前言
近年来,全球电子信息产业的高速发展,使薄膜科学的应用日益广泛。而溅射靶材作为镀膜产业的基本耗材
,其制备技术也得到了长足发展。溅射薄膜由于其致密度高,附着性好,被广泛应用于装饰、工模具、玻璃
、电子器件、半导体、磁记录、平面显示、太阳能电池等众多领域。随着上述领域的快速发展,对靶材的需
求量急剧增加,同时对靶材的高质量、大型化及利用率方面也提出了更高的要求。
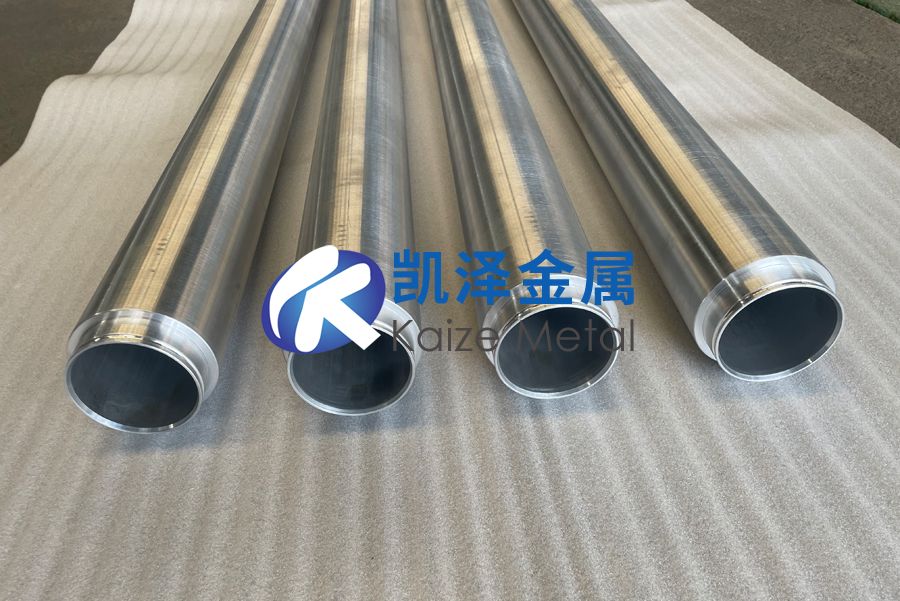
目前采用传统方法制备靶材的局限性越来越大,对于很多大尺寸的高熔点、脆性材料几乎无法制备。例如长度达3~4m,直径100mm以上的钨、钼、铬、硅及其合金靶管状靶材或尺寸达到几平米的平面靶材,传统方法
成本很高而且难度大几乎无法完成。因此,需要寻求新的大尺寸靶材制备方法来突破溅射靶材制备技术的瓶
颈。
等离子喷涂技术由于喷涂温度高,几乎可以熔化所有金属及陶瓷材料,并且涂层厚度可控,可实现近净成形,已逐渐由表面涂层制备扩展到了材料成形领域,成为一种新型的溅射靶材制备方法。
1、溅射靶材的主要制备方法
溅射靶材按其材质可分为纯金属靶、合金靶、陶瓷化合物靶(包括氧化物、硅化物、碳化物、硫化物等)、复
合靶。按形状可分为平面靶和管状旋转靶,平面靶又可分为矩形板和圆形靶。目前,虽然溅射靶材种类繁多
,但其基本的制备工艺主要有可分为粉末冶金法和熔炼铸造法两大类。
粉末冶金法包括粉末压制烧结法、粉末热等静压法等。粉末冶金法是将纯金属粉末按比例混合均匀,经过压
制成形,然后在高温下烧结,经压力加工、热处理后最终得到靶材。适合于难熔金属如钨、钼靶材及陶瓷靶
材等。采用粉末冶金法制备的靶材具有成分均匀及晶粒均匀细小、成品率高的优点,但制备过程采用粉末混合、压制和烧结工艺,容易在制备过程这带人杂质元素,烧结过程杂质排除效果较差,造成靶材纯度相对较
低,并且烧结靶材的密度也较熔炼靶低。
熔炼铸造法的基本工艺是将一定比例的合金原料熔炼后浇注到模具中形成铸锭,然后通过锻造、挤压或拉拔
的成形工艺进行加工,最后经过热处理、机加工等工序制备得到溅射靶材。常用的熔炼方法有真空感应熔炼
,真空电弧熔炼和真空电子束熔炼等。
与粉末冶金法相比,熔炼铸造法得到的靶材纯度高,密度高,但其工艺较为复杂,对设备要求高,成本也随之升高,并且靶材晶粒粗大。若各组分之间熔点和密度相差较大,则难以获得成分均匀的合金靶材。
以上两类方法在溅射靶材的制备方面虽然被广泛采用,但其共同的问题就是难以制备大尺寸(平面靶及管状
靶)的溅射靶材,尤其对一些高熔点脆性材料更是如此。而靶材的大尺寸及高利用率(管状靶材利用率可达50%~70%])已经成为了未来镀膜领域的新趋势。因此,开发新型的大尺寸溅射靶材制备方法已经成为目前
靶材制备领域亟待解决的问题。
2、等离子喷涂技术
2.1 等离子喷涂技术简介
等离子喷涂是利用等离子火焰加热融化喷涂粉末使其形成涂层,一般等离子喷涂使用Ar或N2气,再加入5%~
10%的H2气,气体进入电极区的弧状区被加热电离形成等离子体,其中心温度一般可达15000℃以上,将金属
或非金属材料粉末送入等离子射流中,将其加热到半熔化、熔化或气化状态,并在冲击力的作用下将其沉积到基体上,从而获得具有各种功能的涂层。等离子喷涂工艺首先出现在航空航天及核工业领域,并日趋发展
成熟,因其涂层具备高性能,并且厚度、质量和再现性可控,所以等离子喷涂工艺已迅速扩展到其他行业,
如溅射靶材的制备领域等。
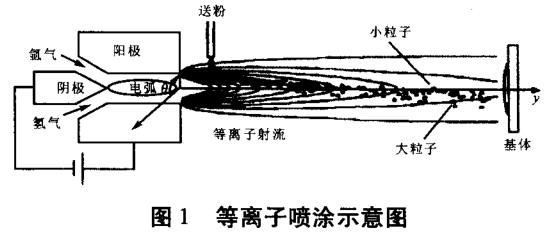
2.2 等离子喷涂技术的特点
等离子喷涂具有如下特点:(1)等离子喷涂的焰流温度高,热量集中,几乎能融化所有高熔点的粉末材料,
可以根据工件表面性能要求制备出各种性能的涂层;(2)等离子焰流喷射速度高,能使粉末获得较大的动能
和较高的温度,涂层与基体结合强度高;(3)喷涂层平整光滑,厚度精确可控,直接进行精加工即可获得产
品,是一种近净成形制备方法,节省材料,特别适合贵重金属涂层及靶材的制备;(4)等离子喷涂通过采用
真空密闭,通人还原性气体、惰性气体保护等方法,可获得氧含量低、杂质少的涂层;(5)采用高能等离子
喷涂设备,粉末沉积率高,沉积速度快,可获得较厚的涂层,这是制备溅射靶材的重要保证。
2.3 等离子喷涂设备
等离子喷涂设备主要由等离子喷涂电源、等离子喷枪、控制柜、送粉器装置等组成。
等离子喷涂电源是等离子射流能量提供装置,其工作电流和电压是影响涂层质量的重要参数。喷枪是集所有
喷涂所用的电、气、粉、水于一体的核心装置,为喷涂材料的融化、细化及其喷涂能力转换提供空间,喷枪
设计的好坏直接影响到喷涂涂层的质量及喷涂效率。这两者是等离子喷涂系统中最为关键的部件。
目前国内外先进的等离子喷涂设备向轴线送粉技术、多功能集成技术、实时控制技术、喷涂功率两极化(小
功率或大功率)的方向发展。加拿大的Mettech公司开发出AxialIII三阴极送粉等离子喷涂系统,是目前国际
上成功商业应用的轴向送粉等离子喷涂设备。与传统的枪外送粉等离子喷涂设备相比,它的沉积率高、送粉
速率高、孔隙率低、获得的涂层硬度高,且对粉末粒度分布要求不高。SulzerMetco公司的Muhicoat等离子
喷涂系统,将计算机和可编程逻辑控制器PLC稳固性结合起来。Multi.coat等离子喷涂系统可进行大气等离
子喷涂、真空等离子喷涂和超音速火焰喷涂。喷涂的涂层质量高、重现性好,能自动记录喷涂参数,自动报
警和处理事故,是目前集成性能较好的等离子喷涂设备。PRAXAIR-TAFA公司开发的5500~2000等离子喷涂系
统是实时控制技术的代表,使喷涂系统的闭环控制提高到新的水平。其开发的大功率等离子喷涂系统PlaJet
,喷枪功率可达到200kW。
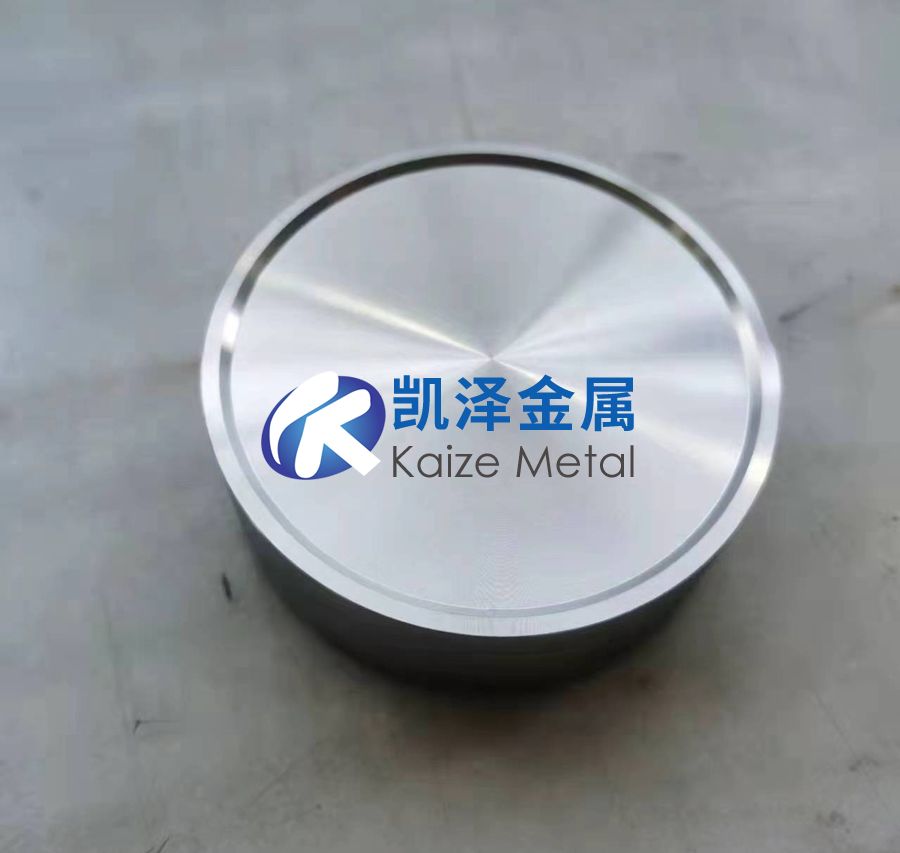
在国内,北京航空制造工程研究所研制的ASP一2000型等离子喷涂设备采用了许多新技术,总体性能达到国
外90年代水平。航天科技集团703所研制的HT一200型超音速等离子喷涂设备额定使用功率达到200kW,填补
了我国大功率等离子喷涂设备的空白。
2.4 影响喷涂效果的因素
2.4.1 电弧功率
电弧功率过高会使等离子体电离度增加,火焰温度升高,可能会使喷涂材料气化而引起涂层成分改变。功率
过低会引起粉末颗粒加热不足,涂层粘接强度低,硬度和沉积效率低。
2.4.2 供粉
供粉速度应与输入功率相适应。一般来说,粉末送到焰心才能使其获得优良的加热和最高的速度。
2.4.3 喷涂距离和喷涂角
喷涂材料及其涂层的特征对喷涂距离很敏感。喷涂距离过大,粉末的温度和速度下降,结合力、喷涂效率都
会明显下降;过小会使基体表面温度过高,影响涂层结合。在基体温度允许的情况下,喷涂距离适当小些为
好。喷射角,一般应大于45度,喷涂角过小会导致“阴影效应”,涂层中会出现空穴,造成涂层疏松。
2.4.4 基体的温度控制
在喷涂前把工件预热到喷涂所需要的温度,然后对工件采取喷气等冷却措施,使其保持恒定温度。
2.4.5 喷涂压力
在金属材料的喷涂过程中一般采取低压等离子喷涂(也叫真空等离子喷涂),在压力为4~40kPa的可控气氛腔
室内喷涂。由于工作气体离子化后,是在低压气氛中边膨胀边喷出,喷流射速可达到超音速,适合对氧化敏
感的金属材料的喷涂。对于氧化物陶瓷可采用水稳等离子喷涂,其能量密度高,燃烧稳定,喷涂效率高。
3、等离子喷涂制备溅射靶材研究现状及发展趋势
随着等离子喷涂技术的发展,采用等离子喷涂法在基底上沉积出一定厚度的靶材材料已经成为可能。由于等离子体温度很高,高功率可调,几乎对所有的陶瓷、金属、金属化合物都可以进行喷涂,形成各种常规方法
难以制备的不同成分的合金及非合金。目前被广泛用于缺损修复、高温、耐磨、腐蚀防护,各种功能涂层的制备。
通过分析等离子喷涂技术的特点及市场对各种种类繁多的溅射靶材材质以及形状的需求,采用等离子喷涂技
术制备溅射靶材已经完全具备了条件,尤其是制备高熔点脆性管状旋转靶及大尺寸溅射靶方面具有明显的优
势。如在管状不锈钢或其他材质的基体上喷涂靶材料沉积层,经过后期处理,即可形成管靶,在不锈钢板上
喷涂形成平面溅射靶等,这大大降低了溅射靶材的制造成本,在未来溅射靶材制备领域具有很大的潜力。
3.1 等离子喷涂制备溅射靶材的特点
(1)等离子喷涂过程中基体表面不带电,不熔化,喷枪与基体相对移动速度快,对基体的热变形影小,无
组织变化。可直接在基体上喷涂形成溅射靶材,并有可能进行重复喷涂,重复溅射利用,也可用于靶材的修
复;(2)高温等离子体几乎可熔化一切高熔点和高硬度的粉末材料,尤其适合制备高熔点脆性金属及陶瓷的
靶材;(3)通过采用真空密闭喷涂,通入还原性气体、惰性气体气体保护等方法,可获得氧含量低、杂质少
的涂层;(4)等离子喷涂高温高速,粉末沉积率高,沉积速度快,可在短时间内获得较厚的涂层。
3.2 国内等离子喷涂制备溅射靶材的研究现状
目前,对等离子喷涂制备溅射靶材的研究还处于起始阶段,各方面还都不成熟。中南大学解露等人采用型号
为DH-1080,最大功率80kW的等离子喷涂设备,在大气环境下,以氮气送粉,氮气冷却,在石墨芯模上喷涂
了厚度为5mm的纯钼镀层,初始致密度达到了89.7%,在1500℃,10MPa压力下热等静压处理1.5h,其致密度
达到92.5%。然后再经过1600℃,125MPa热等静压处理2h,致密度达到了97.3%。虽然该方法制备的钼制品并非溅射靶材
,并且尺寸也只有φ30mmx80mm,但该方法的成功为等离子喷涂制备大尺寸难熔金属溅射靶材提供了可能。他
们采用该方法制备的Mo-ZrC复合涂层厚度可达20mm,完全符合溅射靶材的厚度要求。
庄志杰采用离子喷涂法制备圆柱形大面积镀膜靶材,通过等离子热喷涂将单一金属或非金属材料喷涂在衬管
上形成具有一定厚度的溅射靶材,结构简单,性能可靠。西北稀有金属材料研究院扈百直等人¨采用等离子
喷涂在经过预处理的基体上制备了氧化铌溅射靶材,靶材厚度可达12mm,密度为4.6-5.2g/cm3,其靶材的
长度和直径几乎不受限制。
3.3 等离子喷涂制备溅射靶材中存在的问题
虽然等离子喷涂在溅射靶材制备方面潜力巨大,但同时该方法也存在一个重要缺陷,那就是喷涂组织的多孔性。以热喷涂管靶为例,其显微组织为圆饼状扁平细晶粒,晶粒取向平行于旋转轴方向,靶材内有大量微米
级孔洞,靶材整体孔隙率高达5%~20%。在不锈钢管上采用等离子喷涂法,形成Mo、Nb、Si、Si-A1、Cr、
A1一Zn、TiO等材质的靶材,其相对密度达到85%~95%以上,厚度由几毫米到几十毫米,根据材质不同,
靶材纯度一般在99.5%~99.9%之间。而组织的疏松多孔,容易吸附杂质、湿气等妨碍溅射过程中高真空的
迅速获得及真空度的稳定,并且导致在溅射过程中,靶材溅射表面瞬间高温使松散颗粒团状掉落,污染被镀
件(玻璃)表面,影响镀膜质量和镀膜产品的合格率。因此,组织的多孔性极大的限制了等离子喷涂制备溅射
靶材的发展,使这些靶材大多只能在对靶材致密度要求不是很苛刻的领域应用,如卫浴、手机、五金、建筑
、节能玻璃等装饰性的镀膜上。
目前,解决等离子喷涂溅射靶材致密性差的方法主要有后期的热等静压致密化及压力加工法,如将等离子喷涂靶材进行轧制或锻造,以进一步提高靶材的致密度。
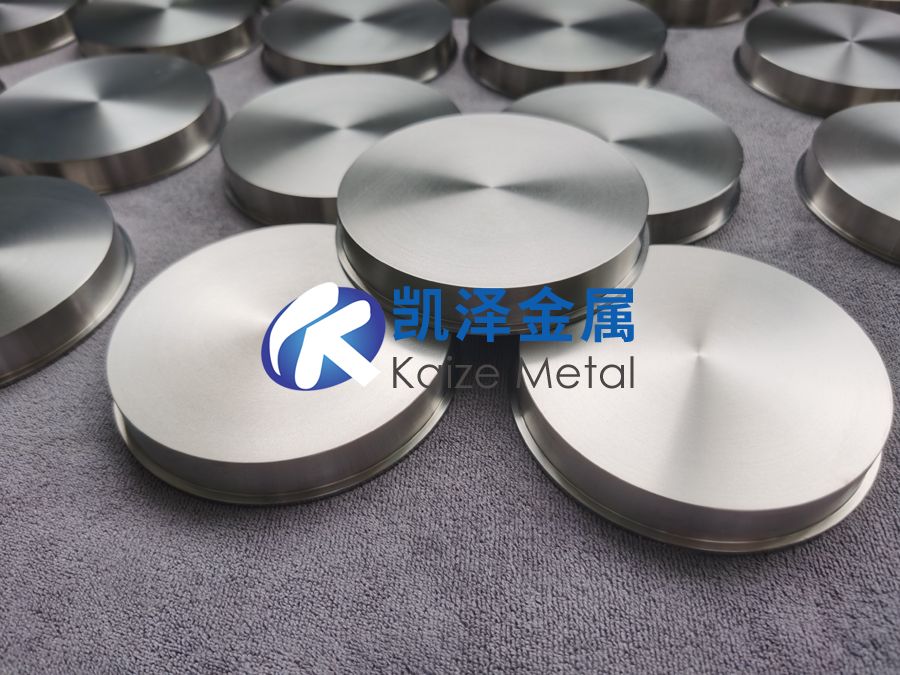
另外,若在大气环境下喷涂,靶材表面和空气中的O2和N2等气体大面积接触,会产生大量的氧化物和氮化物杂质,即使是真空等离子喷涂技术,也不能完全避免合金靶材中氧化物和氮化物的产生。因此,喷涂靶材在
溅射前必须用隔离的前级泵除去表面吸附气体。而相对来说,熔铸制靶技术很容易通过熔渣反应防止金属的
氧化和氮化,从而得到极低氧含量的纯金属或合金靶材。
3.4 等离子喷涂制备溅射靶材发展趋势
为提高溅射效率和靶材利用率,大尺寸靶材增多,旋转管状靶材被越来越多的采用。为适应不同的应用要求
,不同成分的合金金属、化合物靶不断涌现。随着技术发展和制备低成本的驱动,采用等离子喷涂制备靶材的种类在不断增加,范围在不断扩大。
随着等离子喷涂设备的发展和应用技术的提供,制备靶材组织密度较差、纯度较低的缺点也会随着技术进步
不断得到改善,该技术的适用材料范围广以及低成本的优点会日益凸显出来,必将在靶材制备领域获得更广泛的应用。
4、结语
等离子喷涂技术仍需进行以下两方面的研究:一是合理选择喷涂工艺,优化工艺参数,改善粉末受热和熔化
状态,减少环境对高温离子的污染和氧化,形成性能优良的涂层。二是进一步研究涂层形成机理、孔隙形成
机理,寻求消除或减少孔隙率的办法,进一步研究涂层与基体的结合机理,提高涂层强度。
可以预见,随着等离子喷涂技术的发展,可以引起溅射靶材制备技术的重大变革,仅需要更换成型粉末和工
艺参数就能够制备范围广泛的各种材料的大型平面和旋转管靶。
在材料成型领域,由表面技术发展而来的等离子喷涂成形技术,与喷射成形技术相比应用范围更大,更有优
势,可对高熔点金属、金属化合物、陶瓷等材料进行高速喷涂成形,并且可能作为制备复合材料一个发展方向。
参考文献
[1]王大勇,顾小龙.靶材制备研究现状及研发趋势[J].浙江冶金,2807,II(4):I一9.
[2]张青来,贺继弘.溅射靶材综述[J].上海钢研,2002,(4):30-40.
[3]安耿,李晶,刘仁智,等.钼溅射靶材的应用、制备及发展[J].中国钼业,2011,35(2):45-48.
[4]赵嘉学,金凡亚.常见磁控溅射靶材利用率及其计算方法的探讨[J].核聚变与等离子体物理,2007,27
(1):66-72.
[5]张永清,阴生毅,严秀峰,等.离子喷涂NiCrBSi+Ni/A1复合涂层的设计及应用[J].表面工程,1996,
(1):36-39.
[6]赵秋颖,贺定勇,蒋建敏,等.微束等离子喷涂Mo涂层[J].中国表面工程;2009,22(6):68-71.
[7]周静,韦云隆,张隆平,等.等离子喷涂耐磨涂层及热障涂层的新进展[J].表面技术,2001,30(2):23
-28.
[8]汪刘应,王汉功.多功能维弧等离子喷涂技术与应用[M].北京:科学出版社,2010:1-2.
[9]王振民,黄石生,薛家祥.等离子喷涂设备的现状与进展[J].中国表面工程,2000,13(4):5-8.
[10]刘曦.活塞环表面的等离子喷涂[J].车用发动机[J],1996,(o4):34-37.
[11]戴达煌,周克崧,袁镇海,等.现代材料表面技术科学[M].北京:冶金工业出版社,2004:129-141.
[12]陈丽梅,李强.等离子喷涂技术现状及发展[J].热处理技术与装备,2006,27(1):40-45.
[13]解露,熊翔,王跃明,等.热等静压对等离子喷涂成形钼制品的影响[J].中南大学学报(自然科学版),2011,40(10):3009-3014.
[14]谭政,夏光明,熊翔,等.ZrC对等离子喷涂成形钼制品的影响[J].金属材料与冶金工程,2012,40(3):3-7.
[15]庄志杰.以等离子喷涂制备圆柱形大面积镀膜靶材及方法:中国,201110256260[P].2011.
[16]扈百直;胥小勇,刘孝宁,等.一种氧化铌旋转靶材及其制备方法:中国,201210553666[P].2012.
相关链接