半导体工业用靶材是在半导体材料制备中用于薄膜沉积的原材料,在物理气相沉积(PVD)、化学气相沉积(CVD)等技术中起关键作用,通过溅射技术将高纯度金属或合金材料精确沉积在硅晶圆上形成薄膜层,实现芯片内部微型晶体管连接与信号传递。其主要类型包括金属靶材(如铝靶材用于传统互连层、铜靶材适用于先进制程互连层、钛靶材作扩散阻挡层、钽靶材用于高端芯片屏蔽层、钨靶材用于存储器、钴靶材起接触作用)、合金靶材(如钨钛合金靶材作接触层材料、镍铂合金靶材起接触作用)和化合物靶材(如砷化镓靶材用于高频率高功率电子器件及光电器件、氮化镓靶材用于光电器件、锗靶材用于红外光学及光纤通信、硒化锌靶材用于特定光电领域)。半导体靶材性能要求严格,需具备高纯度(通常达 5N5 以上,即 99.9995%)以避免杂质影响薄膜电学性能及导致晶圆短路等问题,高精度尺寸(控制直径、厚度等偏差)以确保薄膜厚度均匀一致,以及良好组织结构(均匀致密、无气孔裂纹偏析等缺陷)以保证溅射速率稳定和薄膜质量。以下是凯泽金属针对半导体工业用靶材的全维度纵深分析,涵盖主流靶材类型、关键性能、技术挑战及未来趋势:
一、定义与核心作用
术语 | 描述 |
半导体工业用靶材 | 用于物理气相沉积(PVD)或溅射工艺的高纯度金属或合金材料,通过离子轰击形成纳米级薄膜,实现导电、绝缘、扩散阻挡等功能,是半导体制造的核心材料之一。 |
二、主流靶材类型与特性对比
靶材类型 | 核心成分 | 关键特性 | 主要应用场景 |
钛靶(Ti) | Ti(纯度≥99.995%) | 低电阻率,优异附着力,形成TiN扩散阻挡层 | Cu互连层、DRAM电容器电极 |
钽靶(Ta) | Ta(纯度≥99.99%) | 高熔点(3,020°C),化学惰性,生成TaN/Ta₂O₅绝缘层 | 5nm以下节点扩散阻挡层、高k介质 |
铝靶(Al) | Al(纯度≥99.999%) | 低电阻(2.65 μΩ·cm),易加工,用于传统互连 | 逻辑芯片互连、功率器件电极 |
钴靶(Co) | Co(纯度≥99.98%) | 低界面电阻,抑制电迁移,适配先进制程 | 7nm以下节点Cu互连封盖层、触点金属化 |
钨靶(W) | W(纯度≥99.95%) | 高熔点(3,422°C),抗电迁移,用于高深宽比结构 | 3D NAND字线、通孔填充 |
钼靶(Mo) | Mo(纯度≥99.95%) | 低热膨胀系数(4.8×10⁻⁶/K),适配玻璃基板 | 显示面板TFT电极、OLED阳极 |
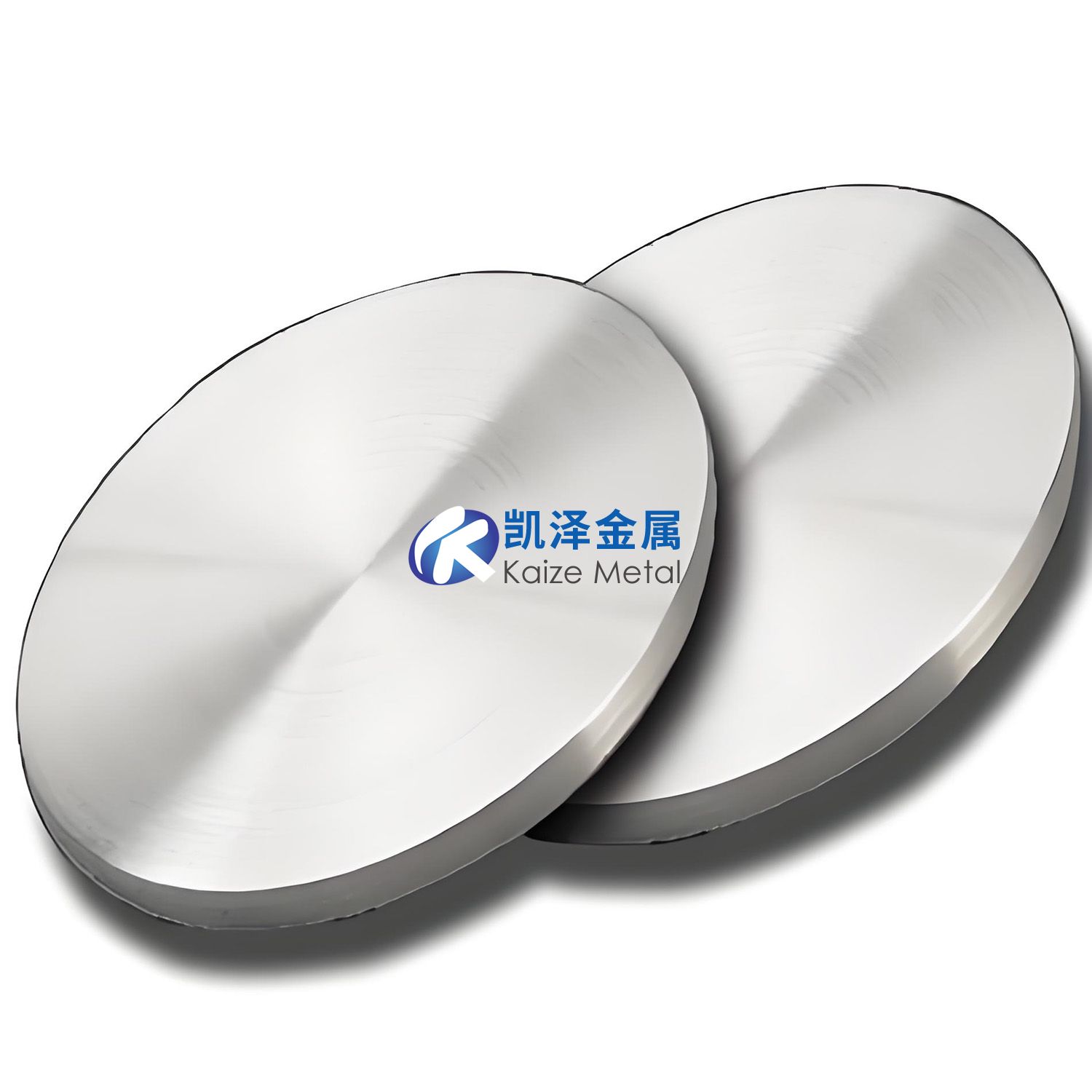
三、关键性能指标与半导体需求
性能参数 | 半导体行业要求 | 典型靶材达标示例 |
纯度 | ≥99.999%(5N5) | 钴靶(Fe<0.5 ppm,Ni<0.3 ppm) |
晶粒尺寸 | ≤50μm(均匀性±10%) | 钛靶(EBM熔炼+热等静压,晶粒尺寸30-50μm) |
密度 | ≥98%理论密度 | 钽靶(HIP处理后密度16.6 g/cm³,理论值16.69 g/cm³) |
缺陷控制 | 表面粗糙度Ra≤0.02μm | 铝靶(电解抛光+超声波清洗,Ra=0.015μm) |
四、制备工艺与核心技术
工艺环节 | 关键技术 | 典型设备/方法 |
熔炼提纯 | 电子束熔炼(EBM)去除低沸点杂质,真空自耗电弧炉(VAR)细化晶粒 | 真空电弧炉(氧含量≤50 ppm) |
成型加工 | 热等静压(HIP)消除孔隙,精密轧制控制晶粒取向 | 等静压机(压力≥150 MPa,温度1,200°C) |
绑定技术 | 钎焊(Ag-Cu-Ti焊料)或扩散焊,确保靶材-背板热导率>200 W/m·K | 真空钎焊炉(温度800-950°C) |
表面处理 | 镜面抛光(金刚石研磨液)+等离子清洗,降低颗粒污染 | CMP设备(去除率≤0.1μm/min) |
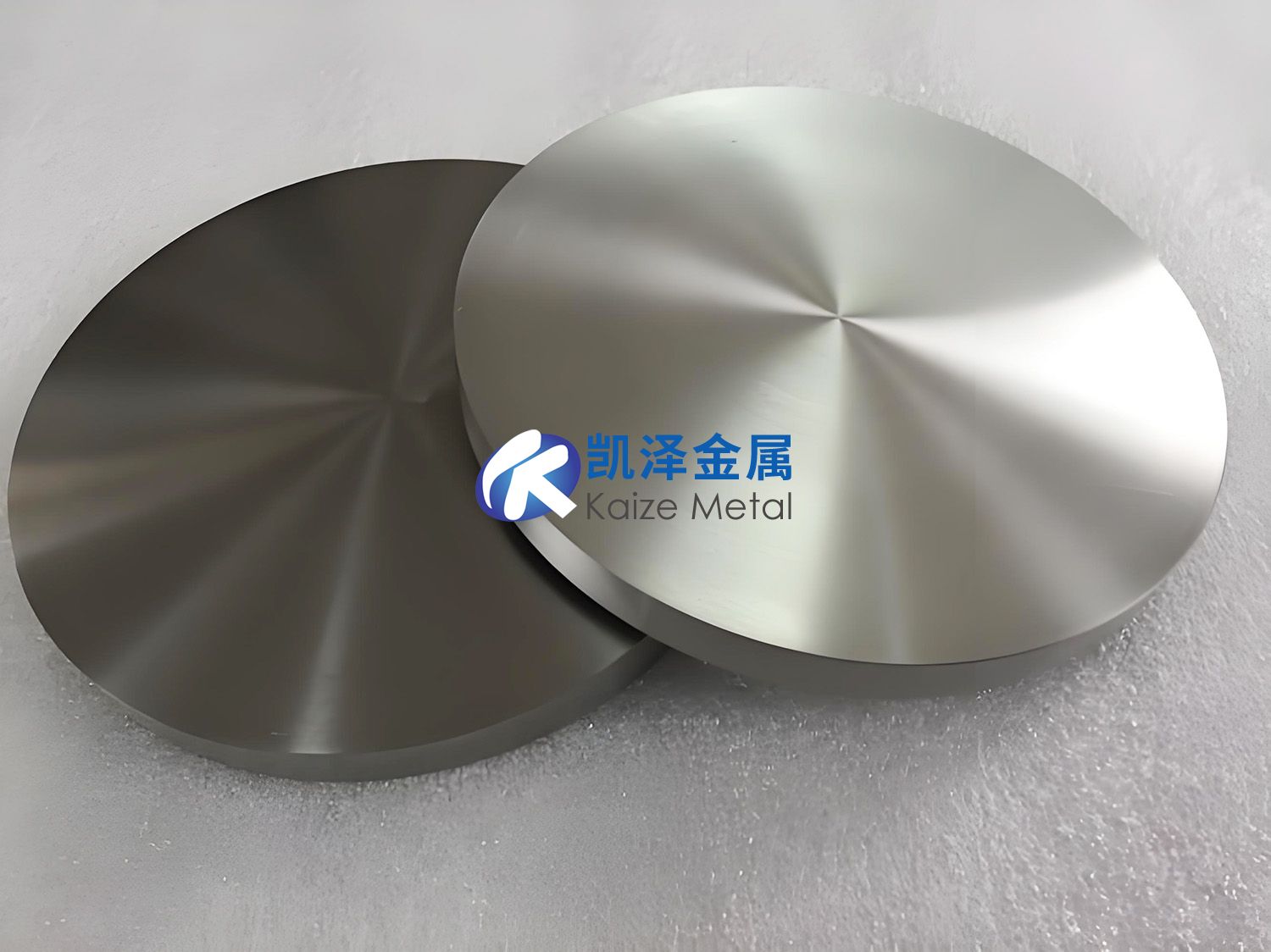
五、执行标准与质量控制
标准类型 | 国际标准 | 核心要求 |
纯度标准 | SEMI F47 | 金属杂质总量≤10 ppm,特定元素(如U、Th)≤1 ppt(用于先进制程) |
晶粒取向 | ASTM E112 | 晶粒度评级G≥7(晶粒尺寸≤32μm),各向异性指数≤1.2 |
缺陷检测 | SEMI M73 | X射线检测孔隙尺寸≤10μm,数量≤3个/cm²;表面颗粒≤0.1μm,密度≤10个/㎡ |
六、技术挑战与前沿攻关
挑战类型 | 具体问题 | 创新解决方案 |
薄膜均匀性 | 3D结构台阶覆盖率<80%(深宽比>10:1) | 高功率脉冲磁控溅射(HiPIMS),提升离子化率至90%以上 |
界面缺陷 | TiN/Cu界面粗糙度导致电阻增加20% | 原子层沉积(ALD)预镀0.5nm TiN种子层,结合溅射工艺 |
材料兼容性 | 钴靶在EUV光刻胶下的金属污染(>1E10 atoms/cm²) | 开发Co-W-B系合金靶,降低扩散系数50% |
成本控制 | 钽靶原材料成本占比>60% | 回收半导体废料中的Ta,纯度提至5N级,成本降低30% |
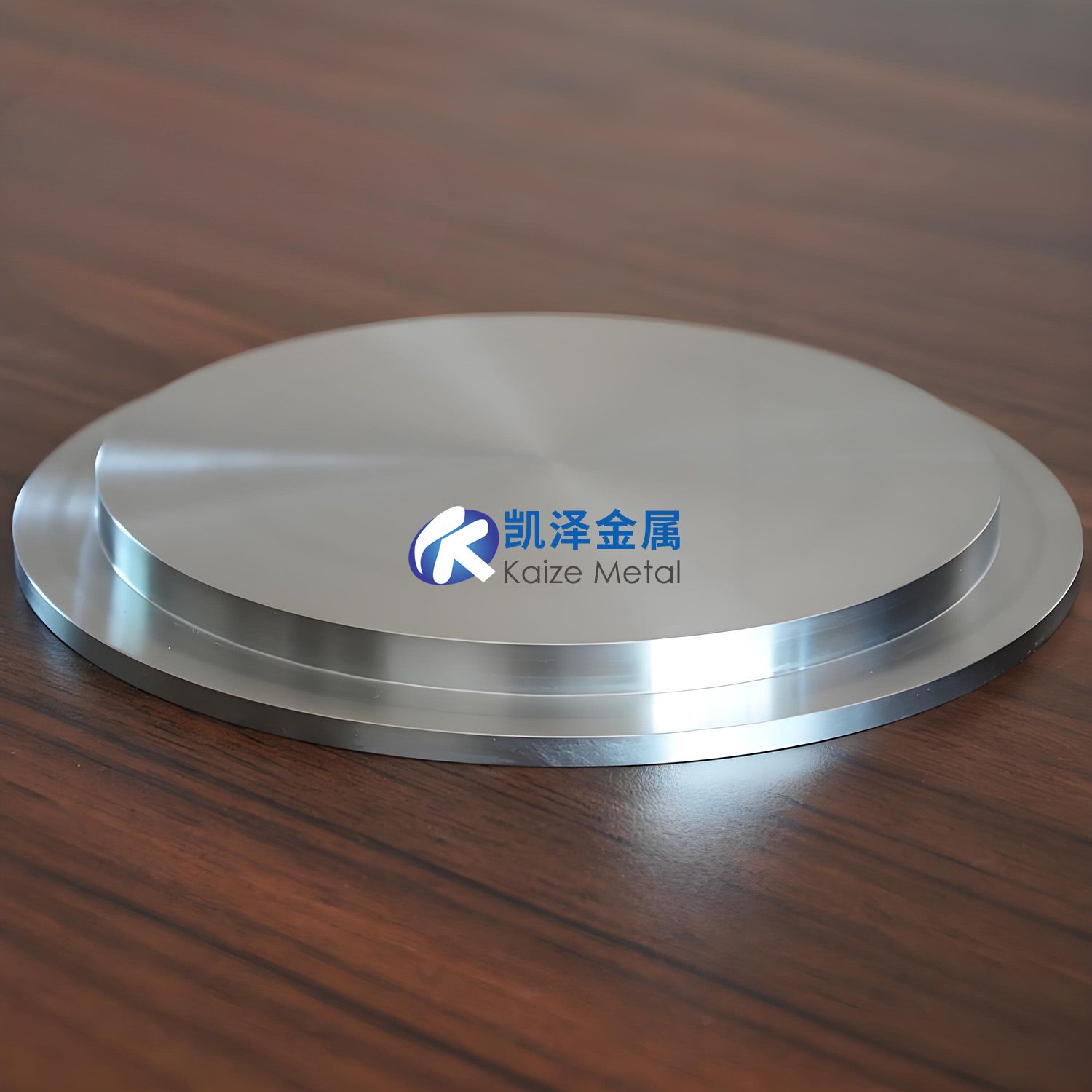
七、未来发展趋势
技术方向 | 发展路径 | 预期效益 |
新型合金靶材 | 高熵合金(如AlCoCrFeNi)用于超薄扩散阻挡层 | 薄膜厚度降至1nm以下,电阻率降低15% |
复合靶材 | Ti-Mo梯度靶(成分连续变化)适配多层薄膜需求 | 减少工艺步骤,生产效率提升40% |
绿色制造 | 靶材再生技术(利用率从30%提升至80%) | 降低半导体制造碳足迹30% |
智能化生产 | AI实时监控溅射等离子体状态,动态调整工艺参数 | 薄膜均匀性从±5%提升至±1% |
八、典型应用案例
应用场景 | 靶材方案 | 性能提升 |
3nm节点Cu互连 | Co/TiN复合靶(ALD+PVD协同) | 电阻降低18%,电迁移寿命延长5倍 |
3D NAND存储 | W-TiN叠层靶(深宽比>30:1) | 通孔填充无空隙,良率提升至99.9% |
EUV光刻掩模 | TaBN吸收层靶(Cr替代方案) | 光吸收率>90%,尺寸精度±0.1nm |
功率器件 | Mo/Al/Mo三明治靶(低应力电极) | 热循环寿命从1,000次提升至10,000次 |
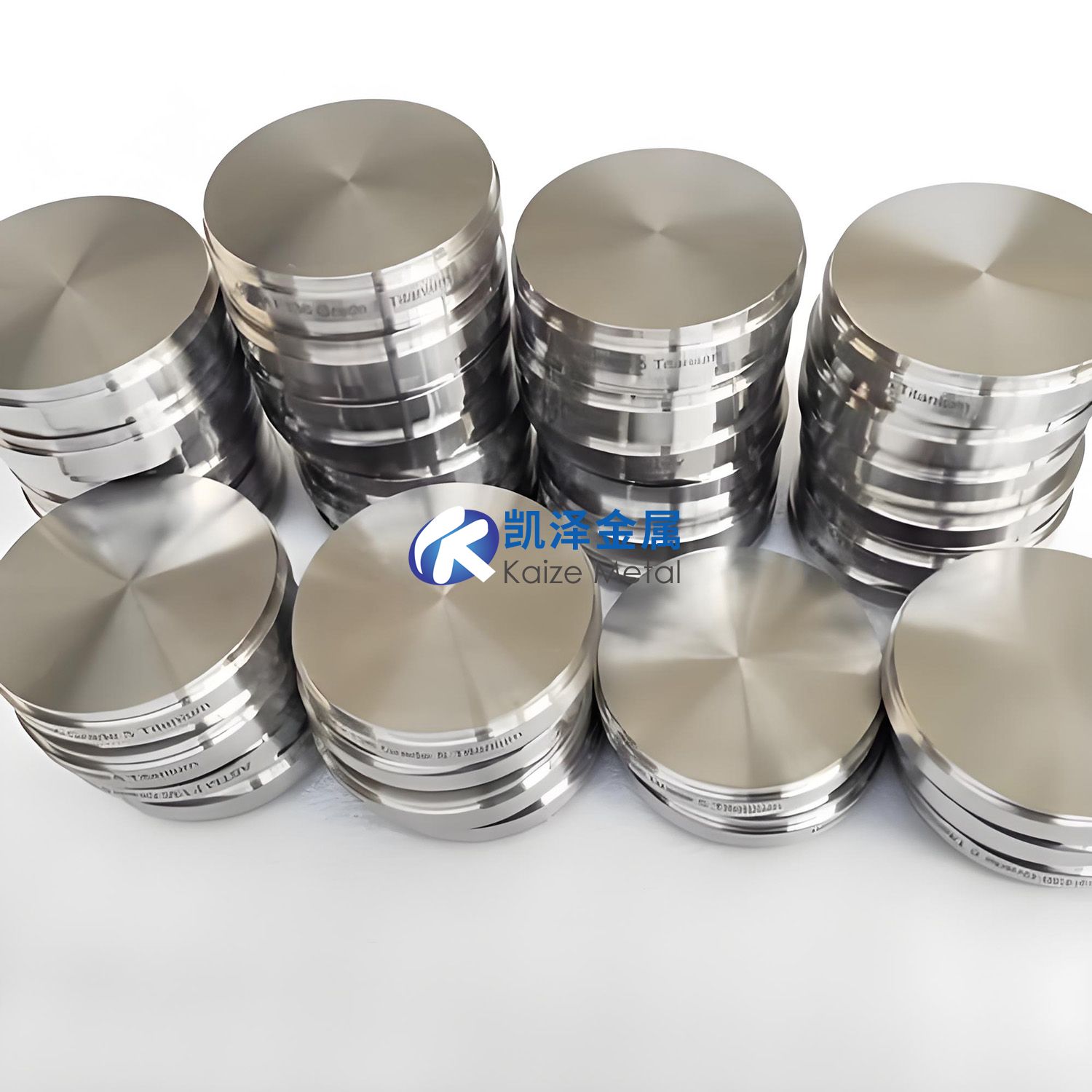
九、结论
半导体工业靶材正向超高纯度、纳米级精度及多功能复合化发展:
材料创新:高熵合金与梯度靶材突破传统性能极限;
工艺融合:ALD与HiPIMS技术结合解决3D结构镀膜难题;
可持续发展:靶材回收与绿色制造降低行业碳足迹。
未来3-5年,靶材技术将直接推动2nm以下制程、3D封装及新型存储器的商业化进程。
相关链接