引言
钛合金作为一种具有比强度、比刚度高,耐热性好的金属材料,并且其抗疲劳、抗腐蚀能力出众,工作温度范围宽,在航空航天、医疗、船舶、军工等领域得到广泛关注与应用[1,2]。然而,从加工制造角度来看,钛合金具有导热系数小、比热小、弹性模量低、化学活性很强等特点,因此,其加工困难,从而使其成为国内外学者研究的热点。解决钛合金加工中的上述问题,关键在于研究钛合金的切削机理以及切削参数的合理选择[3]。铣削力和材料去除率是材料铣削加工过程中重要的物理量,对加工零件的加工效率、加工质量及加工能耗产生很大的影响。于是,以最小铣削力、最大材料去除率为目标,进行参数的合理选择。然而,材料去除率与铣削力互相矛盾,一方最优将会导致另一方做出妥协,为解决这一问题,需进行多目标优化,以获得目标函数的最佳适应值[4]。目前,国内外众多学者对钛合金材料进行了一系列研究。Zhu等[5]针对小型CBN磨头磨削钛合金建立了磨削力数值预测模型,以便对工艺参数进行优化。Wu等[6]以航空发动机TC4钛合金整体叶盘叶片为研究对象,研究了整体叶盘叶片表面波纹度的形成机理和优化方法。Shen等[7]对钛合金表面变质层进行铣削研究,分析了表面变质层的形成机理,得出了各参数对表面粗糙度和残余应力的影响规律,并建立了预测模型。根据TC4高速切削中铣削力的方差分析和回归模型,Ngoc等[8]指出进给速度和轴向切深是影响铣削力的最重要因素。基于Box-Behnken设计实验,Karkalos等[9]指出进给速度对表面粗糙度的影响起着主导作用。近年来,切削参数优化受到了广泛的关注并被大量研究。易茜等[10]利用多目标水循环算法实现加工变形和加工效率的调节最优。Monir等[11]基于回归和遗传算法对126BHN低合金钢进行切削参数优化,得到最佳表面粗糙度。Ven‐katesh等[12]利用响应面法设计实验建立目标函数,采用遗传算法、模拟退火算法和神经网络算法进行优化,对预测值进行分析比较,得到最优值。
Ojordje等[13]基于遗传算法对AISI1040钢进行干式车削,以最小化表面磨损、最小化表面粗糙度和最大化材料去除率为目标,进行多目标优化,通过改变遗传算法的参数来获得目标函数的最优值。本文以铣削参数(铣削速度vc、每齿进给量fz、铣削深度ap和铣削宽度ae)为变量,选用L16(45)正交表,设计四因素四水平正交实验。基于极差分析,找出铣削参数对铣削力和材料去除率的影响规律。以最小铣削力、最大材料去除率为目标,分别以灰色关联分析法(GRA)和粒子群优化(PSO)算法进行参数优化,对比分析得到最优值。在PSO优化前,基于回归分析建立铣削力与铣削参数的二阶多项式数学模型,为PSO优化模型做准备。最后,对优化结果进行实验验证与比较,选择最佳优化方法。
1、实验条件和方法
1.1 实验条件
实验以钛合金Ti-6Al-4V(TC4)薄壁件为研究对象,其中薄壁件大小为50mm×50mm×5mm,钛合金的化学成分如表1所示。通过专用夹具,把工件的一端固定在工作台,刀具按照预先设定的参数在工件的另一端运行加工。
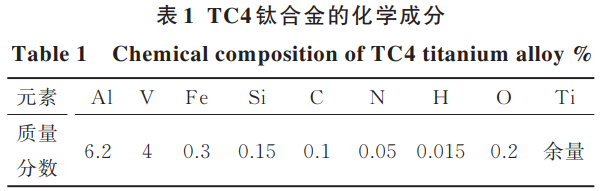
铣削实验现场如图1所示。实验设备采用大连三垒SVW80C-3D增减材复合五轴加工中心,加工刀具选择YG8-4B-R3.0四刃硬质合金球头铣刀,加工过程产生的铣削力由Kistler三向铣削测力仪进行采集。
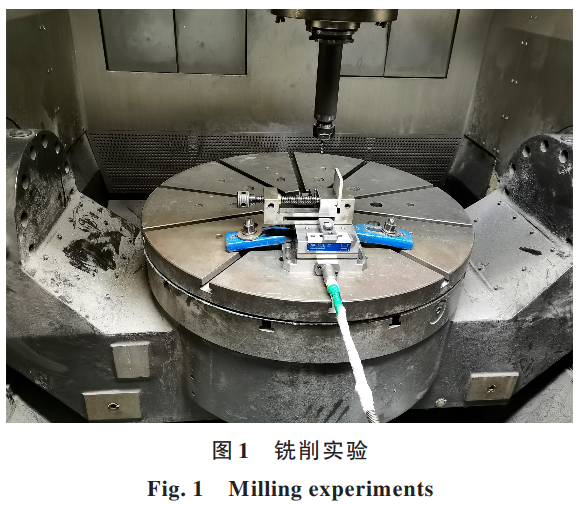
1.2 实验方法
为探究铣削加工参数对铣削力以及材料去除率的影响规律并寻求最佳参数组合,基于正交实验方法设计实验,加工方式采用侧铣(顺铣)、干润滑。本实验选用L16(45)正交表,设计四因素四水平正交实验,铣削加工参数分别为:铣削速度vc(mmin)、每齿进给量fz(mmz)、铣削深度ap(mm)和铣削宽度ae(mm)。
表2为实验因素水平。
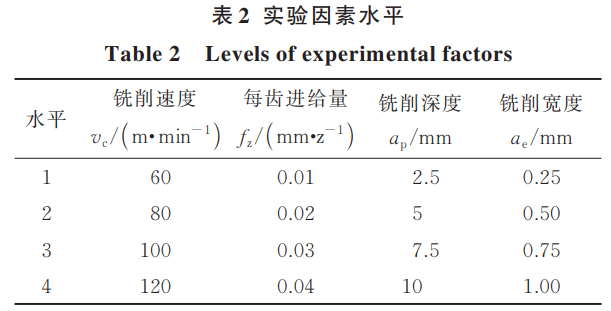
2、实验结果及讨论
2.1 数据处理
为了得到科学观测值,在测力仪采集的数据中,取相对平缓稳定位置数据的均值分别作为X、Y和Z方向的铣削力数值。根据式(1)和(2)分别求出合力F和材料去除率MRR。得到最终实验结果,如表3所示。
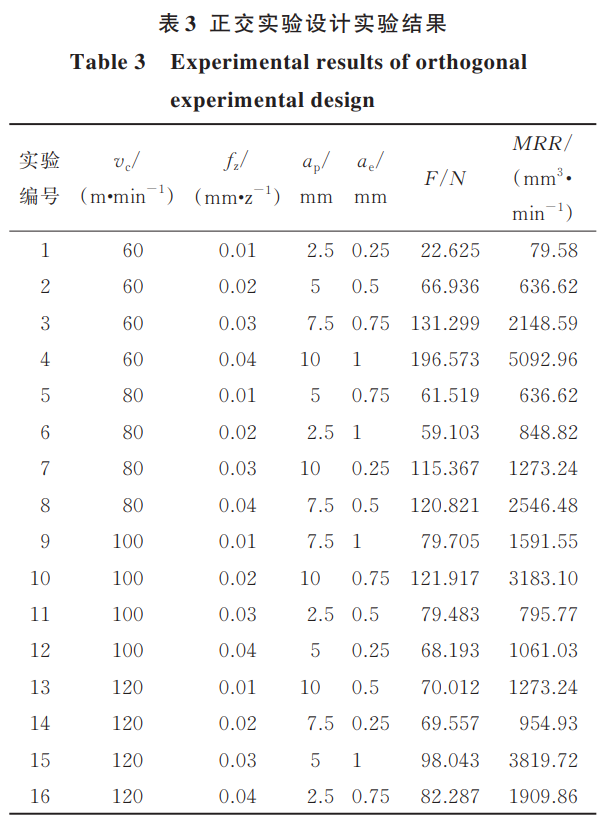
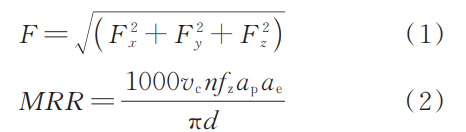
式中:Fx为x方向的铣削分力;Fy为y方向的铣削分力;Fz为z方向的铣削分力;d为铣刀直径,本实验d取6mm;n为铣刀刃数,本实验n取4。
2.2 铣削合力F
采用极差分析法处理数据,来判断铣削参数对铣削合力F的影响程度。表4为合力F的极差分析结果,图2为各铣削参数对F的影响。根据结果分析可知,铣削速度vc对铣削合力F的影响呈负相关,每齿进给量fz、铣削深度ap和铣削宽度ae对铣削合力F的影响呈正相关,影响程度大小依次为铣削深度ap、每齿进给量fz、铣削宽度ae、铣削速度vc。
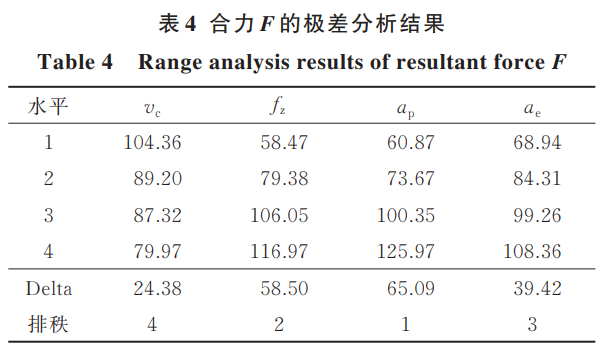
2.3 材料去除率MRR
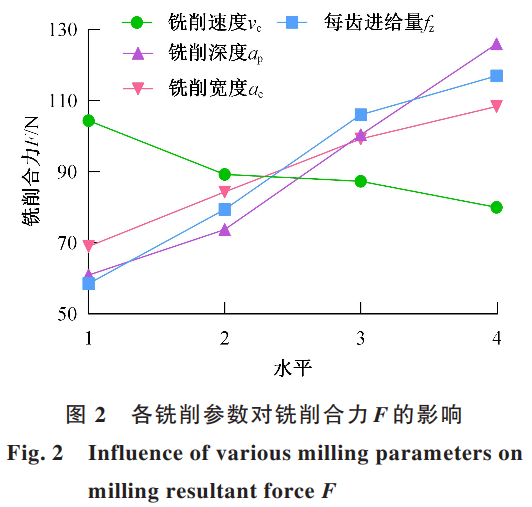
同样采用极差分析法进行数据处理,来判断铣削参数对材料去除率MRR的影响程度。表5为材料去除率MRR的极差分析结果,图3为各铣削参数对材料去除率MRR的影响。
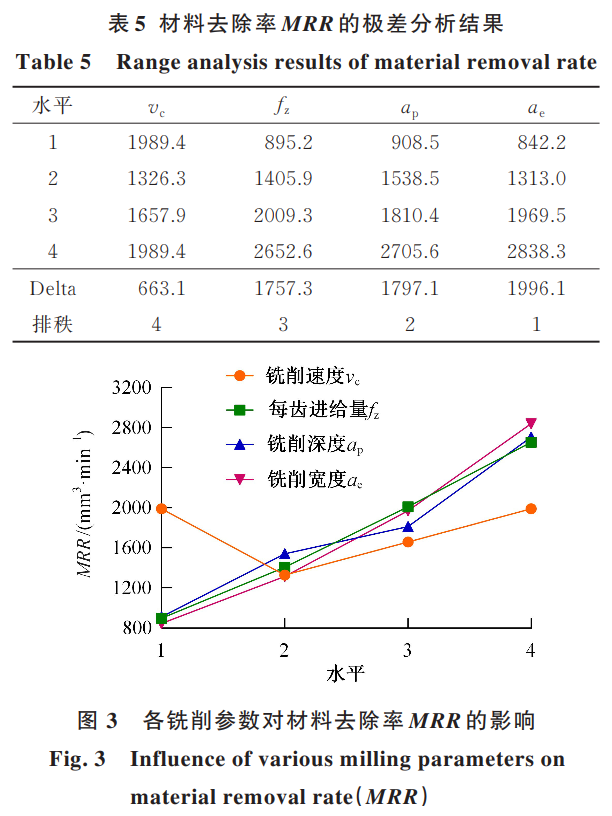
根据结果分析可知,材料去除率MRR随着每齿进给量fz、铣削深度ap和铣削宽度ae的增大而增大;对于铣削速度vc,材料去除率MRR先随其增大而减小,后随其增大而增大。铣削参数对材料去除率MRR的影响程度大小依次为铣削宽度ae、铣削深度ap、每齿进给量fz、铣削速度vc。
3、铣削参数优化
3.1 基于灰色关联分析的参数优化
3.1.1 灰色关联分析(GRA) 本文以合力F和材料去除率MRR为响应量进行优化研究,属于多目标优化问题。为了解决多目标优化的复杂性问题,利用灰色关联分析(GRA)的方法,将多目标优化转化为单目标优化[14-17]。如图4所示,灰色关联分析的步骤如下:步骤1:计算信噪比信噪比(S/N)是获得最佳因子水平最合适的方法。假设ηij为第i次实验第j个响应的信噪比;
yijk为第i次实验第j个响应在第k次重复实验下的实验数值;n为重复实验的次数,则信噪比的计算公式如下所示:

式(3)适用于“越小越好”的响应,而式(4)适用于“越大越好”的响应。对于铣削力而言,铣削力越小越好,故选用“越小越好”响应,即式(3);另一方面,针对材料去除率,材料去除率越高,性能越好,于是选择式(4)。步骤2:数据归一化对每个响应的实验数据进行归一化处理,使其介于0和1之间,以降低可变性,此过程也称为灰色关联生成。
式中:
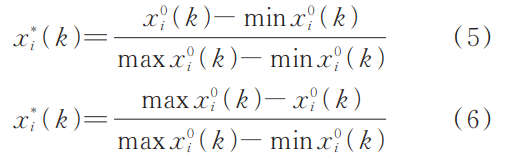
x*i(k)为归一化数值,x0i(k)为原始的实验数据;maxx0i(k)为第i个数列中所有实验的最高水平;minx0i(k)为第i个数列中所有实验的最低水平。对于铣削力选用式(6),即“越小越好”响应;对于材料去除率选用式(5),即“越大越好”响应。步骤3:计算灰色关联系数(GRC)将数据归一化后,计算灰色关联系数:
式中:
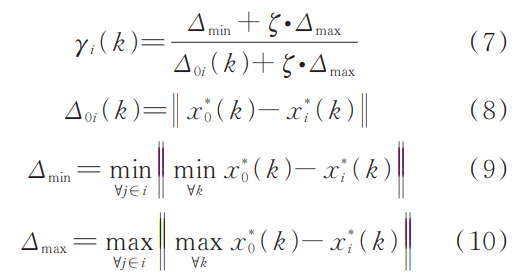
γi(k)为灰色关联系数;ζ为分辨系数,其作用在于提高关联系数之间的差异显著性,ζ∈[0,1],通常ζ取0.5;Δ0i(k)为参考序列(x*0(k)=1)和比较序列(x*
i(k))的差值,信噪比、归一化、GRC的数据处理结果如表6所示。步骤4:计算加权灰色关联度(WGRG) 通过取每个性能特征的灰色关联系数的平均值来计算灰色关联度(GRG),数学表达式如下:

式中:γi为第i次实验的灰色关联度;n为响应量的数量。在实际的工程应用中,每个响应的重要性是不同的。为了研究每个响应的影响,需对其分配权重因子。则加权灰色关联度(WGRG)数学表达式如式(12)所示:
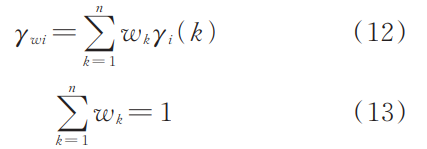
式中:γwi为加权灰色关联度;wk为每个响应量的权重因子。
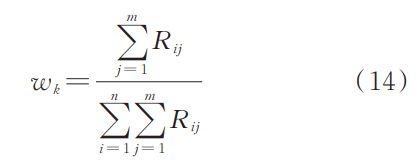
式中:Rij为灰色关联系数极差;n、m分别为响应量数目、铣削参数数目。在本研究中,根据实验设计,n、m分别取2、4。
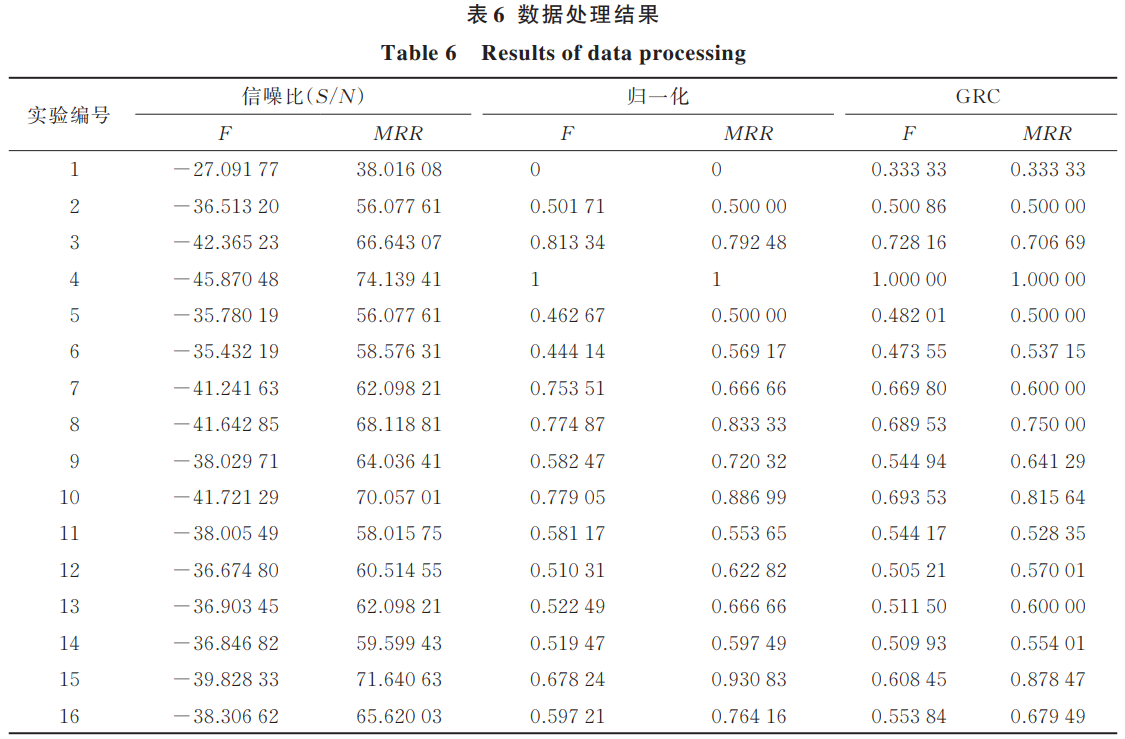
表7为各个水平灰色关联系数的均值。根据所得到的权重系数,可得加权灰色关联度公式如下:

式中:WGRG为加权灰色关联度;GRCF和GRCMRR分别为铣削力和材料去除率的灰色关联系数。响应的加权灰色关联度值如表8所示,根据加权灰色关联度可知,第4组铣削参数最好。
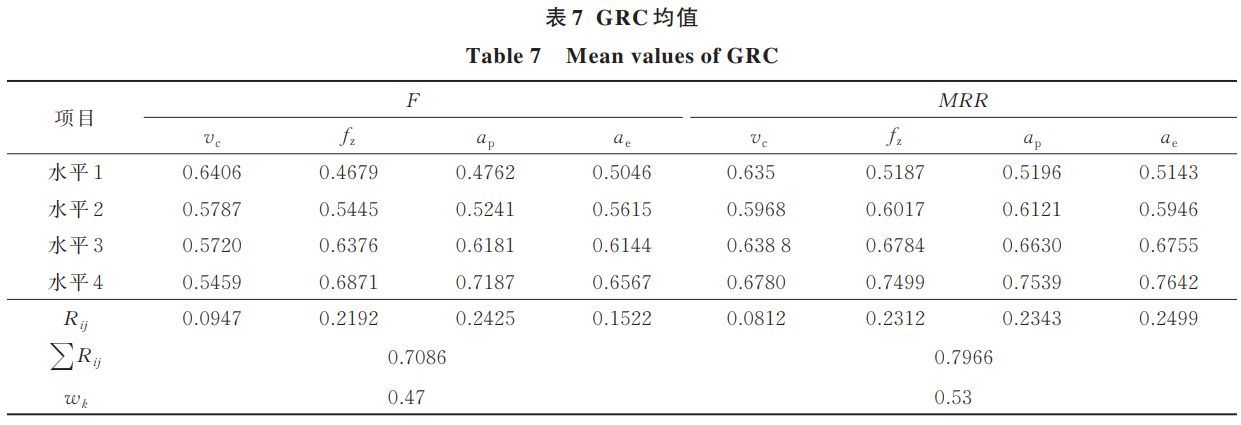
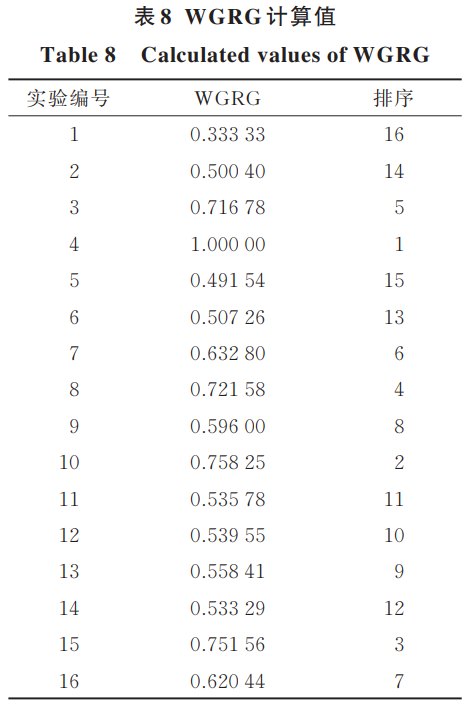
3.1.2 基于GRA参数优化
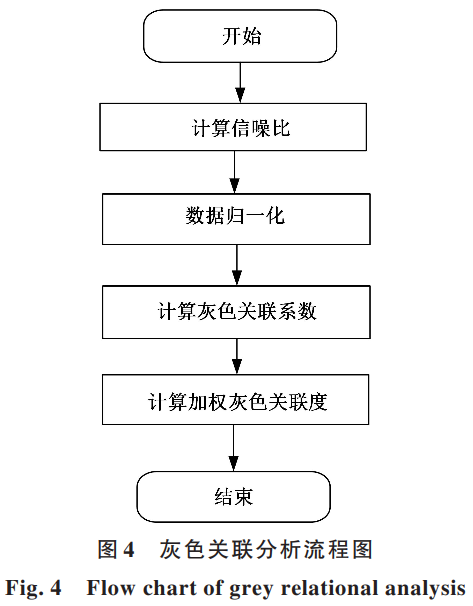
通过上述4个步骤,将多目标问题转化为单目标问题。通过极差法衡量加权灰色关联度值,确定最佳切削参数水平,如表9、图5所示。
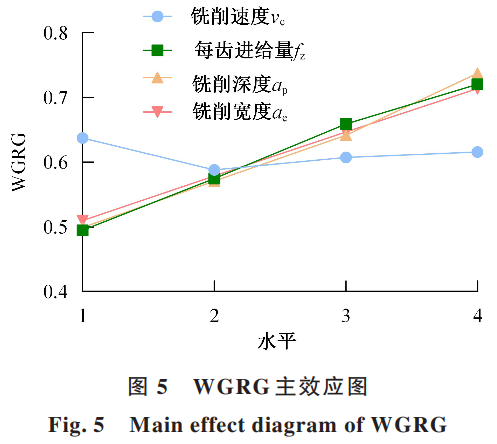
从表9、图5可知,对铣削力和材料去除率的组合影响大小依次是铣削深度ap、每齿进给量fz、铣削宽度ae、铣削速度vc。WGRG随着每齿进给量fz、铣削深度ap和铣削宽度ae的增大而增大;对于铣削速度vc,先随其增大而减小,后随其增大而增大。于是根据正交实验和灰色关联度,可得到该实验的最优解,最优解结果为A1B4C4D4,即vc=60mmin、fz=0.04mmz、ap=10mm、ae=1mm,恰好是第4组实验,其WGRG为1。
3.2 基于粒子群优化(PSO)算法的参数优化
3.2.1 建立铣削力预测模型 为研究智能算法参数优化问题,首先需建立铣削力与铣削参数之间的关系的数学模型。采用逐步回归方法建立二阶多项式数学模型[6],数学表达式如式(16)所示:

式中:ŷ为铣削力的预测值;β为数学模型的系数;第二项为线性效应;第三项表示交互性效应;最后一项表示二次效应。利用Python对实验数据进行回归分析,得到铣削力与铣削参数之间的关系的数学模型,如式(17)所示:
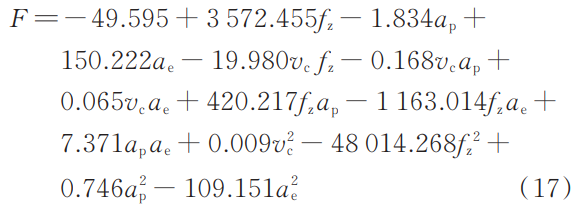
建模完成后,运用IBMSPSSStatistics软件对其进行F检验。铣削力的预测值与实验值对比如图6所示,从图6中可以看出,铣削力的预测值与实验值非常接近,并且平均误差为3.75%,最大误差为10.2%,表明预测值与实验值之间无显著差异。铣削力F预测模型的方差分析(ANO‐VA)结果如表10所示,取α=0.05,查表可知,临界值Fα(13,2)=19.419,表10中F远大于临界值19.419,说明回归方程显著。图7为回归标准化残差的正态P-P图,从图可以看出,实验点围绕45°直线均匀随机分布,无异常点出现,说明预测模型良好。因此,该回归数学模型可以作为铣削力的预测模型。
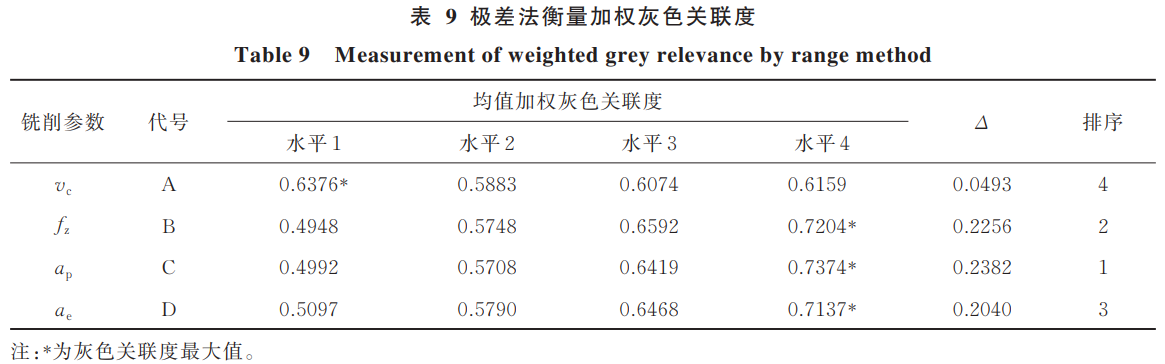
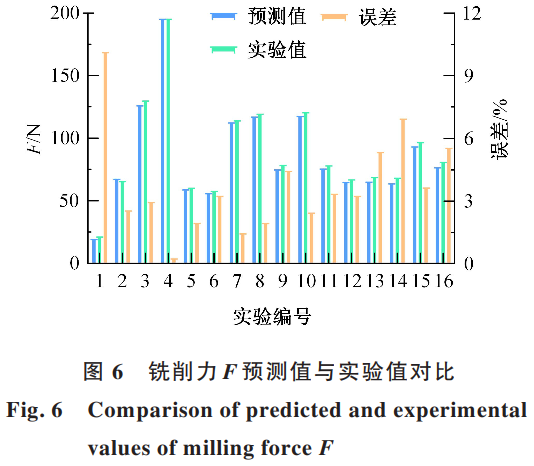
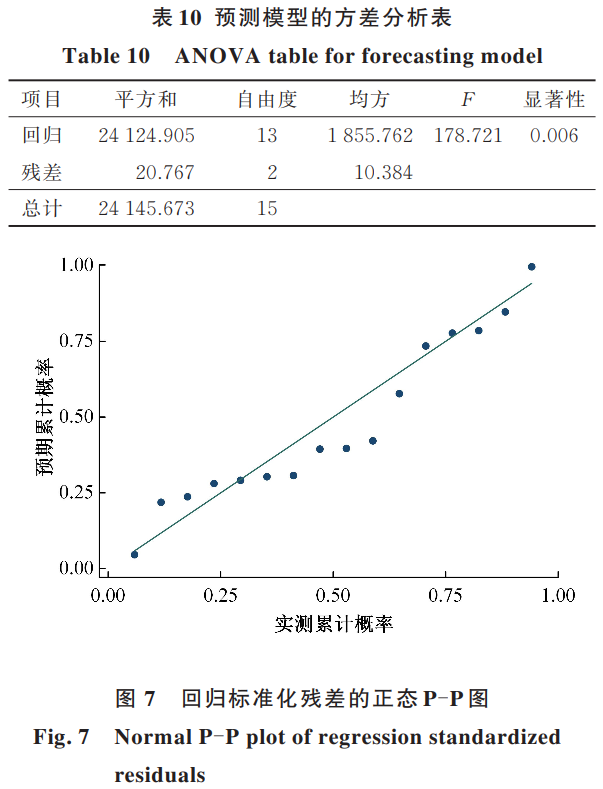
3.2.2 基于PSO参数优化
根据前文理论分析,要使优化目标达到最优,即铣削力最小和材料去除率最高,需建立一个优化模型,如式(18)所示:
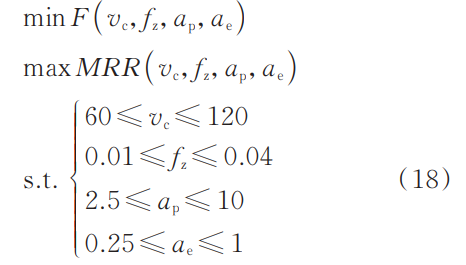
利用线性加权方法,将多目标优化转为单目标优化,使铣削力及材料去除率均可达到相对最优的参数组合。设ω1、ω2为加权因子,且ω1+ω2=1,本文ω1、ω2分别取0.47和0.53,优化模型如式(19)所示:
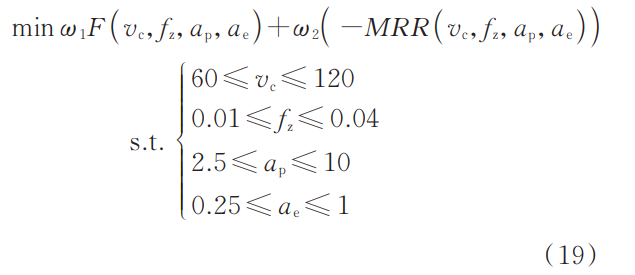
通过Python编写PSO算法程序(见图8)对优化模型进行优化,得到最优解gBest=-5331.2516,且此时最优参数组合为vc=120mmin、fz=0.04mmz、ap=10mm、ae=1mm。
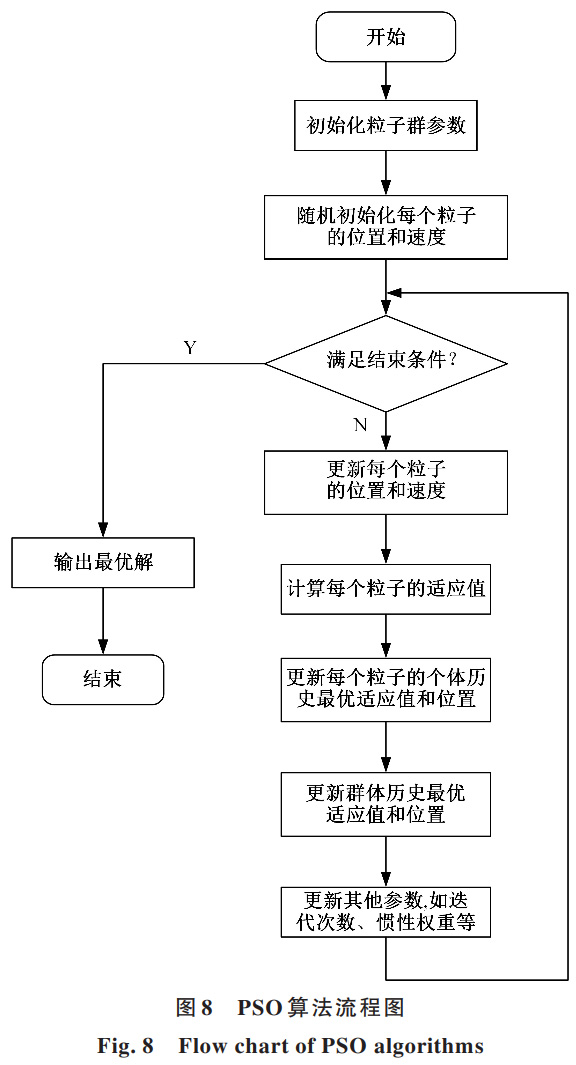
4、实验验证
为对铣削力预测模型准确性及两种参数优化方法有效性进行评估,需展开实验验证。基于GRA进行优化时,得到的最优参数组合为vc=60mmin、fz=0.04mmz、ap=10mm、ae=1mm,经实验验证可知,铣削力F实验值为196.573N,材料去除率MRR为5092.96mm3min,而此时的铣削力F预测值为196.636N,预测值与实验值之间的相对误差为0.3%。当采用PSO进行参数优化时,最优参数组合为vc=120mmin、fz=0.04mmz、ap=10mm、ae=1mm,此时铣削力实验值F=147.121N,材料去除率MRR=10185.92mm3min,铣削力的预测值F=148.984N,相对误差为1.3%。验证实验的预测值与实验值之间的相对误差均低于2%,说明预测模型比较准确与实用。
在实验验证的基础上,可以看出,基于PSO进行优化得到的铣削力更小,材料去除率更大,因此,与GRA优化相比,PSO优化效果更好。
5、结论
(1)采用正交实验方法设计钛合金TC4薄壁件铣削实验,通过极差分析得知铣削速度vc对铣削合力F的影响呈负相关,每齿进给量fz、铣削深度ap和铣削宽度ae对F的影响均呈正相关,且铣削参数对F影响的显著性由大到小的顺序为:铣削深度ap>每齿进给量fz>铣削宽度ae>铣削速度vc。
(2)通过极差分析,得出每齿进给量fz、铣削深度ap和铣削宽度ae对材料去除率MRR的影响均呈正相关;对于铣削速度vc,材料去除率MRR先随其增大而减小,后随其增大而增大。铣削参数对材料去除率MRR影响的显著性由大到小的顺序为铣削宽度ae>铣削深度ap>每齿进给量fz>铣削速度vc。
(3)利用Python对实验数据进行回归分析,得到铣削力与铣削参数之间的关系的数学模型,ANOVA分析结果表明,F=178.721远大于临界值Fα(13,2)=19.419,并且平均误差为3.75%,最大误差低于11%,说明铣削力预测模型显著。
(4)采用灰色关联分析法与粒子群优化算法分别进行铣削参数优化,相比之下,粒子群优化算法得到的参数组合vc=120mmin、fz=0.04mmz、ap=10mm、ae=1mm,其铣削力更小、材料去除率更大,因此,粒子群算法优化效果更好。
参考文献:
[1] Tan Liang, Yao Chang-feng, Ren Jun-xue, et al. Ef‐ fect of cutter path orientations on cutting forces, tool wear, and surface integrity when ball end milling TC17 [J]. The International Journal of Advanced Manufactur‐ ing Technology, 2017, 88(9-12): 2589-2602.
[2] 张翔宇, 路正惠, 彭振龙, 等 . 钛合金的高质高效超声 振动切削加工[J]. 机械工程学报, 2021, 57(5): 133-147. Zhang Xiang-yu, Lu Zheng-hui, Peng Zhen-long, et al. High quality and efficient ultrasonic vibration cut‐ ting of titanium alloys[J]. Journal of Mechanical Engi‐ neering, 2021, 57(5): 133-147.
[3] Li J, Yang X, Ren C, et al. Multiobjective optimiza‐ tion of cutting parameters in Ti-6Al-4V milling pro‐ cess using nondominated sorting genetic algorithm-II [J]. The International Journal of Advanced Manufac‐ turing Technology, 2015, 76: 941-953.
[4] Serra R, Chibane H, Duchosal A. Multi-objective optimization of cutting parameters for turning AISI 52100 hardened steel[J]. International Journal of Ad‐ vanced Manufacturing Technology, 2018, 99(5-8): 2025-2034.
[5] Zhu Li-da, Yang Zhi-chao, Li Zhao-bin. Investiga‐ tion of mechanics and machinability of titanium alloy thin-walled parts by CBN grinding head[J]. The In‐ ternational Journal of Advanced Manufacturing Tech‐ nology, 2019, 100(9-12): 2537-2555.
[6] Wu D, Wang H, Zhang K, et al. Research on forma‐ tion mechanism and optimization method of surface waviness of TC4 blisk blade[J]. Journal of Manufac‐ turing Processes, 2019, 39: 305-326.
[7] Shen X, Zhang D, Yao C, et al. Formation mecha‐ nism of surface metamorphic layer and influence rule on milling TC17 titanium alloy[J]. The International Journal of Advanced Manufacturing Technology, 2021, 112(7,8): 2259-2276.
[8] Ngoc Chien Vu, Shyh Chour Huang, Huu That Nguyen. Multi-objective optimization of surface rough‐ ness and cutting forces in hard milling using taguchi and response surface methodology[J]. Key Engineer‐ ing Materials, 2018, 773: 220-224.
[9] Karkalos N E, Galanis N I, Markopoulos A P. Sur‐ face roughness prediction for the milling of Ti6Al4V ELI alloy with the use of statistical and soft computing techniques[J]. Measurement, 2016, 90: 25-35.
[10] 易茜, 李聪波, 潘建, 等 . 薄板类零件加工精度可靠 性 分 析 及 工 艺 参 数 优 化[J]. 中 国 机 械 工 程, 2022, 33(11): 1269-1277.
Yi Qian, Li Cong-bo, Pan Jian, et al. Reliability analysis of machining accuracy and processing parame‐ ter optimization for thin-plate parts[J]. China Mechan‐ ical Engineering, 2022, 33(11): 1269-1277.
[11] Monir K O, Samy E A A. Optimization of cutting conditions using regression and genetic algorithm in end milling[J]. International Journal of Engineering Research in Africa, 2016, 20: 12-18.
[12] Venkatesh M, Suresh K R N. Optimization of mill‐ ing operations using artificial neural networks (ANN) and simulated annealing algorithm (SAA) [J]. Materi‐ als Today: Proceedings, 2018, 5(2): 4971-4985.
[13] Djordje V, Katica S, Zeljko K, et al. Multi-objec‐ tive optimization of steel AISI 1040 dry turning using genetic algorithm[J]. Neural Computing & Applica‐ tions, 2021, 33(19): 12445-12475.
[14] Eskandari B, Davoodi B, Ghorbani H. Multi-objec‐ tive optimization of parameters in turning of N-155 iron-nickel-base superalloy using gray relational anal‐ ysis[J]. Journal of the Brazilian Society of Mechanical Sciences and Engineering, 2018, 40(4): No. 233.
[15] Maiyar L M, Ramanujam R, Venkatesan K, et al. Optimization of machining parameters for end milling of inconel 718 super alloy using taguchi based grey re‐ lational analysis[J]. Procedia Engineering, 2013, 64: 1276-1282. [16] Ic Y T, Yildirim S. MOORA-based taguchi optimis‐ ation for improving product or process quality[J]. In‐ ternational Journal of Production Research, 2013, 51 (11): 3321-3341.
[17] 魏子茹, 卢延辉, 王鹏宇, 等 . 基于 CRITIC 法的灰 色关联理论在无人驾驶车辆测试评价中的应用[J].机械工程学报, 2021, 57(12): 99-108.
Wei Zi-ru, Lu Yan-hui, Wang Peng-yu, et al. Ap‐ plication of grey correlation theory based on CRITIC method in autonomous vehicles test and evaluation [J]. Journal of Mechanical Engineering, 2021, 57(12): 99-108.
[18] 曾念寅, 宋丹丹, 李寒, 等 . 改进鲸鱼优化算法及涡轮 盘结构优化[J]. 机械工程学报, 2021, 57(20): 254-265.
Zeng Nian-yin, Song Dan-dan, Li Han, et al. Im‐ proved whale optimization algorithm and turbine disk structure optimization[J]. Journal of Mechanical Engi‐ neering, 2021, 57(20): 254-265.
[19] 易茜, 柳淳, 李聪波, 等 . 基于小样本数据驱动的滚 齿 工 艺 参 数 低 碳 优 化 决 策 方 法[J]. 中 国 机 械 工 程, 2022, 33(13): 1604-1612.
Yi Qian, Liu Chun, Li Cong-bo, et al. A low carbon optimization decision method for gear hobbing process parameters driven by small sample data[J]. China Me‐ chanical Engineering, 2022, 33(13): 1604-1612.
[20] 卫星驰, 赵嫚, 杨青平, 等 . 考虑工件变形的五轴侧 铣 薄 壁 件 铣 削 力 建 模 [J]. 机 械 工 程 学 报 , 2022, 58(7): 317-324. Wei Xing-chi, Zhao Man, Yang Qing-ping, et al. Milling force modeling of thin-walled parts with 5-Axis flank milling considering workpiece deformation [J]. Journal of Mechanical Engineering, 2022, 58(7): 317-324.
[21] 于繁华, 刘仁云, 张义民, 等 . 机械零部件动态可靠 性稳健优化设计的群智能算法[J]. 吉林大学学报:工 学版, 2017, 47(6): 1903-1908. Yu Fan-hua, Liu Ren-yun, Zhang Yi-min, et al. Swarm intelligence algorithm of dynamic reliabilitybased robust optimization design of mechanic compo‐ nents[J]. Journal of Jilin University(Engineering and Technology Edition), 2017, 47(6): 1903-1908.
[22] 张禹, 鹿浩, 吕董, 等 . 基于 IMOFA 的航空发动机 管 路 多 目 标 优 化 布 局[J]. 东 北 大 学 学 报:自 然 科 学 版, 2022, 43(8): 1120-1126. Zhang Yu, Lu Hao, Lyu Dong, et al. Multi-objec‐ tive optimization layout of aero-engine pipe routing based on IMOFA[J]. Journal of Northeastern Univer‐ sity(Natural Science), 2022, 43(8): 1120-1126.
[23] 陈 昭 明,邹 劲 松,王 伟,等 . 改 进 粒 子 群 神 经 网 络 融 合有限元分析的铸锻双控动态成型多目标优化[J].吉林大学学报:工学版, 2022, 52(7): 1524-1533.
Chen Zhao-ming, Zou Jin-song, Wang Wei, et al. Multi-objective optimization of casting-forging dy‐ namic forming based on improved particle swarm neu‐ ral network and finite element analysis[J]. Journal of Jilin University(Engineering and Technology Edi‐ tion), 2022, 52(7): 1524-1533.
相关链接