
[4] 胡敏。磁控溅射 Ti/TiN 多层薄膜制备及其性能研究 [D]. 南昌:南昌大学,2010.
[5] 高鹏飞。磁控溅射法制备 ITO 薄膜及其光电性能研究 [D]. 北京:北京交通大学,2014.
[6] 易旭阳,李继文,刘伟,等。基底偏压对磁控溅射沉积 MoSi2 薄膜结构及力学性能的影响 [J]. 河南科技大学学报 (自然科学版),2020,41 (5):1-7;12;3.
[7] 罗蓉蓉,但敏,李鹏远,等。脉冲偏压对磁控溅射 MoS2 固体润滑涂层性能影响 [J]. 真空科学与技术学报,2018,38 (3):208-213.
[8] 范迪,雷浩,宫骏,等。正交电磁场离子源及其在 PVD 法制备硬质涂层中的应用 [J]. 真空,2014,51 (4):48-52.
[9] 霍秋红,张翔,王昆仑,等。脉冲偏压占空比对磁控溅射制备 ITO 薄膜光电性能的影响 [J]. 科技智囊,2020 (8):50-53.
[10] 薛莹洁,陈海峰。磁控溅射镀膜中钛靶冷却系统的仿真与优化 [J]. 钛工业进展,2017,34 (2):38-44.
[11] 侯丽媛。双靶共沉积镀制复合膜的成分均匀性研究 [D]. 沈阳:东北大学,2010.与液压,2022,50 (20):70-77.
相关链接